Milking it – plastic-like foam gets tough with proteins
Milk protein whey – a by-product of cheese making – is being used to fabricate high-performance, plastic-like foams that show chemical resistance and mechanical strength, stiffness, and toughness in harsh environments at over 150°C.
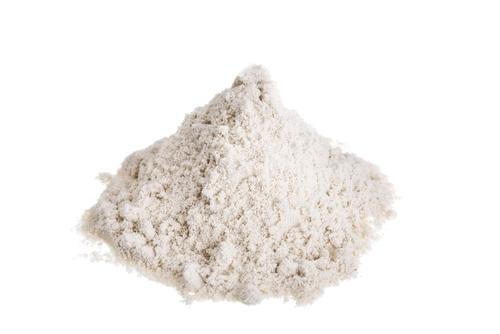
The product could be used for applications such as filtration, thermal insulation, fluid absorption, catalysts in cars, fuel filters, or packaging foam for sound or thermal insulation, improving on current plastics.
According to the study, High-temperature and chemically resistant foams from sustainable nanostructured protein published in Advanced Sustainable Systems, the foams can retain their properties at 180°C for as long as 24 hours, exceeding the properties of most ‘classical petroleum-based thermoplastics’.
‘With the harsh environment we exposed the foam to, the…mechanical properties, [in fact], improved relative to the unexposed material,’ says Mikael Hedenqvist, Professor in the Division of Polymeric Materials at KTH Royal Institute of Technology, Sweden. ‘We explain that being an effect of chemical crosslinking of the protein during the harsh conditions.’
The foam is made from protein nanofibrils (PNFs) which are self-assembled from hydrolysed whey proteins. ‘PNFs grown from 40g L-1 whey protein under acidic conditions (pH2), followed by incubation at 80°C for 24 hours, were straight with a length of up to 5µm and width of ≈4nm,’ the paper reads.
‘The lyophilised PNF foams designated PNF-40-gly-33 (with glycerol as plasticiser) and PNF-40 (without glycerol) exhibited greater temperature stability than the commercial-grade petroleum-based thermoplastic foams (here polystyrene and polyethylene), which collapsed/melted after being subjected to a temperature of 150°C and were oxidised/degraded within 24 hours.’
The paper adds that ‘the high density of hydrogen bonds formed between peptide segments arranged in the form of B-sheets provides the PNFs with a strength as high as 0.6GPa (value calculated from a single fibril), which is comparable with that of steel. The fibrils thus possess physical properties significantly stronger than the non-fibrillated proteins.’
And while the material shows a colour change, the protein foams maintain their shape. The foam’s properties are also found to improve with age. Its mechanical performance enhances after days of exposure to high temperatures – after one month of exposure to 150°C, the material become stiffer, tougher and stronger. Following the ageing process, the degradation onset temperature of the PNF-40 foam is found to increase from 260-280°C.
The char residue after pyrolysis, meanwhile, is ≈26%, which the research says is beneficial in applications where fire resistance is needed. The researchers explain that polyurethane forms a liquid during a fire, whereas the protein instead leaves a char.
The study reports that PNFs are considered good candidates for bio-based foams as they combine mechanical strength with flexibility, while also providing a material with biocompatible properties.
Finally, the material has also proved resistant to water and aggressive substances after the ageing process, which polymerises the protein, creating new covalent bonds that stabilise the foams. Surfactants and reducing agents normally decompose or dissolve proteins, but after ageing they show resistance – and the foam is also unaffected by diesel fuel or hot oil.
Hedenqvist concludes, ‘The next step is to develop further the foaming and nanofibril production processes for upscaling.’