Steel committed to fuel switching
Steel manufacturer Ovako is installing hydrogen electrolysers at its site in Hofors, Sweden. Alex Brinded visited the facility to find out more.
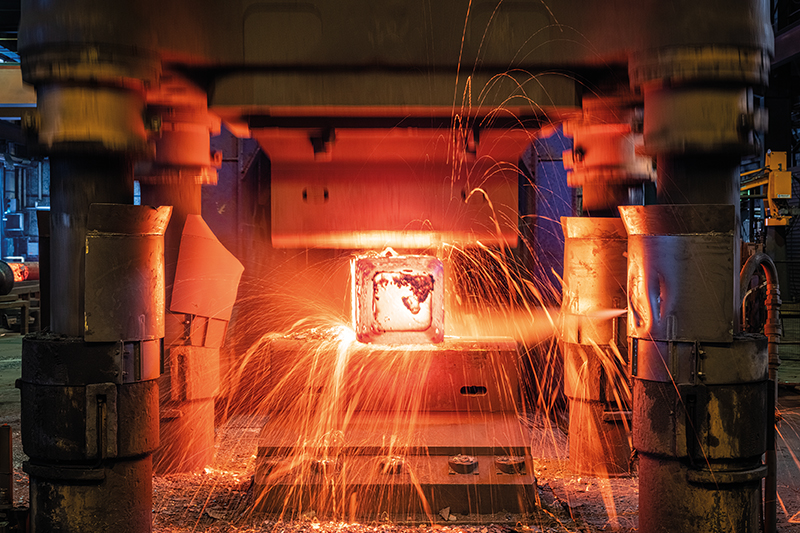
In a small town, two hours north of Stockholm, Sweden, a train winds its way down a railway track. At 4am, it returns trundling back the way it came, but lighter. If you were to stay in the outbuilding it passes metres away, you would hear the distant sounds of steel scrap being unloaded.
This is Ovako’s production facility in Hofors, where they have recently installed eight hydrogen electrolysers. The town of Hofors started producing iron in 1549, due to the coal and water that was abundant in the area. There are now 73 furnaces at Hofors, which use ingot casts while Ovako’s other sites use continuous casting.
Indeed, the Swedish steel producer hopes to install eight more hydrogen electrolyser furnaces. They have already conducted an initial trial but want to see the electrolysers in action before going full-throttle.
Steely plan
Ovako’s hydrogen project brings together Sweden’s Energy Agency, Volvo Group, Hitachi Energy, H2 Green Steel, Nel Hydrogen and their customers.
As well as providing energy for steel production, Ovako plans to supply hydrogen for fuelling stations close to their factories, while selling the energy to stabilise the power grid and use the cooling water for district heating.
They are using Phase 1 of the project to monitor hydrogen consumption and whether they will need to switch to liquefied petroleum gas (LPG) at any point. New pipework and valves have been installed to switch fuels as required, or when the cost of electricity is too great, such as at peak hours or during a power outage – as there was for a short period last winter.
Start-up and testing of the 20MW alkaline water electrolysers began in June, with production targeted for September. They have also recently secured funding for hydrogen at their site in Smedjebacken from the Swedish Energy Agency.
Heading for hydrogen
With 2,800 employees, Ovako has nine production sites in 30 countries, while its owners – Nippon Steel and Sanyo Special Steel – have more than 100,000 employees globally. Together, they make bar steel, special profiles, wire rod and wire, mechanical tubes and rings.
The recent hydrogen trial follows earlier transitions in its fuel usage. Electric arc furnace (EAF) usage at the company dates back to 1930, when the first one was installed, before the company became 100% EAF in 1977 when the last blast furnace was closed.
In 1995, the heating furnaces changed to oxyfuel, and by 2015, fossil-fuel-free electricity was supplied to all Ovako’s Swedish production sites – the other two being in Smedjebacken and Hällefors – with the site at Imatra, Finland, following suit in 2018.
In March 2020, the Hofors site reported to have produced the world’s first fossil-fuel-free heated steel for hot-forming. The control system was reprogrammed with hydrogen parameters to allow for a simple and fast switch to LPG or natural gas if required. Project Manager Mikael Persson says because the two systems are completely independent, it allows for true electric flexibility.
Japanese global financial services firm, Nomura, released an analysis in 2021 of major global steelmakers by Scope 1 and 2 emissions per tonne of crude steel. The report, Nomura ESG research: steel, nonferrous, wire and cable, found Ovako produced the least emissions. Ovako’s aim is to have reduced their CO₂e emissions by 80% against their 2015 baseline by 2030 and their carbon footprint by 60%.
They currently claim to have reduced their CO₂e emissions by 57% from 485,000t in 2015 to 210,000t in 2021, and are committed to the Science Based Targets initiative. This was mainly from use of non-fossil-fuel electricity, conversion of their furnaces, energy efficiency improvements and district heating. Carbon offsets are used to counterbalance any remaining emissions.
To deliver the 80% reduction by 2030, the company plans to change its internal transport provision, convert its rolling mill furnaces to hydrogen, switch heat treatment furnaces to electric and improve yield. It is estimated that this integrated approach would bring emissions down to 97,000t.
The melting of steel at over 1,400°C and the heat treatment process at less than 1,000°C are both electrified, while the heating of steel for hot forming at about 1,200°C could be electrified too, says the company.
Certainly, there is a wall of intense heat that can be felt standing on a viewing platform above giant automated hoists that lift the ingots in and out of reheating pits. A giant robot then manipulates and bashes the ingots before they are rolled out into bars.
In the new hydrogen electrolysers, common drinking water will be used with an electric current separating it into oxygen and hydrogen. The system comprises a transformer, rectifier, electrolysers, scrubber, gas holder, compressors and dryers.
It is anticipated the hydrogen plant will produce a maximum of 3,880Nm³ of hydrogen per hour and 1,940m³ of oxygen. It will consume 17MW every 60 minutes to begin with and ramp up to 20MW at the end of life. The auxiliary equipment will use 2.5MW/h and the system will need 9m³ of water per hour.
The cooling water will approximately circulate at a maximum of 255m³/h using an internal system via a cooling tower, with a secondary cooling water system for district heating.
These large metal tube-like electrolysers sit in a dark first-floor warehouse with the adjoining room being cleared for the installation of eight more. The cells sit in round discs neatly stacked like poker chips in a line.
Ovako report the use of hydro, wind and other fossil-free power sources, with the broad benefits of fossil-free hydrogen for fuel-cell powered trucks and residual heat for district heating of nearby communities.
Anders Lugnet, Group Technical Specialist (Energy & Furnace Technology), is responsible for the development of equipment. He says, 'It has been easier to achieve these targets with our process efficiency development and our automation – it was a more natural step. For example, we have a lot of oxyfuel on the site [making it] easy to go for hydrogen…And the burners work fine with the ones we have. But initially when we started with oxyfuel it was for process efficiency and product quality.'
Lugnet explains when the electrolysers are first used '[it] is a really slow start-up with a lower potassium hydroxide level and it cannot use full current. Then we run it for two weeks, and you take the potassium hydroxide to the 25% level and you ramp up again. The start-up takes three to four weeks. Once it is in a hot state, it (the electrolyser) increases to full-operating efficiency at 10% per minute. The maximum output is almost 4,000m³ per hour.'
He continues, 'I believe that the future will be…decentralised [hydrogen] producers…because you need pipelines and storage. Next step is to have storage…and then connect the producers with some kind of grid. But I think that is 20 years’ away.'
While looking at hydrogen storage, Patrik Ölund, Head of Group R&D, says there is the bigger problem of hydrogen combustion and avoiding hydrogen embrittlement. He notes, 'High-strength steel is more prone to [such] problems with atomic hydrogen getting into the steel, [causing] a recess concentration and a delayed fracture. We are designing a material [with] more passivation to avoid [this]. We can also design the material with hydrogen traps that can accommodate hydrogen in the steel so it will not be as detrimental.'
Forging ahead
As well as developments in manufacturing, the demands on the products themselves are changing in the move to emissions reduction technology, explains Ölund.
Ovako makes more than 500 steel grades of bars, tubes and rings for customers in automotive, mining, energy and other sectors, including their IQ-steel – an ultra-clean steel optimised for fatigue strength. Their biggest business is providing steel for wind turbine bearings – a growing sector for them – with the bearings up to 4m in diameter. While in automotive, Ölund notes as traditional gear boxes disappear, there are more issues with high-cycle fatigue with the drive-trains for electric cars.
Fatigue testing is carried at Hofors as well, with support from academic institutions. They are working with ultrasonic techniques for advanced testing to 'find inclusions'. He reports by using inversion testing they can examine large volumes with high accuracy, which allows them to see how changing certain parameters can change the product.
As I return home from an insightful two days at the firm’s Hofors site, it’s clear that Ovako is on a firm trajectory with its partners to transform steel production. The business and sustainability case is a no brainer for them. Lugnet concludes, 'Everyone wants to go fossil free [and] have exceptionally low CO₂ per tonne value…Our customers are asking for low-emission steel.'
Consuming scrap
Along with a new form of energy, Swedish steelmaker Ovako currently uses 97.2% of scrap metal to produce steel for a diverse number of products – from automotive parts and wind turbine bearings to railway clips, horseshoes, axe heads and weightlifting bars.The company reports that it is Sweden’s largest recycler and has the lowest carbon emissions in the entire steel industry. Ovako says it recycles around 800,000t of scrap each year, making it one of the largest recyclers in the Nordics.
Ovako believes steel is an ideal material for closed-loop recycling as it can be reused again with no detrimental effects on its performance. They remove most impurities through oxidation but iron is not easily oxidised. Also, as steel is magnetic, other metals are largely removed by magnetic separation.
Patrik Ölund, Head of Group R&D, says, 'It is a fantastic way to refine scrap into a really good product, with the exception of copper, which we cannot remove so we have to select the scrap to minimise it in the steel.' That means more work at the scrap input stage, but leads to a higher quality steel.