Evolving metallography
Dr Lee Cobb MIMMM, UK Managing Director of Struers, reflects on the current and future state of automated metallography and welding.
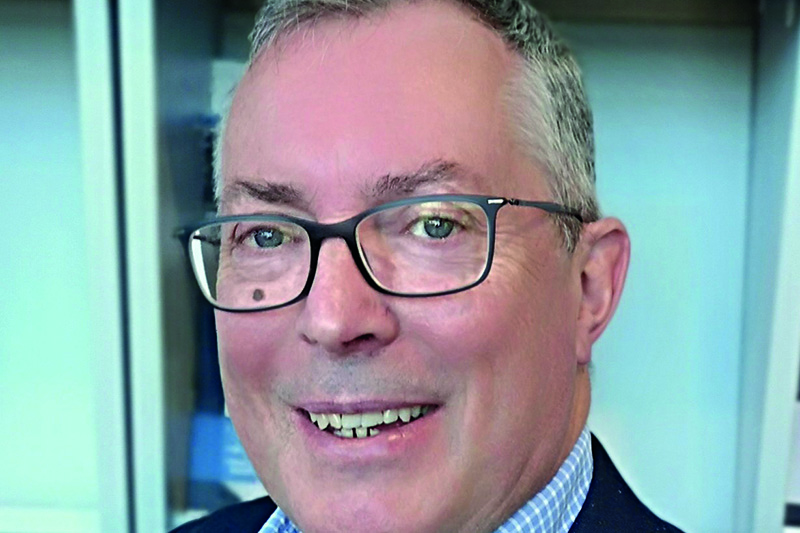
For a long time, the automotive industry has had a shortage of newly qualified and/or industry-trained metallographers to form part of their production quality check teams and workforce. Yet, as original equipment manufacturers face the demand for more battery-electric, hybrid and alternative fuel-source vehicles (hydrogen being the front runner), new testing requirements are being put in place to cope with powertrains, braking, steering systems and components, as new vehicles go from concept to production.
More testing results in the need for more sample preparation. With the current human resource landscape, it is essential for metallographic manufacturers to anticipate future use and requirements, and provide a means for easy-to-use, fully automated, metallographic equipment and turn-key solutions.
Any google search on ‘automation of metallography’ will produce a plethora of results – some focusing on the robotisation of processes using standard bench-top equipment, others on direct sample analysis and microstructure recognition using software algorithms.
Naturally, in the advancing age of artificial intelligence (AI), there is more interest in machine learning and the use of AI to provide consistent, learned interpretation of good and bad microstructure. By doing so, operators can effectively move away from any human influence and rely on a calibrated system that would provide traceability (regarded as the utopian vision for many manufacturers) and, perhaps more importantly, a means of operator-free report generation – leaving the metallurgist available for other duties, often related to system improvements and to allow time for prototyping and R&D.
Today, we have high-throughput industries already looking to automated sample preparation solutions to help them meet the demands of in-house testing regimes and of their customers. It is almost inevitable therefore that the automotive industry will head more towards this ‘black box’ solution – where the sample is simply passed onto the machine (or the robot collects it), and the full report and analysis (and exquisitely prepared sample) is handed to the operator at the end of the test cycle.
While the skillsets of the metallographer are required more than ever in the development of new materials and their application. It therefore seems reasonable to assume that there will always be the need for well trained, expert metallographers and metallurgists.
We have seen the precursor to this in the North East of England, with one of the large automotive manufacturers, by way of weld inspection and analysis. Right now, weld inspection is fundamental to keep joining technology working and in line with quality checks and requirements for production lines.
An example weld can be prepared fully automatically with the resulting sample only requiring inspection, measurement and/or analysis – or even more fundamentally, a pass or fail. The measurement is then typical of what is capable through software application via light microscopy.
In this example, the technicians are production operatives, not metallographers. A metallurgist will ultimately pass/fail the samples as they are reported on, but the specifics of metallography in terms of application know-how and material-based preparation selection are left to the machine.
We have seen weld inspection lines facilitated in this way for some time, and the current trajectory is for this to become more automated to allow the metallographers and metallurgists onsite to focus on other things.
In a robot-manned factory, sampling may be even better controlled, with the robot cutting the sample from a test coupon, almost akin to what happens in the printed circuit board and semiconductor industries today, where given the right control environment, a full tear-down of a production vehicle chassis and bodywork may ultimately not be required.
Think Philip K. Dick’s Minority Report – the Lexus factory as depicted in the Tom Cruise film may provide the ultimate, relatively non-dystopian vision of the factory of the future, with all metallography carried out by machine and supervised by the company metallurgist. Maybe. This even lends itself to the multiple-material test-house, where off-the-shelf, proven, preparation methods may be selected at the press of a button.
The IOM3 World Titanium Conference meeting this summer provided a great opportunity to listen to leading academics in their field and understand their needs and requirements going forward. It was nice to hear the same commentary on the consistency, speed and reproducibility provided by automation, but it was also satisfying to realise that there is always the need for the metallographer, materials scientist and metallurgist to help develop the methods and approaches we ultimately use for sample preparation, regardless of the route we adopt to get there.