Coral reefs inspire carbon dioxide sequestration in composite building materials
An electrochemical process sequesters carbon dioxide to create resilient, self-healing and fire-resistant mineral-polymer materials.
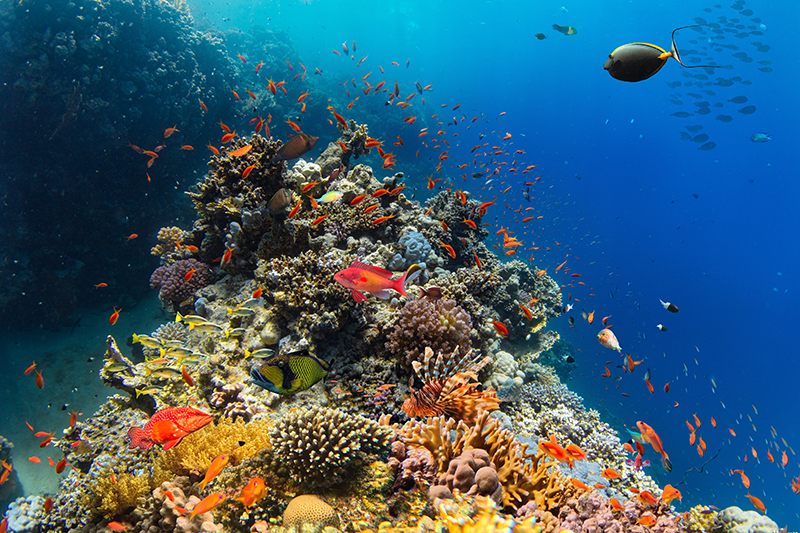
The team at the University of Southern California, USA, report that the resulting mineral-polymer composites demonstrate extraordinary mechanical strength, fracture toughness and fire-resistance.
Qiming Wang, Associate Professor of Civil and Environmental Engineering, says, 'Unlike traditional carbon capture technologies that focus on storing carbon dioxide or converting it into liquid substances, we found this new electrochemical manufacturing process converts the chemical compound into calcium carbonate minerals in 3D-printed polymer scaffolds.'
The paper – Towards negative carbon footprint: carbon sequestration enabled manufacturing of coral-inspired tough structural composites in npj Advanced manufacturing – claims, 'Compared to an existing method that utilises CO₂ to fabricate low/negative-carbon concrete, our method not only enables structures with designed microarchitectures but also features a 25-times higher carbon sequestration efficiency.'
In nature, coral builds aragonite skeletal structures known as coralites through biomineralisation – by sequestering CO₂ from the atmosphere through photosynthesis. Combining this with calcium ions from seawater, the coral precipitates calcium minerals around organic templates.
The team has 3D printed polymer scaffolds that mimic coral’s organic template from a Clear V3 resin. The printing of 25µm-thick layers takes 83 seconds to solidify. The polymer is then washed with acetone and air-dried for 24 hours at 25°C to remove any residual solvent.
The group then coats the scaffolds with a thin conductive layer of palladium of ~100nm, using a sputter coater. The coating enables electrochemical water splitting.
They connect the samples to electrochemical circuits as cathodes and immerse them in calcium chloride solution, with a 6V power supply. When CO₂ is added, a hydrolysis process occurs to form bicarbonate ions. The electrochemical water splitting around the cathode structure obtains hydroxide ions. Together, these react with the calcium to form calcium carbonate, which over six days fills the 3D-printed pores to create a dense mineral-polymer composite.
The group reports that scanning electron microscopy shows the minerals grow from the lattice’s inner surface and gradually extend to fill the pores. The thickness of the minerals increases until day four, when the pores are mostly filled, and the structure becomes a composite.
CT scanning shows that the process fills the lattice pores by more than 85% before the outer structure is mineralised.
A Life Cycle Assessment reports an uptake of 2,720kgCO₂/t, which is said to be higher than in carbon-negative concrete at 150kgCO₂/t and carbon-absorbing functional wood at 30-40kgCO₂/t.
The stiffness of the 3D-printed structure with the conductive coating has been found to increase after mineralisation by more than 500 times, the flexural strength increases around 50 times, and the shear strength increases by around 17.5 times.
The shear fracture toughness of the calcium-carbonate-mineralised composite is reported as 102 times higher than the calcium-carbonate mineral phase and 81 times greater than the polymer phase. Meanwhile, compared to natural coralite, the composite’s specific shear strength is 100% greater, while the specific shear fracture toughness is 600% higher.
Although the 3D-printed polymer scaffolds initially lack inherent fire-resistant properties, the mineralised composites reportedly maintain their structural integrity in experimental flame tests.
Wang says the composite has a natural fire-suppression mechanism of 30 minutes to direct flame exposure. When exposed to high temperatures, the calcium-carbonate minerals release small amounts of CO₂ that appear to have a fire-quenching effect.
In addition, cracked fabricated structures can be repaired by connecting them to low-voltage electricity.
The team has used the material to construct large-scale, load-bearing structures and a house model a few centimetres tall and wide, finding that it had a load equivalent to 176 times its own weight.