Making lower carbon cements
BRE Principal Consultant and Cementitious Materials Group member, Andrew Dunster FIMMM, discusses some of the alternatives to pure Portland cements as well as research, development and testing of low-carbon cements and concretes.

Cementitious materials make up more than half of the materials we use worldwide. While the category has low embodied energy compared with many other materials, these large volumes mean they account for approximately 8% of global CO2 emissions. Looking ahead, the demand for cementitious materials is likely to remain relatively static in Europe, while in emerging and developing countries consumption of cement will continue to rise to meet the needs of growing populations and urbanisation.
However, according to the interactive world cement industry map on the Industry About website, most of the major cement producers are global businesses and it is likely that cementitious innovations adopted in Europe and the USA would spill over into new global markets. Although there are other applications, the primary use for cement is in concrete, which comprises predominantly cementitious materials, water, coarse aggregates and sand.
In the context of concrete, most cement is either used in ready-mixes – where the concrete product is delivered as a fluid to the point of placement and compaction on site – or precast concrete, which includes a range of products made in factories. The majority of cements in concrete used globally at scale are based on Portland cement (PC) clinker, which was developed in the 1800s. Hydration of PC, in concrete, is an exothermic reaction and a source of external process heat is not commonly required to cure it, except for some factory made products where enhanced early strength is required.
Embodied CO2 associated with the manufacture of modern UK PC clinker in the most efficient cement works is around 0.913 tonnes of CO2 equivalent per tonne of cement (t/t) of PC. Here, the CO2 is associated with the energy – grinding and combustion of coal or alternative fuels – required for partial melting of the mineral constituents in a cement tunnel kiln, grinding of the raw clinker, and decarbonisation of limestone (CaCO3) during the clinkering process, which is an essential raw material for making the cement minerals in PC.
Efficiencies in the manufacturing process and use of alternative kiln fuels can help, but process CO2 savings reach a lower limit without changing the composition of the cement clinker or blending the ground clinker with other materials. Supplementary materials (SCMs) also known as cement replacement, include coal fly ash and ground granulated blast furnace slag (ggbs). According to the UK Mineral Products Association, they have embodied carbon of approximately 0.1kg/t and 80kg/t respectively, and have routinely been used to blend and replace a portion of the powdered PC in concrete mixes.
Such blending during cement manufacture can lower the embodied carbon to around 0.73t/t on average, but there are technical limitations, such as effects on rate of strength development, that dictate how much can be used. These materials are also becoming more difficult to obtain in some countries, primarily due to the move to renewable power generation, the UK steel industry decline and changes in practice like greater use of recycled versus primary steel. At the same time, developers of buildings and major infrastructure, including those in the UK, are increasingly demanding lower carbon concrete solutions. Manufacturers of some new low-carbon cements claim CO2 reductions by mass of concrete of between 30%-80% compared with conventional PC concretes. Some also claim savings in process water use.
Standards in cement and concrete
A wide range of PC-based cements are covered in Europe by the European Harmonised Standard EN 197 common cements, with all cements containing at least a proportion of Portland. Not all of these are provided for in the British Standard for Concrete (BS 8500) nor are all available or even familiar to specifiers in the UK.
Globally, most standards and guidance for cements and concrete are based around PCs, sometimes blended with SCMs for durability, cost and to enable embodied CO2 reduction. The cement industry in Europe is responding to these environmental and material availability issues in several ways by seeking:
- Introduction of a wider range of SCMs for use as two-component blends or combinations with PC in concrete as alternatives to fly ash or ggbs. Examples include natural or calcined pozzolanas covered by recent British Standards BS 8615
- Reduction of the PC clinker content – the clinker factor – in manufactured cements while still meeting the cement standard (EN 197) through blending with other materials like limestone and SCMs, and Development of new alternative cements that do not contain any Portland clinker.
- A further alternative to the invention of a new cement is to seek to save carbon and conserve resources through more efficient use of cement replacements, such as fly ash, by exploiting synergies, for example, in the use of powdered limestone as a third component.
Concrete durability and performance
A number of the SCM or alternative binder materials are unfamiliar in the UK and work is needed to enable UK industry to gain confidence in their performance and durability, update documents that complement and underpin EU standards, and remove non-technical blockers to enable mainstream commercial use in the UK.
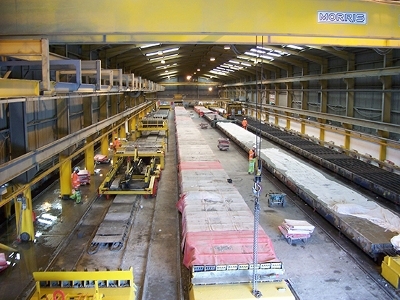
PC-based concrete mixes are typically designed to meet a specific 28-day or less minimum compressive strength requirement. New cements often do not develop their strength at the same rate as purely PC-based concretes, an aspect that may also require independent assessment with different concrete mix formulations and storage conditions for the purposes of enabling design and developing guidance.
The BRE Building Technology Group has been involved in several collaborative research and commercial projects in recent years, on an independent and impartial basis.
Depending on the application, concrete durability studies typically include assessments of rates of atmospheric carbonation and chloride ingress. These can lead to corrosion of embedded steel reinforcement – sulphate and acid resistance – both of which can degrade the cementitious binder materials. Also covered is resistance to freeze thaw or abrasion, dimensional stability and cement-aggregate interactions.
Calcium sulphoaluminate lab studies
Aether and ECO-Binder were two collaborative, EU-funded projects completed in 2015 and 2018, respectively. Both involved developing Belite-Ye’elimite-Ferrite (BYF) based low-CO2 binders, which comprised a cement clinker with a lower calcium content and higher sulphate content than PC. Three BYF cements have been tested, with cement prototypes provided to BRE by manufacturers and project partners, Heidelberg Cement, LafargeHolcim and Vicat.
BRE manufactured concrete specimens for testing in-house and by partners. These ranged from 100mm concrete cubes to full-scale concrete beams and columns, and had different compressive strength grades and cement contents. Durability assessments results were compared against established PC-based reference cements. BRE’s results showed the retention of mechanical strength, absence of swelling in water and limited drying shrinkage, which was lower than PC-based concretes. No special placing or compaction methods were required for the fresh concretes, and the water and cement contents of the mixes were similar to conventional PC concretes.
Other aspects of performance such as chloride migration and carbonation rates were assessed. Long-term monitoring of performance is continuing in marine conditions, particularly sulphate solutions and long-term strength retention in various temperature and wet or dry conditions. Activities towards developing a new European Standard for this type of cement have started and the results from these projects will help to provide evidence of performance towards these and other standards.
Alkali activated cements
Alkali activated cementitious materials (AACM) generally comprise a powdered solid aluminosilicate of binder, typically fly ash, ggbs or thermally activated clay, together with an alkaline chemical activator such as sodium silicate and/or sodium hydroxide solutions, or a solid chemical activator. A series of collaborative R&D projects have been conducted on this category, including BRE durability studies and pilot trials such as the manufacture of pre-stressed railway sleepers, concrete block pavers and roof tiles under factory conditions.
The mixes used fly ash and ggbs as binders, with sodium silicate liquid activator, and the products or test specimens showed similar performance to PC reference concretes. Tests on railway sleepers, for example, exceeded industry requirements, included the transfer strength – the point in time at which the pre-stressing load applied on the production line is released from the pre-stressing wire into the concrete – and achieved the necessary self-compacting properties, surface finish, 28-day strength and passed compliance tests for the dynamic performance and fatigue of the sleepers.
Work was supported by grants from Innovate UK with partners including Marshalls, Cemex, PQ Silicas and David Ball Group. A publicly available specification (PAS 8820) developed through the British Standardisation body BSI exists for these materials.
Non-hydraulic binder
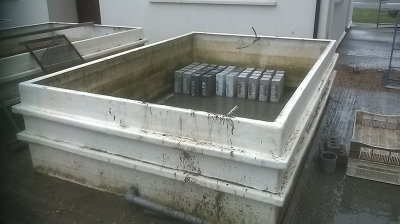
The Solid Life project evaluated a calcium silicate-based cement containing mineral phases with lower calcium content than PC, being based on the minerals CA and C3S2, rather than the C3S and C2S in PC1. The new cement is produced in existing cement kilns using the same raw materials as PC. The key difference being this type of cement is produced using less limestone and at lower kiln burning temperatures. The low-lime chemistry of Solidia cement allows raw materials to sinter, fuse and form clinker at approximately 1,200°C, compared with 1,450°C for PC. Ultimately, this leads to reduced CO2 emissions during cement manufacturing. Another key difference is that the cement is non-hydraulic – it recaptures additional CO2 during the curing of the concrete, since hardening occurs due to a carbonation process rather than hydration of the cement. The manufacturers also claim 80% recovery of the process water, from concrete production.
BRE’s assessments included creep in compression, frost scaling, resistance to abrasion and attack by acid or seawater, all of which showed similar or better performance between Solidia concrete and a reference PC concrete with similar strength. Concrete paving blocks made in industrial pilot trials also performed well. The manufacturing partners are using the results of the study as supporting evidence towards CE marking. The work, which was conducted in partnership with Solidia Technologies, USA, and Lafarge Holcim, (France and Austria) was supported by funding from the European Union in the framework of LIFE Program under grant agreement LIFE15 CCM/FR/000116.
Multi-component with limestone
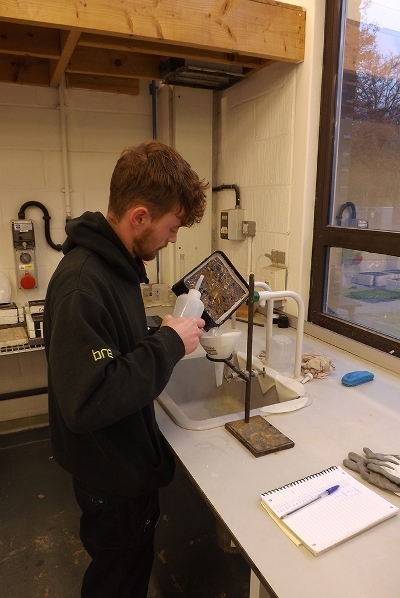
One approach to conserve supplies of ggbs and fly ash and reduce embodied CO2 in each cubic metre of concrete is through more efficient use of cement replacement materials. Recent research has shown that combinations, such as cement-ggbs-powdered limestone, cement-fly ash-limestone and cement-calcined clay-limestone, work better in a multi-component cement to potentially enable higher rates of PC replacement.
In 2018, BRE joined a project led by industry body Mineral Products Association (MPA) to develop new low-carbon, multi-component cements for UK concrete applications. The research and demonstration activities are part-funded by the government under the BEIS Industrial Energy Efficiency Accelerator programme, managed by the Carbon Trust and Jacobs. BRE is carrying out validation testing for strength development and durability of new concretes, in which 65% PC cement replacement has been achieved.
Activities are also expected to include installation of a pre-cast concrete earth retaining wall for potential long-term monitoring. On completion of the initial technical programme, recommendations will be presented to the BSI to support standardisation of low-carbon multi-component cements in BS 8500.
Modern Portland cement production is an efficient process with little waste beyond gaseous CO2. But the scale of operation makes it the largest anthropogenic source of CO2, after transport and energy.
Looking to the future, it is likely that more complex blended Portland cements, ternary and even higher order systems, as well as cements without any PC will continue to be developed and adopted to optimise the demand for new buildings and infrastructure while minimising embodied CO2 in their construction.