Closed-loop recycling of plastics from vehicle interiors
A solvent-based plastics recycling technique designed to meet the requirements of the European Vehicle Directive.
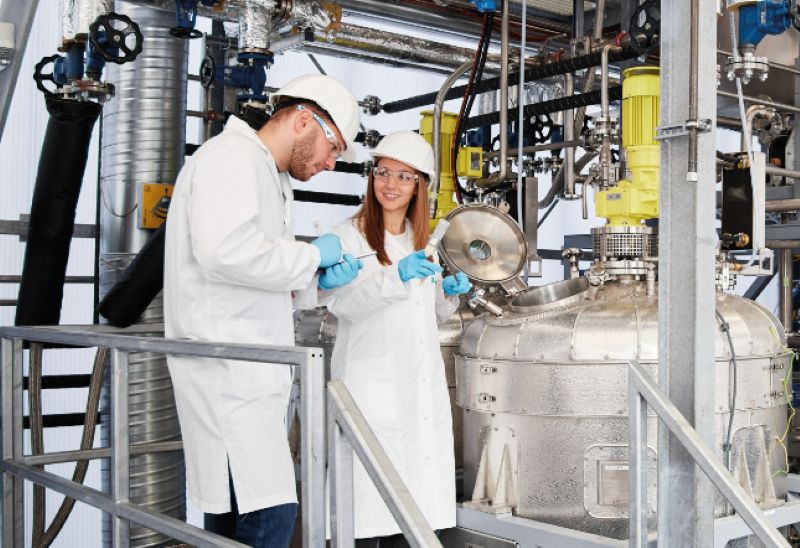
According to EU regulations, plastic components in new vehicles must contain 25% recycled materials by 2030.
The Fraunhofer Institute for Process Engineering and Packaging IVV in Germany is further developing its technique to selectively dissolve target polymers from waste streams and potentially remove critical legacy additives.
The aim is to meet the high requirements for processability and odour emissions for reuse in vehicle interiors.
The approach allows engineering plastics to be separated, purified and recovered from the materials mixture in end-of-life vehicles.
Once the target polymer is sorted from the shredder residue, it is selectively dissolved in a special, non-hazardous, solvent formulation. The undissolved components are then mechanically removed, and contaminants are separated at the molecular level using special purification steps.
After purification, the size and molecular weight distribution of the target polymer’s macromolecules are claimed to be the same as virgin materials. The target material is recovered from the solvent by precipitation and dried.
The recovered plastics reportedly reach purity levels of up to 99%, and legacy additives can be reduced to those below the legal threshold, e.g. 100, 500 or 1,000ppm.
A pilot test has been completed with an original equipment manufacturer.
Dr Martin Schlummer at the Fraunhofer Institute IVV says, 'Dissolution recycling selectively dissolves target polymers from mechanically enriched 80-90% feedstock and separates non-target materials and polymers as well as contaminants.
'Even fibres, fillers and legacy additives like flame-retardants and plasticisers can be removed to receive a purified, recycled polymer for new automotive compounds.'
The method is advantageous Schlummer claims, because 'it is a physical dissolution process as the polymers are not degraded and thus an effective alternative to chemical recycling, as it does not require polymerisation from chemically recycled feedstocks (pyrolysis oil, monomers).
'It produces purified polymers from mixed and contaminated waste plastics, not applicable to mechanical and often not to chemical recycling.'
He continues, 'Shredder residues with high shares of rigid plastics are separated by a combination of common sorting technologies, including metal separation, density separation, tribo-electrostatic sorting and spectroscopic sorting to enrich target polymers of higher densities.
'Different combinations of these technologies can enrich the target polymers PP, PC+ABS and PAs with high purities, [with] all sorting technologies allowing high throughputs and being available at industrial scale.
'In best case, the plastic recycling strategy goes hand-in-hand with current metal recovery and uses synergies.'
The recycled materials are then optimised for their mechanical properties, which are demanding for the automotive market.
He adds, 'Stabilisers are used to enhance thermal stability and prevent degradation during processing.
'Depending on the use of the recyclates, impact modifiers or fillers can be added to adjust the mechanical properties of the compound formulation according to the intended application. Quantities depend on the application.'
The recyclate obtained is compounded with virgin material and additives to produce a product with a high polymerase chain reaction content.
Schlummer says, 'Depending on the application and the specific formulation, recycled plastics can contain up to 100% recycled content. This means that, ideally, no virgin materials are needed in the final product if sufficient high-quality recyclates are available. Industry, however, mostly requests recyclates containing 30-70% recycled content.'
A project funded by the Volkswagen Foundation will develop the process to close the loop on complex post-consumer waste from end-of-life vehicles for high-quality automotive interior applications.