Sea change for zinc oxide production
Chemical engineers claim to have developed a method of manufacturing zinc oxide (ZnO) for health and beauty products, such as sunscreen, that requires 95% less energy and is more cost effective.
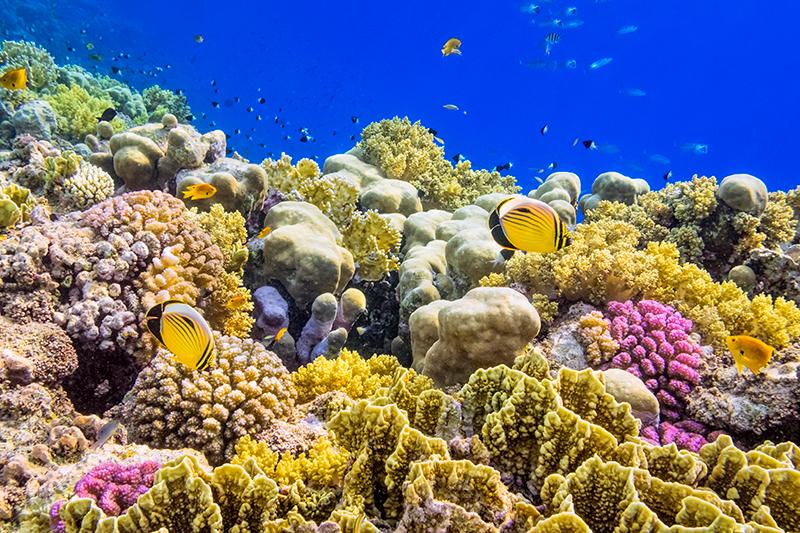
The scientists, from the University of Sheffield and Imperial College London, UK, note this could eliminate the ‘devastating impact’ of chemical-based sunscreens on marine life.
The technique is called Oxidative Ionothermal Synthesis (OIS). Dr Kyra Sedransk Campbell, a Research Fellow at the University of Sheffield, explains, ‘There are currently two categories of ZnO available on the market – mass (bulk) produced and advanced. The former is offered in limited grades and is produced without a view towards specificity. These products are low in price, but also low in quality and performance…using extremely energy intensive processes.
‘The end-users using this product either cannot afford a higher priced and better performing material, or are satisfied as they may not be aware that a better alternative is available.
‘In the latter category, the specification for advanced zinc oxide requires complex techniques which often cannot be scaled, and therefore a high price is commanded.’
Campbell describes, ‘This new technique is…a one-pot method that uses water blended with ionic liquids to create a specific environment for the nucleation and growth of zinc oxide. This careful control allows us to achieve specificity in the products made…[It is a] flexible manufacturing method that can enable production of a wide range of particle types – very unusual for a wet-chemistry method in which analysing is done in the liquid phase.
‘And we start with a solid precursor (rather than a salt). This is an important removal of a step (solid precursor to salt) that requires energy and therefore has an environmental footprint itself.’
The OIS method dramatically reduces energy needs by operating at relatively low pressures, Campbell adds.
The researchers convey the importance of energy and cost efficient manufacture of ZnO by explaining how alternative low-cost sunscreens contain chemicals that impact on marine life, such as the bleaching of coral reefs. Meanwhile, high-end sunscreens that contain zinc oxide avoid such effects on the environment. ‘The market is predominantly made up of the chemical sunscreens because the price point is significantly lower than that of mineral-based sunscreens,’ asserts Campbell.
She says that, although their products cross into the advanced materials category, ‘because it is a one-pot method, we have confidence that the translation [in the market] should be relatively straightforward’.
Zinc oxide is used across a wide range of applications including tyres, paints, personal care products, sensors, etc. There is also a growing interest in zinc oxide for battery applications.
‘The new technique…offers a sustainable method for manufacturing zinc oxide. Moreover, it has an inherent flexibility to make a wide range of structures with limited tuning required. The latter point is essential as it makes the technology scalable whilst also simultaneously offering flexibility towards different end products,’ Campbell adds.
The team has now launched a start-up company to commercialise the technique, called Nanomox. ‘The company’s first target is to demonstrate the scalability of producing zinc oxide using this OIS method. This will then provide them with additional material in a sufficient quantity so that they can do more testing to work with partner companies towards delivering both more sustainable and higher specification products.
‘We have [also] demonstrated in some preliminary tests that we are able to use recycled products as our starting material and, potentially, use waste streams containing zinc. With the expansion of this work it suggests that we could, effectively, upcycle recycled/waste zinc into a high value commodity.’