Rolls for hot rolling
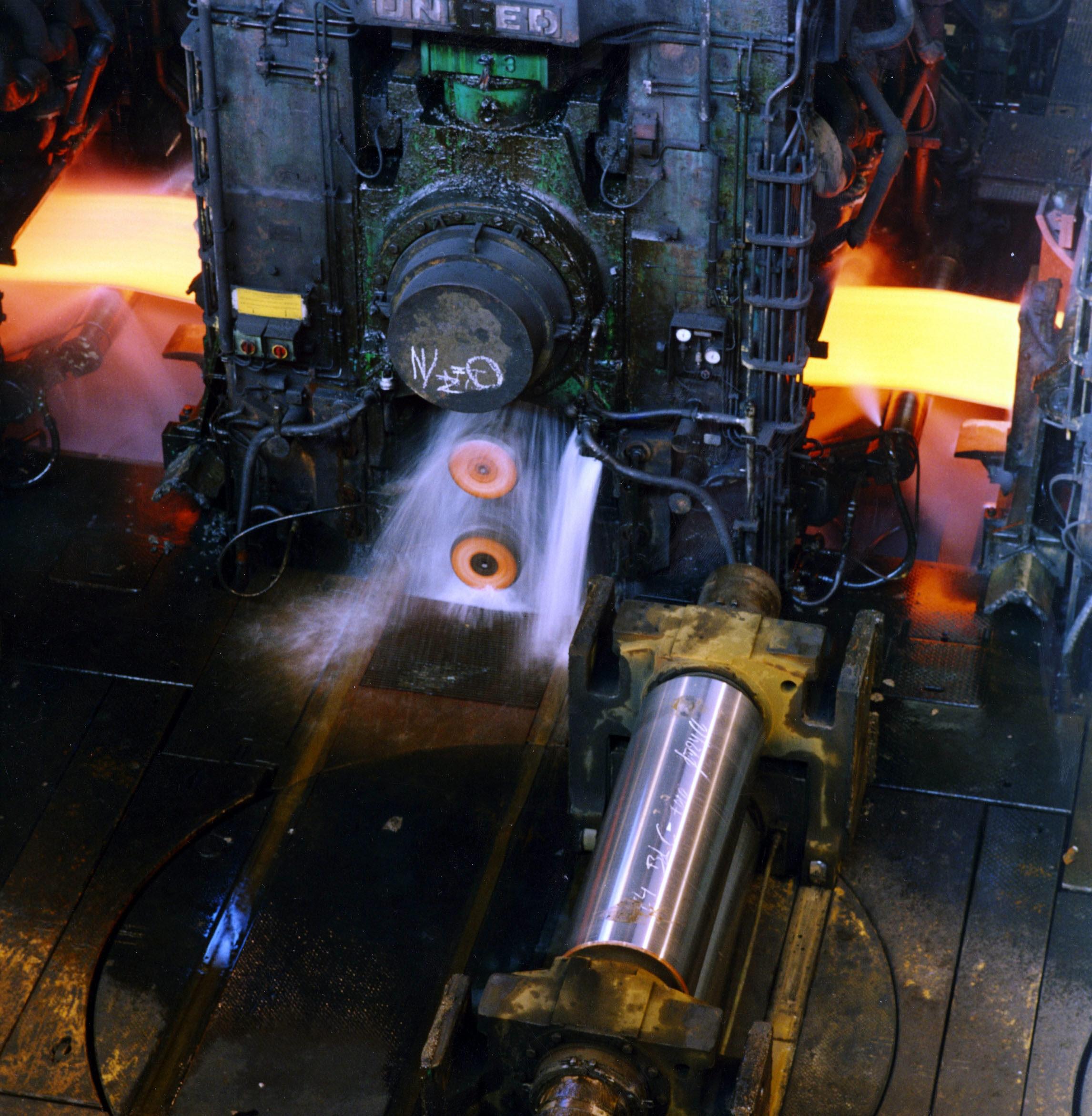
From the superb full conference programme scheduled for Rolls 6, we are now offering a selection of papers in a special series of Rolls for Metal Rolling Online Seminars. Presenters from research institutes and from the roll-making and roll-using industries will present the latest advances and new challenges in rolls technology developments, from scientific as well as industrial perspectives.
Four speakers from 3 continents will present developments and field experiences with advanced rolls for hot rolling applications, ranging from plate mills and hot mill roughing stands to early and late finishing stands. Each paper will provide a unique perspective, from varying viewpoints of roll manufacturers, roll users and research institutes, on establishing reliable rolls across the mills, roll damage modelling, and collaborative research for and implementation of advanced roll grades in hot strip mills.
Reliable Rolls for Hot Rolling of Steel
Presented by Christian Zybill, Walzen Irle
Reliability of rolls is a most important issue for customers involved in hot rolling of steel. IRLE Roll Foundry takes a multilayer approach to combine performance and reliability from the level of microstructure through the casting and manufacturing process up to an interactive customer service. This allows a high degree of adaption to the specific conditions in the mill. Furthermore, extraordinary dimensional accuracy and surface quality of the products are achieved. For the customer the TCO of the rolling process is reduced significantly.
A comparative discussion of the advanced materials will be done including performance and reliability data as a guide for the selection of an optimum roll.
Introduction of Centrifugally Spun Cast High Speed Steel Work Rolls in Hot Mills: A Tata Steel India Perspective
Increasing campaign length and reducing change over time without affecting strip surface quality are the key drivers for introduction of newer grades of work rolls in various hot mills of Tata Steel India.
Centrifugally Cast High Speed Steel Work Rolls were used for the first time in Tata Steel India. Along with the expectations came also a lot of doubts w.r.t. precautions to be used while using the new generation costlier rolls which had higher residual stresses than the previous ones.
Upgradation of the grinding equipment and roll testing equipment was also done.
Tremendous cost benefits like double campaigns without grinding and reduced roll wear scales was obtained. The paper encapsulates the journey undertaken by flat hot rolling mills of Tata Steel at Jamshedpur to absorb this new generation rolls and make them the backbone of a successful finishing mill roll fleet.
Damage modeling of work roll for hot rolling
Presented by Mario Boccalini Jr, Institute for Technological Research (IPT)
Further advances in the development of roll materials for hot rolling mills require deeper quantitative understanding of roll/strip interactions, combining real-time observations with physical and mathematical modeling of rolling operation, such that damage phenomena are recorded as a function of the thermo-mechanical loads acting on the rolls.
A collaborative project involving Gerdau Summit, Institute for Technological Research and University of São Paulo aimed at model the progressive damage of hot rolling roll based on physical and mechanical properties of the micro-constituents of the roll material, thus allowing to design materials with “engineered microstructure” for high performance hot rolling rolls. The overall frame of the project was presented in ROLLS 5 Conference 2015, in Birmingham.
The present work deals with results of damage modeling and experimental validation through pilot rolling mill, considering both mass loss and thermal cracking. Two alloys were used in the experimental rolls: hot worked H13 (quenched and tempered to 45 HRC) and cast Nb-bearing HSS (quenched and tempered to 54 HRC).
Each experimental campaign consisted of hot rolling four hundred AISI 1045 steel plates (15x100x250 mm), that is, about 1 km rolled. Five campaigns for each alloy were performed and, after each campaign, rolls were taken out the stand to measure the roll profile and the thermal crack density.
Comparison between simulations and the operation of the pilot rolling mill were performed, which contributed to a simple model to predict the occurrence of thermal fatigue based on three rolling mill operational parameters: reduction, roll speed and temperature of the rolled material. Additionally, further studies were conducted regarding the abrasive behavior of roll microstructures and on the effect of oxidation on the thermal fatigue behavior.
Cooperative research for late finishing stands’ roll grades - roll producers' knowledge meets customers' demands
Presented by Armin Paar, ESW
The development of highly sophisticated work roll materials requires expertise knowledge in the fields of metallurgy and material science. In the case of roll grades for the late finishing stands the metallurgical characteristics are complex as stable and metastable phases appear together in the microstructure. Indefinite-Chill roll grades (ICDP) consist of cementite and graphite embedded in a bainitic-martensitic matrix and may be supported by MC carbides in the case of carbide-enhanced ICDP grades. The last development step of graphitic HSS grades widens this field as more complex carbides such as M2C and M6C were introduced into the metallurgical system and still a well-balanced microstructure has to be achieved.
Additionally the application in the rolling mill plays an important role in the development of roll grades which meet the customers’ demands. The wear resistance is the most important factor for work rolls but it is well-known that also other criteria are not less important such as the surface quality and the sensitivity against mill incidents. Especially these two factors require a close cooperation between the work roll manufacturer and the customer, including the rolling mill and the roll shop. To improve the work roll surface it is important to understand the mechanisms of work roll degradation which may vary from mill to mill. The sensitivity against mill incidents has to be split into two factors, the resistance against the crack initiation and the resistance against the propagation of existing cracks.
ESW’s cooperative research strategy aims to cover all fields of work roll materials development. Fundamental research is carried out together with universities and other research institutes and based on these results the materials development is carried out. For the development of roll grades with highest demands, close cooperation with customers plays an important role where the specific factors of the application in the mill, roll testing and roll grinding are included.
This paper presents the development of selected work roll grades for the late finishing stands such as VANIC (modified ICDP) and VANIMO (graphitic HSS) including examples of fundamental research as well as the applications in the rolling mills.
Confirmed Speakers
Event Details
- The webinar will be hosted on Zoom
- The session will be recorded and all registrants will receive a link to watch on-demand.
- The session will take place 13:00 - 15:00 BST