Precision within arm’s reach for industrial robotics
The safety and precision of industrial robotics may be improved with a new range of nanomaterial, wireless, strain sensors integrated into the robots’ arms.
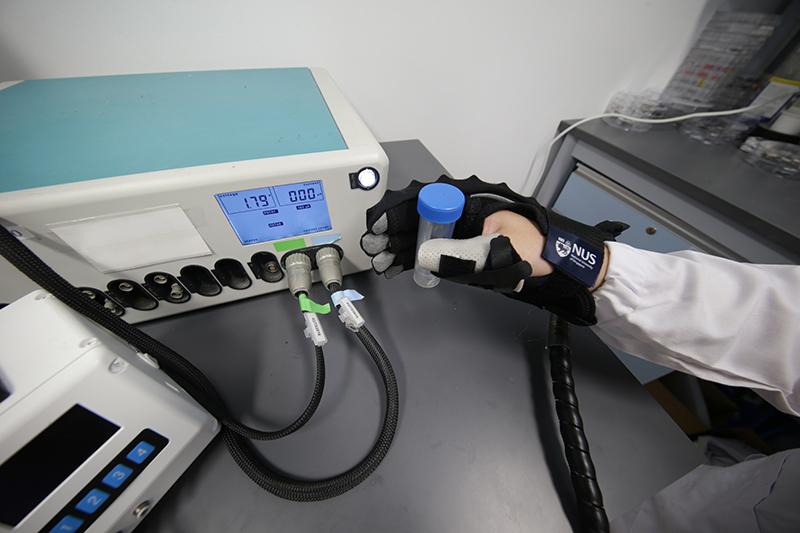
Researchers at the National University of Singapore claim they are 10 times more sensitive than existing technology when measuring minute movements.
The production process is said to enable the sensors to be customised to any working window between 0–900%, while maintaining high sensitivity and signal-to-noise ratio – standard sensors typically vary up to 100%.
‘[We] proposed a promising approach by leveraging wireless technology (for example, near-field communication (NFC)) to develop a wireless, battery-free, strain sensing system that is capable of providing a remote power supply and maintaining facile data connectivity,’ says Yang Haitao, Doctoral Student at the National University of Singapore.
‘Such integration of a wireless transmission node with a high-performance strain sensing system is demonstrated, for the first time, for real-time monitoring of the actuation strains of soft exoskeletons.’
The team fabricated the strain sensors using MXenes – flexible, stretchable and electrically conductive nanomaterials. This was achieved by ‘heating a MXenes-coated responsive substrate above the glass transition temperature of polystyrene (PS), at which the PS substrate was shrunk to 25% of its original area (50% of its original length),’ Haitao notes.
‘By harnessing the surface instability, the upper-layer graphene oxide PS-MXene nanocoating was biaxially compressed into isotropic crumples with the depth of ca. 4µm, and the G1-2D PS-MXene nanocoating was next transferred onto a very high bond (VHB) elastic substrate for the assembly of the strain sensors.’
These can then be coated onto a robotic arm to measure subtle movements as they are stretched. Once coated, the sensors can measure the extent to which the robotic arms are moving and the current position to the resting state.
The mechanism of the NFC-enabled wireless sensing system incorporates a self-designed NFC chip, which is connected to a MXenes sensing module and wirelessly coupled to an NFC reader (i.e., smartphone).
The team has compared the sensing performance – mainly sensitivity and working window – of the strain sensors with other sensors developed using different fabrication technologies, including physical blending, chemical crosslinking, vapour deposition and layer-by-layer assembly. They have also compared a breadth of nanomaterials, including metal foil, carbon nanotubes, silver nanowires, graphene, MXene and molybdenum disulfide (MoS₂).
‘We [also] compared the execution of sensing data processing (including transmission, storage, and analysis) by our system – collectively monitoring the multi-segment robotic actuations through a single database channel – and the conventional method (the integration of multiple power sources and data storage devices together),’ Haitao explains.
‘In doing so, we proved the unique advantage of the combination of the MXenes strain sensor and NFC technology against other published technologies. The wireless MXenes sensor demonstrated ultra-high strain sensitivity (~14,000) in a user-designated working window, and the resistance profiles were collected wirelessly.’
According to the team, the strain-sensing performance was interfered by the analog-to-digital converter (ADC), after the MXenes sensor/circuit was incorporated with the NFC module. ‘For other 2D material-based strain sensors (such as reduced graphene oxide and MoS₂) and commercial sensors, their initial levels of resistance were at least an order of magnitude higher, so the ADC unit would limit their strain ranges and sacrifice their sensitivity,’ Haitao adds.
By adapting NFC technology for the wireless sensing system, the user can collect and visualise data using smart devices such as a smartphone. ‘Our research is expected to support and promote the realisation of the vision of the future smart factory, where the use of mobile device will become increasingly prevalent,’ notes Haitao.
Looking ahead, Haitao explains scalability is determined by fabrication of the MXenes nanocoating with the unique microstructure. ‘One strain sensor only requires a MXenes nanocoating with an area of 2cmx1cm, so we can fabricate 120 strain sensors during the one-step fabrication.’