‘UniMelt’ process to improve environmental footprint of implants
The agreement between US company 6K Additive and Australia-based Surgical Metal Recycling Pty Ltd (SMR) will seek to reuse end-of-life implants.
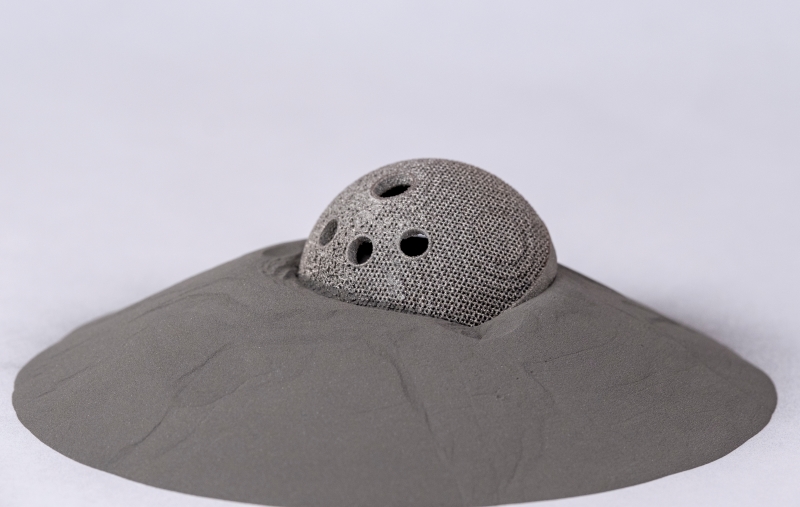
The companies will explore transforming the metals supply chain in Australia, including revolutionising the way surgical implants are treated at the end of their useful life.
Implants as part of surgical interventions has created a significant deposit of valuable metals and alloys within the human population.
When implants are removed for replacement or postmortem, limited options for reclaiming and reusing the materials exist.
The agreement between the two organisations will utilise used and out-of-spec implants, swarf and used metal additive manufacturing powder supplied by SMR and reprocess the material through 6K Additive’s UniMelt production-scale microwave plasma platform, initially in the US, later moving to Europe.
The resulting premium powders can then be used to create new parts through additive manufacturing, with the ultimate goal of the partnership to create new certified implants from existing parts through a sustainable and circular supply chain.
The collaboration will initially focus on titanium (Ti64) and will expand to incorporate cobalt chrome.
A study that quantified the environmental impacts associated with the production of printable metal powders, and specifically compared atomisation technology methods to 6K Additive’s process for titanium (Ti64), finds that 6K’s UniMelt process delivers, at minimum, 74% energy reduction and 78% carbon emission reduction from traditional processes.