Taking on the triple-threat to metals in 3D printing
Engineers in the US claim to have mitigated three types of defects in parts produced by laser powder bed fusion (LPBF) – a form of additive manufacturing.
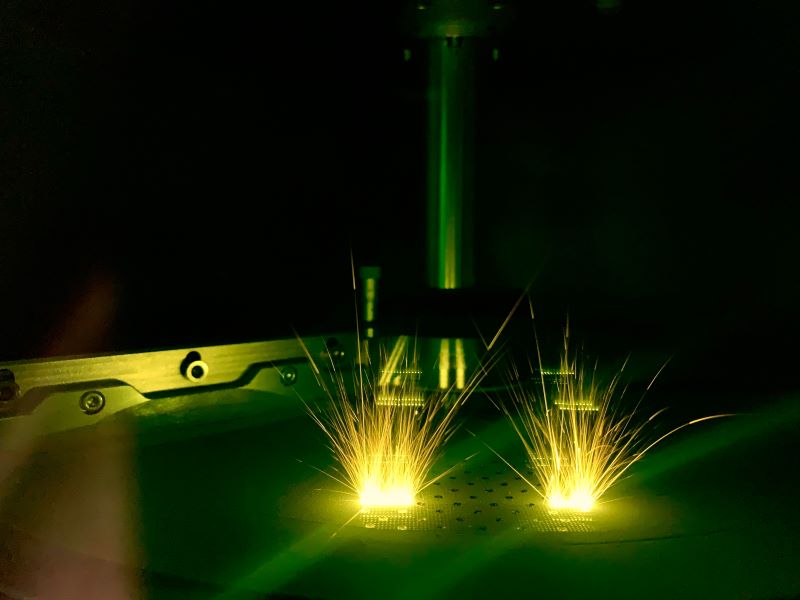
LPBF holds promise to produce metal parts with complex shapes that are difficult or impossible to create using conventional methods.
However, metal parts created through this process too often contain defects relating to pores, surface fluctuations and spatters that compromise the finished component’s reliability and durability, and make the process unusable in safety-critical industries.
LPBF uses a high-energy laser beam to melt and fuse thin layers of metal powder, constructing layer-by-layer from the bottom up. It is usually conducted with a Gaussian-shaped beam.
Professor Lianyi Chen at the University of Wisconsin-Madison says, 'We found that three types of defects…can be mitigated simultaneously by tuning the spatial distribution of laser energy using an innovative ring-shaped beam laser.'
He adds, 'We uncovered the underlying mechanism for the simultaneous defect mitigation is the stabilisation of the keyhole (a vapour cavity caused by intense localised laser heating) by spatially manipulating the incident and reflected laser rays.'
Current methods to solve the problems in the LPBF process mainly focus on only one of the defects, states Chen, while their research 'provides a path for mitigating the three major defects simultaneously'.
The researchers also use the ring-shaped beam to drill deeper into the material, without causing instabilities, which they say enables them to print thicker layers increasing manufacturing productivity.
The team has used an alpha-beta titanium alloy Ti-6Al-4V in testing. It is one of the most widely used materials in aerospace and medical applications because of its high-specific strength and excellent corrosion resistance.
They also integrated the ring-shaped laser with switchable beam profiles into the synchrotron X-ray beamline at Argonne National Laboratory, USA, to run in situ high-speed X-ray imaging experiments that capture the dynamics of defect formation and mitigation.
'Because we understood the underlying mechanisms, we could more quickly identify the right processing conditions to produce high-quality parts using the ring-shaped beam,' explains Chen.
By increasing part quality and manufacturing productivity in the same process, the team hopes their work could enable widespread industry adoption of LPBF.
Chen believes the approach is scalable. The next step is 'to explore more complex beam shapes and gain deeper understanding of the fundamental physics for achieving defect-free and high-productivity additive manufacturing'.