Spotlight: A rare approach
Materials World spoke to the team at Less Common Metals based in Chester, UK, to discuss sourcing, materials analysis and its position in the permanent magnet supply chain.
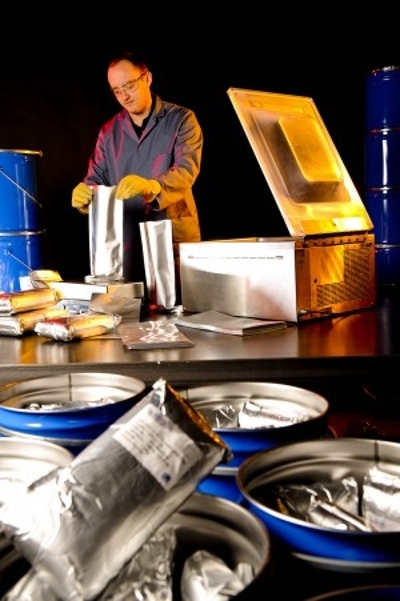
As a specialist manufacturer and supplier of rare earth elements and complex metals and alloys, Less Common Metals (LCM) has opted for a different approach to a wide range of material requirements. For a start, it makes its own neodymium metal onsite and uses this in the manufacture of specified neodymium iron boron (NdFeB) alloys for supply to magnet makers around the world.
‘There are two main advantages of making our own neodymium metal. First of all, we are one of the very few companies in the world outside of China who can make neodymium metal, so the fact we have that capability and expertise onsite is a very important addition to our skillset,’ explains Ian Higgins, LCM’s Managing Director.
‘It also gives us a lot more opportunities for sourcing non-Chinese rare earths. It’s relatively easy to obtain neodymium oxide from outside of China, whereas the metal is pretty much exclusively a Chinese material. This means we now have more options for our resourcing as a result of making our own metal. I would probably say this has been the biggest achievement in my career so far.’
Higgins adds that previous attempts to achieve this had made it clear just how big a challenge it would be to access Chinese technology and adapt it to Western-world production standards.
‘I was fortunate to enjoy the support of an excellent team, both in the UK and China, and this resulted in a project that exceeded all expectations in terms of smoothness of operation and achieving all the objectives. For me, the project was an excellent illustration of what can be achieved with correct planning and execution,’ he says.
Accuracy matters
LCM also specialises in samarium cobalt (SmCo) based powders and has had to develop precise melting profiles over the years, to ensure repeatability and accuracy for melting this large family of alloys with minimal deviation. These SmCo alloy powders are produced by induction melting followed by crushing and milling.
Vacuum induction furnaces are commonly used which means melting is performed in a furnace chamber under a partial pressure of inert gas. The melt cycles determine what power is added for how long and these differ depending on product types, based on incremental increases to give a molten solution.
Temperature readings are taken during the melt cycle to determine if enough heat is present to ensure full dissolution of raw materials. Again, different alloys require specific targets.Soak times allow the alloy to sit at a set temperature for a predetermined period of time to ensure that full melt homogeneity is obtained. The temperature is adjusted for optimum pouring and stabilised for casting. The cast alloy is then cooled until safe to handle.
LCM Process Support Technician, Jonathan Price, explains a typical workflow. ‘We never know what we might be dealing with next. You may see a breakdown of elements required to create a specific chemical composition and prepare for that series of melts, to find it is eventually to be used in F1 car components, scientific equipment in Europe or jet fighter engine parts. There are many new projects and alloy developments at LCM that constantly require us to move and develop with the times. Improving our knowledge and lending that to new products in development has been essential.’
Testing and inspecting alloys
Having an analytical laboratory onsite has been crucial to maintaining the standard of their bespoke alloys, notes Higgins. The laboratory has been operational since 2001 and its primary functions are to test finished products against customer specifications and to provide analytical support to the production department. It is also open to those requiring analysis of alloys, metals, oxides and inorganic salts.
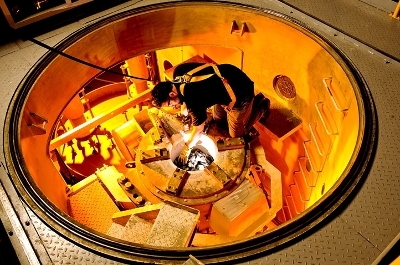
Characterisation of alloys is done by inductive coupled plasma optical emission spectroscopy (ICP-OES), an analytical technique used to detect chemical elements. This is used for major component quantification as well as trace element analysis, while gas analysers are used to measure carbon, sulphur, oxygen and nitrogen. Several tests are carried out including particle size measurement, microstructure analysis, pH testing, flake thickness measurement for strip cast alloys, chemical oxygen demand (COD), and loss on ignition (LOI).
‘The lab team currently consists of three analytical chemists who have a combined 50 years of experience in a variety of backgrounds,’ adds Higgins.
In 2018, the LCM laboratory acquired an ICP optical emission spectrograph to sit alongside the existing ICP-OES. ‘The instrument underwent extensive validation to show that major constituent methods were consistent with the original appliance. In terms of trace analysis, the instrument has been useful in overcoming some of the unique analytical challenges we come across with rare earth elements,’ says George Thomas, LCM Senior Analytical Chemist.
‘In recent months, the production staff have successfully melted new custom alloys based on combinations of various transition metals, with or without rare earth additions. For all the challenges these alloys present the production staff, the laboratory faces the fresh challenge of being able to analyse such materials. In these situations, we have to develop testing methods rapidly and to demonstrate that these methods are valid and repeatable, so that we can provide reliable quality control throughout the trials and the subsequent manufacture of finished products. We also have to consider sample preparation and health and safety, as many of the materials used in trials have not been handled in the laboratory before,’ adds Thomas. Quality assurance is another priority, says Thomas. Particularly when dealing with its samarium cobalt alloys, which need to be produced to a high degree of precision.
Establishing an EU supply chain
‘Another factor has been the importance of an environmental management system,’ according to Higgins. ‘Our approach has been to embed core ethical and environmental standards into the heart of the business. The rare earth industry is dominated by cheap supply and production from China, which often operates far lower ethical and environmental standards that can lead to significant dangerous environmental impacts. We are actively working to establish non-Chinese alternatives for critical raw materials with focus on ensuring they are produced to the highest environmental, quality, health and safety standards. Raw material sources are also audited to ensure they are not supplied from conflict areas, or companies that have unacceptable health, safety and environmental standards. This aligns with manufacturer’s requirements for responsible sourcing.’
Ruth Miller, Environmental Co-ordinator for LCM, described some current projects the company is working on to secure materials.
‘We are now involved with several European Union funded research projects, such as SecREEts and DEMETER, all pioneering new technologies to provide ethically-sourced raw materials and establish an integrated European supply chain. From supporting projects that aim to establish a stable and secure supply of rare earth elements from non-Chinese sources, to a project for a closed-loop permanent magnet recycling process.
The importance of being involved in these collaborative projects is colossal,’ says Miller. This includes the recovery and recycling of rare earth permanent magnet motors and generators from electric vehicles. ‘We are also now working on using technologies developed in China, but operating them to EU standards, such as the production of rare earth metals from oxides by electrolysis.’