Modelling & Roll Life Optimisation
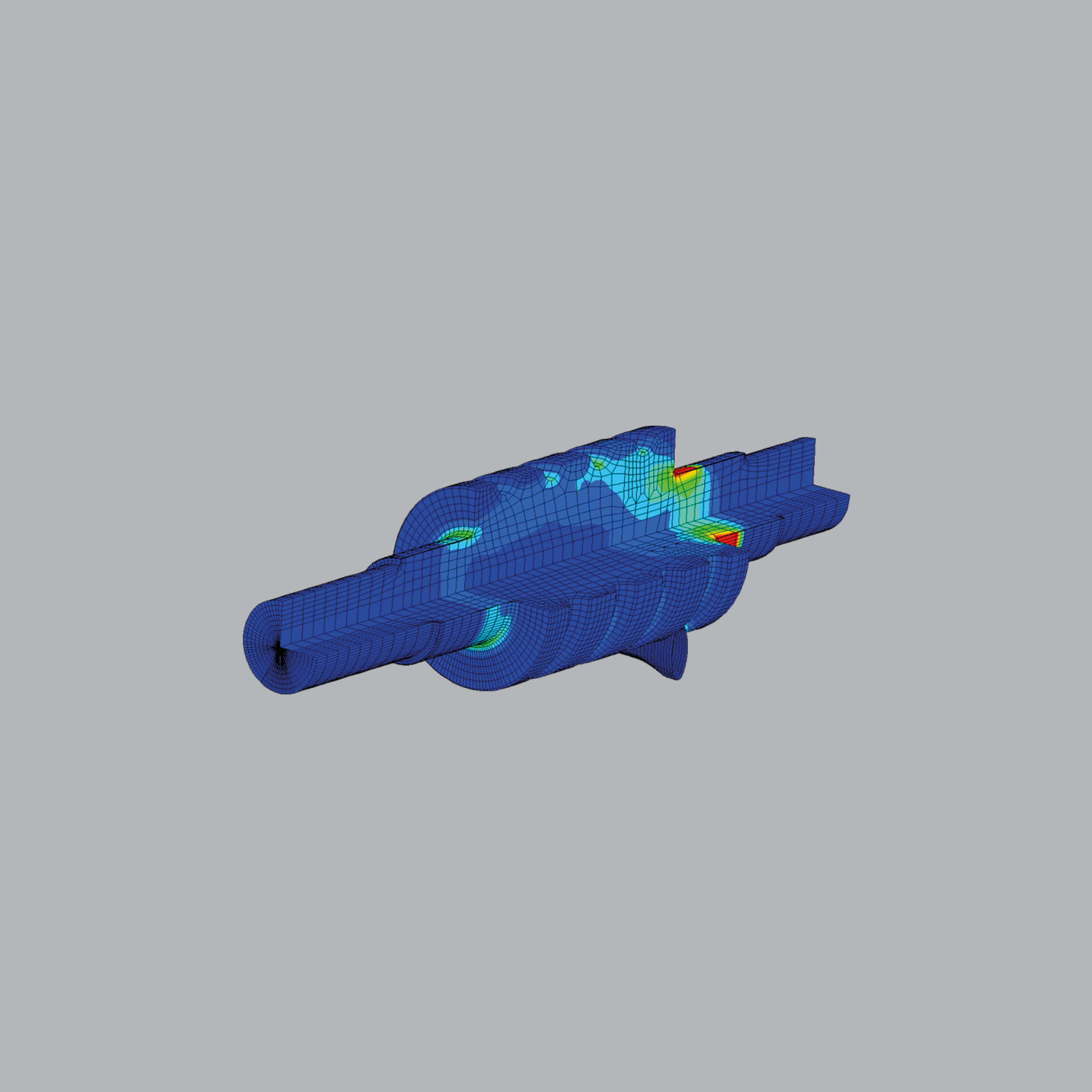
From the superb full conference programme scheduled for Rolls 6, we are now offering a selection of papers in a special series of Rolls for Metal Rolling Online Seminars. Presenters from research institutes and from the roll-making and roll-using industries will present the latest advances and new challenges in rolls technology developments, from scientific as well as industrial perspectives.
Four speakers from the roll manufacturing and roll using industries and from a research institute will present computational methods and modelling results to optimise the life and value-in-use of rolls in various rolling applications. The first paper focuses on long product mill rolls, presenting a new theory to predict the minimum safe working diameters, enabling optimised roll grade selections. In the second paper, a complex design approach is proposed aiming at back-up roll life optimisation. The third paper will feature an FE-model to optimize the roll life in reversing roughing stands. The final paper deals with hot strip finishing mills, showing examples of a numerical approach to calculate the effects of strip and roll cooling parameters and roll material properties on the in-use behaviour of spun-cast and additive-manufactured work rolls.
The selection of Roll Grades for Long Product Reversing Rolls Through Accurate calculation of their discard diameters
Presented by Steve Moir, Kaida Roll
Long Product Mills have hitherto been less predictable than their strip counterparts in terms of their minimum working diameter of the roll, known as the discard diameter. This is due to the wide variation in the profile along the barrel, where these rolls usually break near to the centre of the barrel at the narrowest diameters, but not necessarily as there is also the parameter of the rolling load.
This paper details well established principles that have enabled the calculation of the minimum barrel diameter of long product rolls; dependent on the barrel profile, the roll loading position, the rolling load and the separation distance of the initial roll centres. Once this information has been obtained it is possible to select the most suitable roll grade by making use of the working range from maximum to discard diameter, but at the same time maximising the wear resistance. Wear resistance has an inverse relation to strength, for example, for alloy cast steel rolls. Thereby it is now possible to replace low carbon forged steel rolls with harder wearing alloy cast rolls for clear cost and roll wear benefits for the Long Product Mill.
New Advances and Challenges of Backup Rolls Service Life
Presented by Konstantin Redkin, Whemco
Development of new advanced high strength steel (AHSS) grades and rolling practices continue to challenge roll manufacturers. Increased mill loads and extended rolling campaigns require roll materials to keep pace with ever changing rolling technology. In this study developed finite element analysis (FEA) of the BackUp Rolls (BUR) to predict microstructural evolution and associated transformational and thermal stresses will be discussed. Proposed 3D FEA enables to study the interaction between residual stress in BUR and actual mill loading scenarios. The model is a valuable tool used to highlight potential BUR design shortcomings given specific mill loading conditions.
Predicted residual stresses in BUR, which resulted from proprietary differential hardening heat treatment, were incorporated into 4-HI mill loading model, using actual mill operational data. Localized alternating stress ranges were predicted throughout the BUR. The results show a clear interaction between alternating mechanical mill loads with residual stress profile. Revealed complex interaction between internal pre-strain conditions and externally induced stresses is typically not considered when developing BUR quality specifications. Understanding complex volumetric microstructural and residual stress evolution and modern mill loading interaction is of utmost importance in order to assess required backup roll properties, such as: fatigue endurance and damage tolerance. Novel results facilitate development of specifications and inspection criteria for the rolls being in service under acknowledged loading conditions.
Proposed complex design approach provides the roll manufacturer with critical information about the localized magnitude of pre-loaded internal residual stresses for BUR or work rolls (WRs), so that appropriate non-destructive testing/evaluation can be conducted. Spatial and path depended material properties in large section BUR were studied through computational materials and simulation model based definition and validated via mechanical testing. The relative effect of the key-operating parameters was studied by isolating specific unfavorable loading conditions and considering metallurgical attributes of the rolls. The results of the work were successfully used in the development of a pouring practice to improve roll ingot’s quality combined with heat treatment optimization, where the residual stresses were minimized without scarifying mechanical properties and increasing fatigue endurance.
Development of a FE-model to optimize the roll life in reversing roughing stands
Presented by Sebastien Flament, CRMGroup
Rolls in hot rolling mills have to withstand harsher and harsher conditions throughout the decades. In the early 2000’s, problems of bonding zone fatigue (before reaching scrap diameter of the work rolls) started to occur in some mills. Since then, year by year, increasing fatigue issues were encountered in reversing roughing mills worldwide. Longer rolling campaigns, inadequate backup or work roll maintenance, harder steel grades or increased throughput by reduced amount of passes to achieve the same thickness may explain the higher amount of fatigue occurrences.
A model was developed to predict stresses at the contact surface between the work and backup rolls as well as at the shell–core interface of the work roll. The development was pushed further to define an optimised situation both for roll manufacturer and users to withstand the given rolling conditions in a mill. Indeed, the current practice of the roll users is to request an increased total work roll shell thickness to ensure a determined roll life. However, some limits have been reached regarding the total shell thicknesses leading to some manufacturing issues especially in the field of residual stresses or core material properties.
This paper will illustrate a wide range of fatigue problems encountered in reversing roughing stand and the model outcomes to optimise both the roll use and design to withstand the harsher conditions. The model takes into account work and backup roll geometries, chamfer design, campaign length, wear profiles (work and backup rolls), strip width and rolling forces.
A numerical approach on the effect of strip chilling and high turbulence roll cooling on spun-cast versus additive-manufactured work rolls of hot strip mills.
Presented by Stamatis Kiakidis, Tata Steel
Rolls are key assets for hot strip mills (HSMs), with major impact on mill availability, daily mill and roll shop operations, product quality assurance, and high associated costs. A typical HSM stand has work rolls (WRs) and backup rolls (BURs). Among them, the WRs of the finishing stands of a HSM have the highest impact. The temperature distribution in the WRs, along with its stress field, determine to a great extent the roll serviceability. Within the content of this study, a simulation tool (ASTRO) was developed, capable of providing the thermomechanical state of the WRs during hot rolling.
ASTRO is a numerical model, consisting of a thermal and a stress part. The thermal part calculates the temperature evolution at the WR during a rolling campaign, via a finite differences formulation. Afterwards, the stress part calculates the internal stresses at the WR, taking into consideration the already calculated temperature profile, and all the mechanical loads imposed at the circumference of the roll. This latter part is based on the finite elements theory. Being a two dimensional (2D) model, ASTRO simulates only the middle section of the stand assembly, including the strip, the work rolls, the backup rolls, the roll cooling and the strip chilling systems. The attached figure illustrates a simplification of the rolling stand assembly. The meshed segment of the strip/roll geometry, along with the blue regions of the cooling system, are the features considered during calculations.
Confirmed Speakers
Event Details
- The webinar will be hosted on Zoom
- The session will be recorded and all registrants will receive a link to watch on-demand
- The session will take place 13:00 - 15:00 BST