Closing the loop for Nissan's global recycling systems
Nissan's first global model built using a 'closed-loop' recycling system for aluminium parts has hit the ground with the company's new 2021 Nissan Rogue.
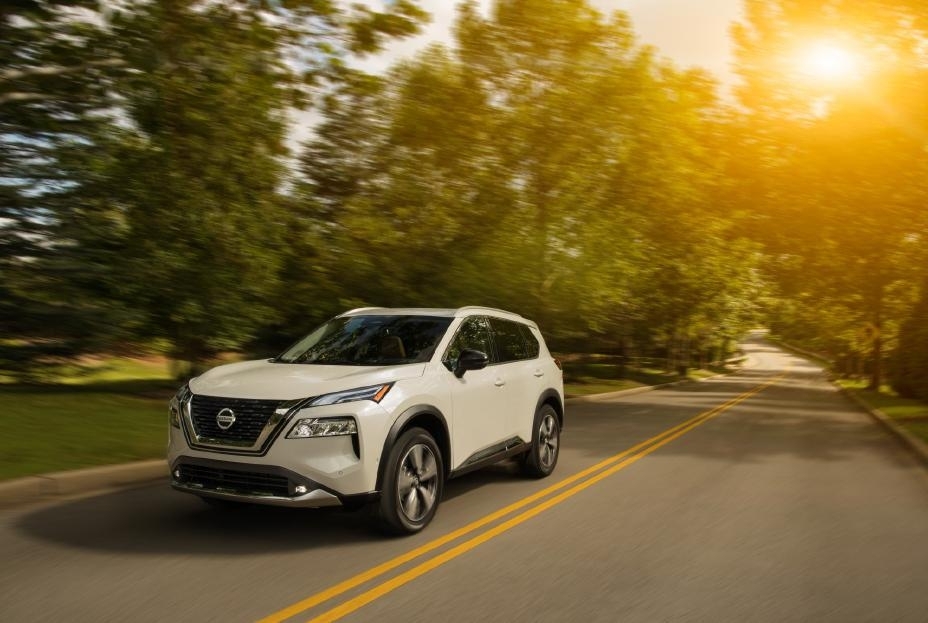
The system helps reduce CO2 emissions compared with using parts made with primary alloys from raw materials, according to the company. It also aims to promote the use of materials that don’t rely on newly mined resources, as well as the reduction of waste from factories.
The bonnet and doors of the 2021 Rogue are stamped from aluminium alloy, a material that reduces vehicle weight and helps improve fuel efficiency and power performance. The model is built in Kyushu, Japan, and Smyrna, Tennessee, USA.
To support the process, Nissan has collaborated with Kobe Steel, Ltd. and UACJ Corp. in Japan, and with Arconic Corp. and Novelis Inc. in the US.
At the core of the closed-loop recycling system is a large pneumatic conveyance system. As parts are stamped into shape, scrap material is shredded and extracted, keeping aluminium grades separate.
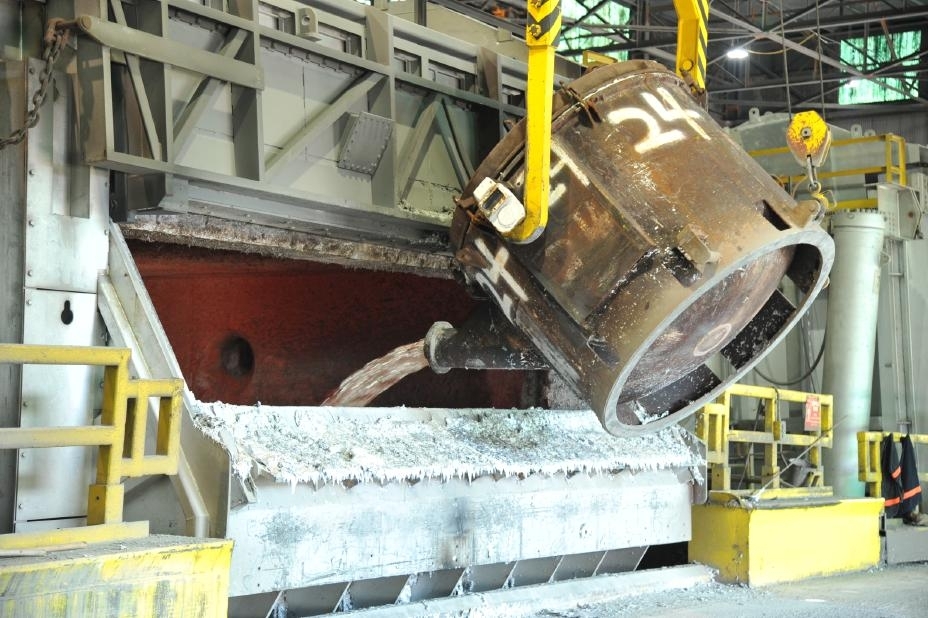
The separation ensures that Nissan can return high-quality scrap to suppliers. The suppliers turn the separated and reprocessed aluminium scrap into aluminium alloy sheets and redeliver them to Nissan for use in production.
The US-based Aluminum Association reports that recycling scrap aluminium saves more than 90% of the energy needed to create a comparable amount from raw materials. The organisation estimates that nearly 75% of all aluminium made is still in use.
Nissan aims to replace 30% of the raw materials used in cars built in 2022 with materials that don’t rely on newly mined resources, as part of the Nissan Green Program 2022.