Reclaiming magnets from loudspeakers
A patented recycling technology that extracts rare earth magnets from loudspeakers in end-of-life cars and flat screen TVs could deliver an important recycling stream for the UK and a domestic source of these metals.
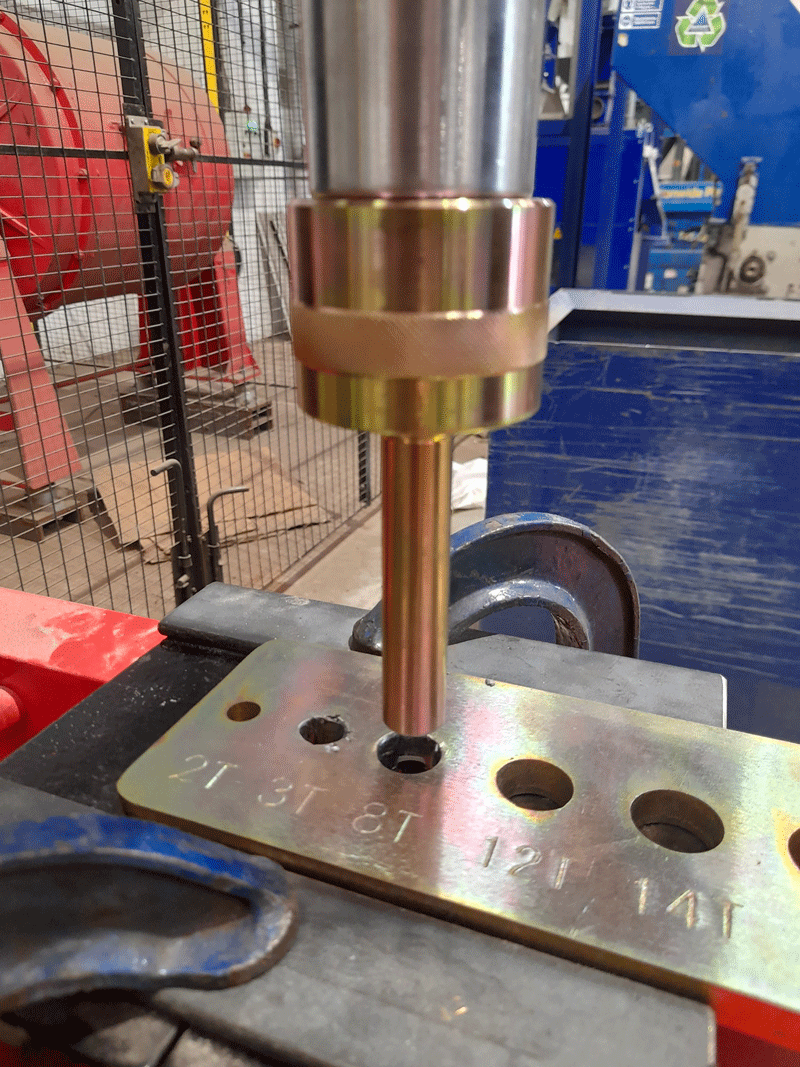
Loudspeakers account for around 20% of rare earth magnet use. The team behind the Rare-Earth Extraction from Audio Products (REAP) project, based at the University of Birmingham, UK, have developed the technology known as Hydrogen Recycling of Magnet Scrap (HPMS). It extracts and demagnetises the neodymium iron boron (NdFeB) alloy powders embedded in loudspeakers.
A number of competing technologies currently remove magnets from end-of-life products, relying on thermal demagnetisation and grinding off the surface coatings, explain the researchers,
but they believe the HPMS process is more cost-effective with fewer energy-intensive steps to remove the material.
'The HPMS process works by introducing hydrogen to the magnet at room temperature and near atmospheric pressure,' explains Professor Allan Walton from the University’s School of Metallurgy and Materials. 'The hydrogen reacts with the material, working its way through the grain boundaries and then into the grains themselves. The reaction generates heat and a volume expansion, which causes the material to break apart into an alloy powder. The coatings peel from the surface and, at this point, the material also demagnetises.'
Walton adds that the alloy powder is then separated from the remaining scrap and a purification process is performed to remove undesirable trace elements and coating materials. Once this is completed, the purified powder can be directly processed back into a new magnet, 'completing the short-loop circle'.
According to the project collaborators, the recompacted magnets have a comparable magnetic property to the originals.
European Metal Recycling (EMR) identifies suitable target products from appropriate waste streams for the project and uses a novel punching process to remove the magnets so they are ‘reactor ready’ for the downstream HPMS process.
Walton shares, 'This means that there is access for hydrogen to get to the magnet and a route out for the demagnetised powder to leave the product. Ultimately, the higher the magnet-to-product ratio, the higher the yield from the HPMS process. The novel punching process developed by EMR produces a feedstock with a very high yield for the downstream HPMS process.'
Walton is one of four directors at HyProMag, the spin-out company leading on the project. He explains that the REAP initiative aims to develop a domestic supply of recycled rare earth magnets from multiple scrap sources.
Although current end-of-life vehicles are not large users of rare earth magnets, he notes that future models, especially electric and hybrid vehicles, will contain significantly more material, providing an important feedstock in the long-term.
The University of Birmingham and HyProMag’s analysis also shows that 85% of flat screen TVs in the UK contain NdFeB. 'Within flat screen TVs, we have estimated there could be around 34,000kg in the waste stream each year,' he says.
Quantifying the recycling potential is problematic, however, because collection systems are non-existent. The University has been awarded funding to develop an automated pilot line at Tyseley Energy Park to extract NdFeB alloy powder and for downstream magnet production, although it will be another year before it is fully operational.
Walton says the facility will enable HyProMag to process up to 400kg of NdFeb alloy powder per HPMS batch. 'The extracted material can be put back into the UK supply chain at multiple points, including direct remanufacture into sintered magnets.
'The pre-processing techniques developed by EMR will be automated and used as one of multiple feedstocks to the large pilot line. This will build upon previous projects where, for example, hard drive scrap was developed. Longer term, we are investigating a much broader range of end-of-life scrap.'
The collaborators are evaluating several product options, including hydrogen decrepitated (HD) demagnetised powders suitable for magnet producers, alloy ingot remelted from HD powders suitable for alloy feed or magnet production, anisotropic alloy powders (HDDR) for bonded magnets, and sintered NdFeB magnets for automotive applications.