Low-carbon retrofit - Entopia Building, Cambridge, UK
A 1930s former telephone exchange has been refurbished to create the headquarters of the University of Cambridge Institute for Sustainability Leadership (CISL).
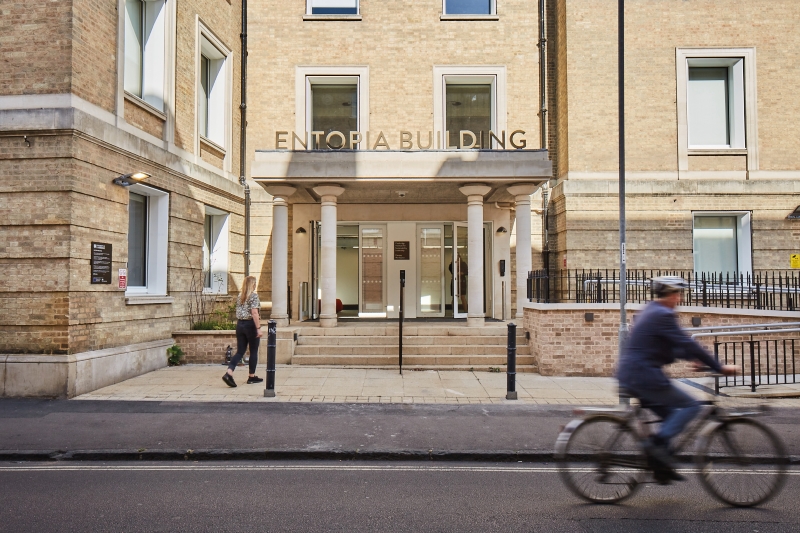
Wendy Bishop, Associate and Passivhaus Designer at architect firm Architype, UK, delves into the low-carbon retrofit of the Entopia Building.
How did this project come about?
The Cambridge Institute for Sustainability Leadership had outgrown their previous office. It didn’t support collaboration or demonstrate their organisation’s values. When a suitably central university building became vacant, there was an opportunity to demonstrate best practice in sustainable and healthy retrofit, addressing a number of demanding sustainability and wellbeing targets – and showing how this could be done cost-effectively to help inspire their network.
The project brief was developed by John French, who Architype had worked with on the exemplar Enterprise Centre for the University of East Anglia, which also set many demanding environmental targets and was the largest Passivhaus building of its kind in the UK.
What have been the challenges and key considerations to transform a six-storey, 1930s telephone exchange into a more sustainable, modern building?
Because Entopia is in a conservation area, it was always going to be a challenge to get planners to accept changes to the exterior of the building.
Moreover, a key consideration for a low-carbon refurbishment is that, if you are keeping lots of existing materials, the embodied carbon of any new materials you bring in is even more important – that is why we did things like retain the existing raised access floors as the floor finish in many areas, rather than replace the worn-out carpet tiles with a new floor finish.
The other important thing is to try and find out as much as possible before starting work – for example, surveys and opening up the building so that there are minimal surprises when work starts onsite.
Tell us more about the ‘whole-life’ strategy and ‘fabric-first’ approach deployed?
We looked at whole-life and lifecycle carbon using our innovative ECCOLAB carbon software to quickly assess the impact of different design choices. These decisions were tied into circular economy thinking and making sure items are durable, repairable, demountable and reusable.
Energy efficiency first is our guiding mantra. A fabric-first approach ensures the focus was on insulating and making the building airtight, and replacing windows with high-performing ones to get energy use right down before we even considered adding things like photovoltaics.
What have been the key technical developments in the retrofit of the building?
Technically, the challenge was to achieve Passivhaus EnerPHit certification for a building of this scale, and we believe this is the largest EnerPHit office in the UK.
We did many studies to demonstrate that replacing the Georgian sash windows would benefit the thermal performance of the building, cut emissions and dramatically improve daylight for occupants – which the planners did agree to. The existing windows, with the original transforms and mullions omitted, were replaced with triple-glazed, high-performance Passivhaus windows. The frame was recessed to maximise the glazing – which increased by 60% – and therefore daylight entering the building. The heat demand was in turn reduced by 35%.
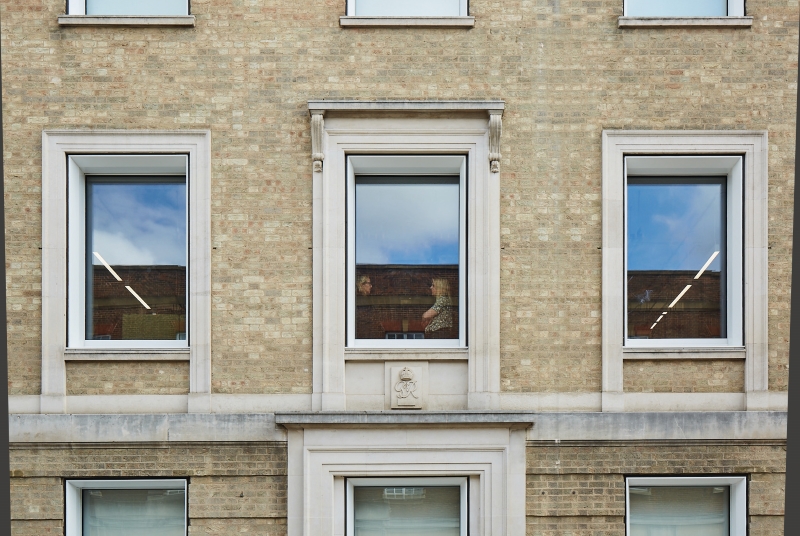
The introduction of a mechanical ventilation heat recovery with a top-up air source heat pump and openable windows – in place of natural ventilation – with localised air conditioning, helped create much better air quality and thermal comfort throughout the year.
We also had to understand and carefully model the construction build-up of the existing building to ascertain the optimum way to internally insulate the building. This included using materials that would work with the existing masonry – such as wood fibre insulation and cork render – which are breathable and natural.
We changed the servicing strategy, which freed up roof space for a new roof terrace, with services consolidated in the basement. Photovoltaics (PV) on the roof terrace help offset some of the very small amount of energy the building uses, with reused steel in the new PV array.
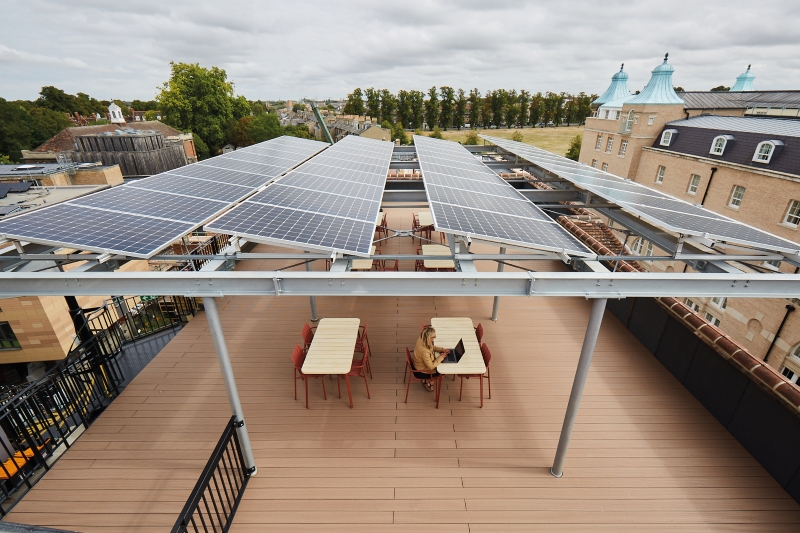
What specific bio-based materials were used and why?
Bio-based and non-toxic materials are much better for people’s health. Cork render and wood fibre insulation were chosen to regulate moisture movement and insulate the masonry internally.
Recycled newspaper (cellulose) acoustic spray to the existing concrete soffit allowed us to soften sounds in the space and give maximum head height and daylighting internally. Hemp insulation in some areas, 15% bio-based Fermacell plasterboard and timber studs (instead of metal) for the internal partitions helped increase the quantity of bio-based materials.
On the furniture and fittings, interior designer Eve Waldron put a lot of thought into maximising bio-based materials, for example, experimenting with combining reused table bases with new bio-based tabletops in materials such as strawboard and bamboo ply, and reupholstering second-hand chairs with hemp fabric.
Can you elaborate on the insights gleaned through the development and how these impacted the project targets?
The project began with a very ambitious target for bio-based materials of 70%, which is very difficult to achieve if you are retaining the structure, replacing windows and not bringing in much new structure – where there is ability to add a large quantity of bio-based materials through timber products. The final figure of 35% bio-based materials by mass is a result of very careful thought and effort by the design team who worked very hard to select the optimum materials.
Given that we believe this is the largest EnerPHit office in the UK, it has shown that the standard can be achieved at scale. Combining the EnerPHit standard with BREEAM Outstanding and WELL targets shows how much the standards can be complementary, even if that can result in a limited choice in specification. For example, finding the required tap heights for the WELL standard combined with low-water flow rates to meet the BREEAM standard.
Achieving EnerPHit certification required careful modelling by the Passivhaus designers and careful monitoring by ISG on site. This included air-tightness testing of a small portion of the refurbishment to check the correct strategy was adopted.
The engineers BDP, UK, co-ordinated with the Institute and the University to make sure that WELL requirements were met, with some credits still being finalised. This required commitment on all sides to achieve such a demanding goal will result in a great workspace for the CISL team and visitors.
High standards
Passivhaus is a building standard for energy efficiency and ultra-low energy heating or cooling, from The Passivhaus Trust.
The Passivhaus EnerPHit standard is for an economically and ecologically optimal energy retrofit.
BREEAM is used to specify and measure the sustainability performance of buildings. Awarded by the Building Research Establishment (BRE), there are currently six different BREEAM certification levels.
WELL standards are used to measure the wellbeing of occupants in a building by six factors: equitable, global, evidence-based, technically robust, customer-focused and resilient.
How were circularity principles integrated into the design of the building?
The reuse of the building structure is inherently circular, and the project went to great lengths to meet circular economy goals. This included redirecting materials that could be removed for secondary uses – for example, donating old furniture to community groups and making sure waste materials were recycled rather than dumped. Newer materials have incorporated recycled materials and use as few as possible virgin materials.
Everything was selected for its durability with ease of repair in mind to help extend its useful life.
The reception desk at the entrance epitomises this approach – ISG, UK, the contractor, found it was being removed from its former home and potentially scrapped. They arranged for Benchmark, UK – the original furniture maker – to remove it and take it back to their workshops to adapt it slightly to the new space.
Unfortunately, the stone top was cracked in the removal process, but we were keen to not simply replace it, or invisibly repair it. Instead, the crack was mended using a Japanese kintsugi-style technique – the process of repairing ceramics using golden-coloured resin to give them a refined aspect – to celebrate the desk’s journey.
LED fittings were also reclaimed – 350 in total. These were inspected by the manufacturer and given a new warranty, which led to the building gaining a BREEAM innovation credit. Steel was reused for the rooftop PV canopy, while other parts that were reused include the existing raised access floor, lift, generator, cable trays, cables and electrical ducts.
How do you see the Entopia Building influencing the built environment?
Retrofit remains a key issue for the industry and is vital to meet zero-carbon goals. A key goal of the project was to inspire and influence industry to show that beautiful and collaborative workspaces within existing buildings are possible when high aspirations are set and the whole client and design team work together to achieve them.
The institute has published a detailed case study on its website that will be a hugely useful resource for all, including students, and will be updated as monitoring data becomes available. Despite only being open for a few months, the project has already generated much interest with many visit requests and is being used as an exemplar case study by the UK Green Building Council and the Passivhaus Trust.
Did you know?
350 reclaimed LED lights
21,000kg of CO₂e saved through reclaimed materials, such as the photovoltaic rooftop canopy
84% of carbon saved per m² compared to a standard office fit-out
62,332kg CO₂e avoided in construction materials
Source: University of Cambridge Institute for Sustainability Leadership, Building Entopia – The story behind the ultra-sustainable retrofit of CISL’s new home in Cambridge