Recycling the ‘unrecyclable’ complex mixed plastic waste
Complex mixed plastic waste gets a new lease of life in construction infrastructure and interiors.
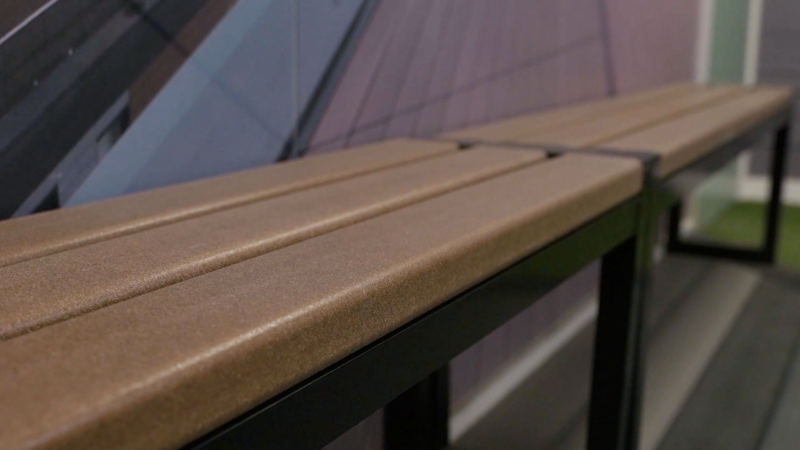
Professor Edward Kosior FIMMM, Managing Director at Nextek Ltd, and Projects Manager Dr Jonathan Mitchell break down the project journey.
Turning the most complex mixed waste streams back into high-value, high-performance building materials is poised to shift the building sector’s entire ecosystem over the next few years. While this does require diving deep into the waste stream to extract what was previously deemed ‘unrecyclable’, we now have the technology to create high-value building applications from low-value resources.
As organisations focus on incorporating end-of-life strategies into everything destined to be placed on the market, we will be able to more rapidly adopt and expand on these emerging technologies to efficiently turn difficult-to-recycle packaging into high-value applications. This will of course require a concerted effort to design for circular economy recycling and continually develop new destinations for every waste fraction.
We have no choice but to do this as the direct impact of waste management sits at the very heart of climate change.
Redefining ‘waste’
From the building sector’s perspective, this is a major opportunity to simultaneously reduce its carbon footprint and offer innovative destinations for low-value waste. Certainly, the construction industry has a significant role to play in our race to reduce our carbon footprint.
According to the UK's Construction Industry Council (CIC) report on Climate Change, the built environment and construction sector accounts for 38% of global carbon emissions, and it has been estimated that globally we build the equivalent of a city the size of Paris every week.
Funded by the Welsh Government, climate action organisation WRAP commissioned a series of supply chain projects designed to drive market confidence in using post-consumer recycled materials in products already on the market. The projects aim to demonstrate how technical challenges can be overcome, and consider the economic and environmental benefits of doing so.
This led to Nextek’s involvement to showcase how low-value materials with no existing end market can be turned into valuable composites destined for a number of building applications.
Urban versus traditional
Timber may be a staple building material but unfortunately it comes at a CO₂ cost, namely its carbon stock – the amount of carbon that has been sequestered from the atmosphere and is stored within the forest ecosystem. It plays a vital role in our efforts to manage our precarious Carbon Budget. According to a report by the Forestry Commission, it has been estimated that the total carbon stock in UK forests is set to fall from around 18Mt of CO₂ in 2020 to around 10Mt by 2040.
While the building sector does have an active re-planting scheme, these figures are concerning as they reflect a number of factors such as ageing forestry, and damage due to mis-managed deforestation and fires.
Taking a range of hard-to-recycle materials, such as crisp packets, plastic food pouches and single-use coffee cups, Nextek sets out to demonstrate how tapping into the recycling stream could cost-effectively and sustainably reduce our reliance on virgin timber, and offer a new destination for previously unrecyclable post-consumer packaging and materials.
Nextek has turned this complex range of polymers, composed of multilayer polypropylene (PP) and low-density polyethylene (LDPE) film, into a unique composite by adding cellulosic fibres and interfacial surface tension modifiers to promote interphase adhesion. This makes the composite suitable for multiple applications, including waterproof decking and furniture that could have the potential to scale to structurally strong materials.
The composite is made by pre-sorting the collected film materials into discreet fractions based on polymer type using their near-infrared polymer signatures, and then blending the formulation components into a uniform mixture prior to a melt compounding step that assures all components are well dispersed. The compounded composite is then processed directly or as a blend by extrusion or injection moulding into new products.
In this project, the team has used up to 30% of this plastic/paper composite material, and its durability, strength and versatility easily matches wood as a building material, in fact in many instances it surpasses it.
In the case of decking products, a range of addition rates of this composite material were evaluated. The key performance parameters that were investigated were the stiffness (modulus), moisture uptake and its flexural strength. This easily matched and exceeded the specifications of the standard formulation, and natural wood as a building material.
The resins used are derived from the collected films and are predominantly polyolefins – i.e. polyethylene (LDPE, LLDPE, HDPE) – and PP in mono-layer formats and a proportion of multilayer formats. These materials have a degree of miscibility due to their similar non-polar nature, allowing formulated blends to be structurally strong and moisture and fungi insensitive, providing dimensional stability and freedom from decay. Balancing the formulation of the composites between polymer and cellulosic fibre phases allows the properties of stiffness, toughness, hardness and dimensional stability to be adjusted.
The materials are also not prone to buckling and can be easily fastened for increased strength, making them more versatile, durable, totally recyclable and easily shaped with low maintenance costs. Since the composites are blends of thermoplastic resins and cellulosic fibre, they can be regranulated at the end of life and put back at controlled ratios during the manufacturing of new products.
A lifecycle assessment, conducted by Greenwich University, UK, comparing the reference composite resin with waste polymers and coffee cups demonstrates lower environmental impact performance across most of the environmental categories than current timber-based composite building materials. This is due to local sourcing of existing materials as opposed to using imported timber fibres for the standard composites. Specific differences were lower global warming potential, land use, water consumption, human toxicity, aquatic toxicity and aquatic eutrophication.
The project is currently scaling up to explore new applications and tapping into a wider range of complex polymeric materials, such as end-of-life durable goods, unrecyclable automotive shredder residue, and laminated plastic-coated paper board.
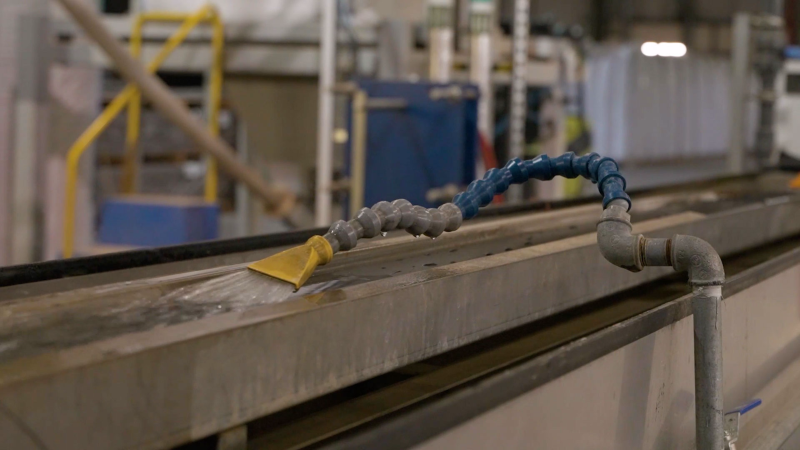
Lightening concrete’s load
Expanding on timber replacement, Nextek applied similar scientific principles to displacing cement with aggregates made from recycled materials, to lower cement’s carbon footprint and find yet another destination for complex waste plastics.
In this scenario, the waste plastics did not require any additional processing steps other than size reduction by granulation to particles approximately 3-10mm in the major dimensions.
This allows the plastic to act as a low-density aggregate and be easily integrated with the mixing stages of cement-based products at volume ratios of 25% and higher, depending on the weight reduction required. There is a reduction in the volume fraction of plastic used, but the properties were found to be adequate for non-structural applications where surface stone appearance was the target.
The polymer/cement composites were designed for low-strength and non-structural applications such as blinding concrete, concrete building blocks, lightweight concrete, pipe laying, road culvert surround concrete and permeable medium, as well as for low-to-medium traffic road pavements, among other uses.
One particular trial that is currently underway, with support from WRAP, focuses on aesthetics and lightweighting of a construction product used on external walls. The top appearance replicates real stone by formulating the top layer with crushed stone and using a mould that has a typical stone surface profile. The back of the stone was filled with a mix of polymer and cement to achieve the desired properties.
This composite structure reduces thermal conductivity, hence boosting the insulation performance of the materials, as well as reducing the density and the product weight making it lighter to install and lessening the load on the buildings.
This lightweight concrete is reportedly 13% lower in CO₂e due to its displacement of the cement from the concrete.
Given that the proportion of polymer could be in the order of 25% of the volume and approximately 10% of the weight, the reduction in cost would be close to 10%. Combined with the CO₂e reductions, this is a compelling incentive for manufacturers to explore these options further.
Building a sustainable future
As we simultaneously strive to improve recycling practices, expand waste collection and enhance the disposal processes to prevent plastic leakage, we must also ensure that the chosen solutions do not have unintended consequences such as raising emissions.
The lightweighting of concrete and the timber replacement projects go a long way to demonstrate the significant value in overcoming the commercial and technical challenges to tapping into alternative waste streams. The resulting reduction of landfilling and the boosting of strong, durable and low-carbon building materials is key to addressing climate change.
By applying novel technology to address issues and opportunities in the multiple lifecycles of polymers, we are entering a new era in sustainable construction that will help make net-zero a viable future for the built environment.