Tailored polymer strengthens 3D-printed sand structures
Researchers are using a specially designed polymer to bind 3D-printed sand structures using the additive manufacturing technique of binder jetting.
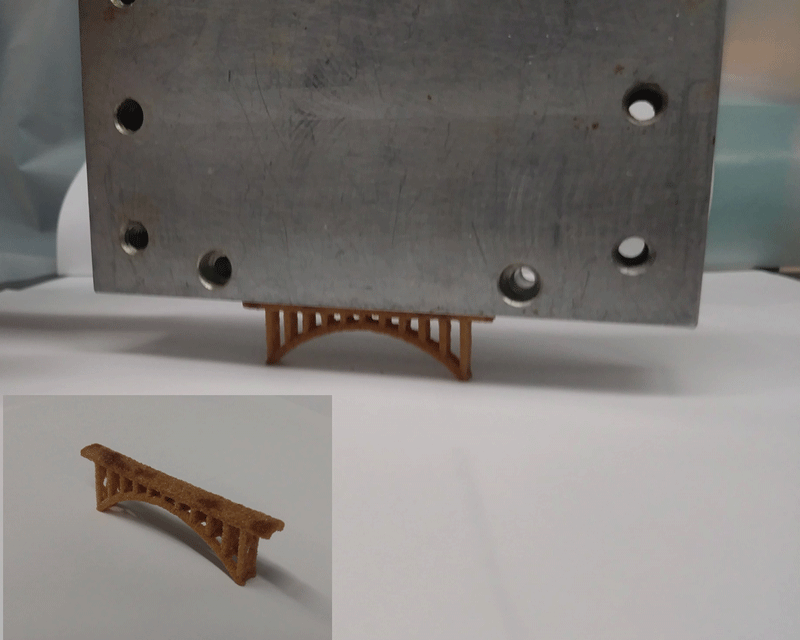
Scientists from the Oak Ridge National Laboratory (ORNL), USA, have tailored polyethylenimine (PEI) to enable sand structures with intricate geometries and enhanced strength. It is said to double the strength of sand parts compared with conventional binders. The printable polymer is also water soluble.
The team explains how silica sand is an attractive material for binder jet printing because it is cheap and abundant, holds its shape when heated, and is washable with plain water. As an example, industries want to use it for composite tooling because sand shapes can be printed, wrapped in carbon fibre and cured, and then the sand is washed away with water. However, applications have been limited because current sand parts are not strong enough to support industrial needs at a large scale.
The binder jet printing, they add, is cheaper and faster than other 3D printing methods used by industry. The concept stems from inkjet printing, but instead of using ink, the printer head jets out a liquid polymer to bind a powdered material, such as sand, building up a 3D design layer-by-layer.
‘The [new] binder works so well because of a unique chemistry that supports strong bonds with sand and reactivity with cyanoacrylate, a material commonly used in post-processing to make printed parts denser,’ says Tomonori Saito, Lead Researcher of the study.
The atomic interface between the binder and sand is critical. Silicate sand has a Si-O structure and PEI has -NH- in its structure. Upon curing, the structure rearranges to maximise the number of H-bonds between PEI and silicate, which forces the CH2 groups in the PEI to contort into a corrugated-like structure to accommodate the H-bonding anchors. This corrugated interfacial structure facilitates densely packed and tightly bound H-bonding interactions of >N-H···O-Si between the cured PEI and silicate that lead to the enhanced mechanical strength.
‘The binder acts like a glue, holding the sand together, as layers are built up to form 3D shapes. We discovered the optimal amount of PEI binder in the sand structure was 5.5wt.%,’ explains Tomonori.
Post-processing, cyanoacrylate is commonly used to strengthen printed parts, which are initially porous.
‘One of our key findings was that, unlike conventional binders, the PEI binder reacts with cyanoacrylate to create very strong chemical bonds. Our untreated part was already stronger than unreinforced concrete, and on top of that, we saw an eight-fold strength increase with the cyanoacrylate step,’ Tomonori continues.
‘The flexural strength was determined by three-point bend test. First, we showed the PEI binder for silica sand doubled the flexural strength of parts to 6.28MPa compared with that of the conventional binder (~3.6MPa), making it stronger than unreinforced concrete (~4.5MPa) in flexural loading. Next, we demonstrated that PEI in the printed parts reacts with cyanoacrylate in a post-processing step, resulting in an increase in flexural strength to 52.7MPa.’
The team has demonstrated a 3D-printed sand bridge that at 6.5cm can hold 300 times its own weight.
The researchers say that this technology could be easily scalable to current manufacturing processes. Tomonori says, ‘It is really only limited by the size of your printer. For an example, in automotive and aerospace industries, the technology could accelerate parts production, meaning you could print an engine block or manifold for vehicles.’
The team is now looking to further demonstrate the potential of this binder and expand the research to other powdered materials beyond sand that could be useful for a range of tooling and construction applications.