Metal waste can make hydrogen
University of Nottingham, UK, scientists have turned metal waste into a catalyst to make hydrogen from water.
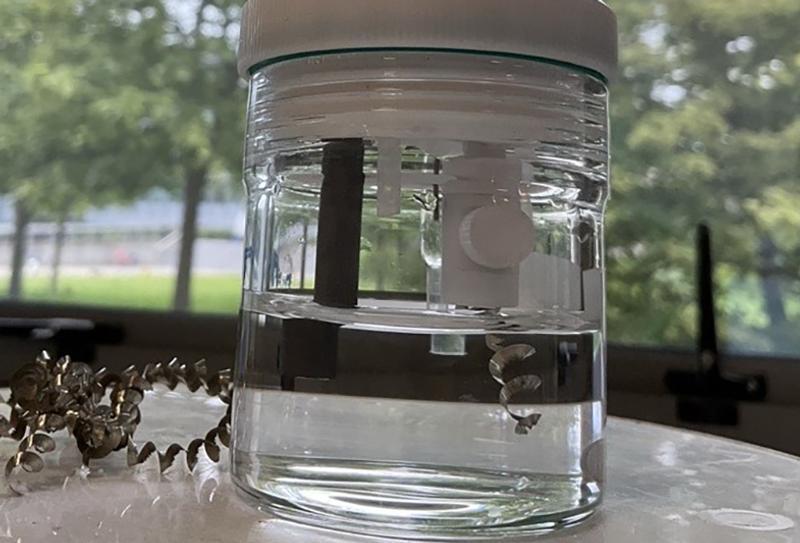
Professor Andrei Khlobystov says this technology solves two challenges. It enables the production of green hydrogen using the least amount of precious metal possible, and it upcycles metal waste from the aerospace industry, all in a single process.
The team reports being able to produce hydrogen from water using only a tenth of the amount of platinum compared to a cutting-edge commercial catalyst.
They spread only 28µg of the precious metal over 1cm2 of swarf to create the lab-scale electrolyser, which is said to operate with 100% efficiency and produces 0.5L of hydrogen gas per minute from a single piece of swarf.
By using a scanning electron microscope, the team inspected the seemingly smooth stainless steel, titanium and nickel alloy swarf by-product from the metal machining industry. They were astonished to discover grooves and ridges that were only tens of nanometres wide and realised this could be an opportunity to fabricate electrocatalysts that can split water into hydrogen and oxygen. The grooves and ridges can anchor platinum or cobalt atoms.
Khlobystov explains, 'The surface area of electrodes plays a crucial role in determining the hydrogen production rate in water-splitting electrolysers. Swarf has a larger surface area compared to flat metal due to nanotextured grooves and ridges. By decorating these features with platinum atoms, we can improve electrocatalytic performance and stabilise platinum against undesirable processes like leaching or coarsening.'
Magnetron sputtering creates a platinum atom ‘rain’ on the swarf’s surface. These atoms coalesce into nanoparticles that fit into the nanoscale grooves.
By using argon gas to generate plasma around a platinum metal disk, Khlobystov says the ions knock out single platinum atoms that fall onto a surface. 'The atoms form clusters whose size depends on the amount of metal and surface nanotexture. The entire process, including the sputtering chamber evacuation, takes 10 minutes, but the actual platinum deposition time is between 10 and 90 seconds,' he explains.
Khlobystov notes that the process for cobalt or any other metal works similar to platinum, with the only difference being that cobalt nanoclusters quickly react with oxygen upon exposure to air. As a result, clusters of cobalt transform into cobalt hydroxide, which acts as the active material for oxygen evolution on the anode side of the electrolyser.
Titanium alloy is the best support for platinum in hydrogen evolution on the cathode, he highlights, while stainless steel performs poorly. Whereas for the anode, a nickel alloy support performs best with cobalt. The researchers plan to investigate this further.
The team thinks that any metal waste source could be used theoretically, provided it has a nanotexture that can anchor platinum or cobalt atoms.
The size and shape of the grooves can vary depending on the metal waste generation method, which can affect the electrocatalyst’s efficiency.
To scale up the process, they would load more swarf into the magnetron sputtering chamber or modify it for a flow process. The team is now partnering with AqSorption, a Nottingham company specialising in electrolyser design and fabrication, to scale up the technology.