Lightsails scaled up for space exploration
Scalable, nanotechnology-based ceramic lightsails could speed up space travel.
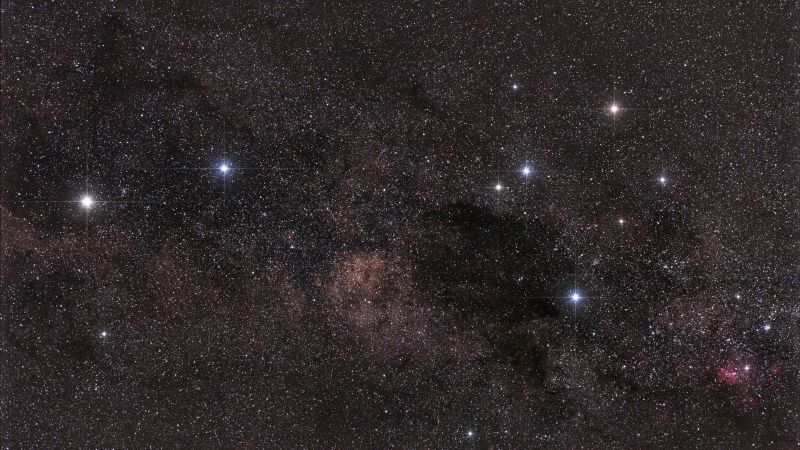
A partnership between Delft University of Technology, the Netherlands, and Brown University, USA, reports to have created the thinnest, large-scale reflectors ever made, while reducing production time from around 15 years to one day.
The current prototype made of silicon nitride (SiN) measures 60mm x 60mm and is 200nm thick covered in billions of nanosized holes. If scaled up, it would extend the length of over seven football fields while being only 1mm thick.
Lightsails use laser-driven radiation pressure to propel spacecraft at high speeds and can be massive sheets with nanoscale thickness.
The Breakthrough Starshot Initiative unites thousands of researchers to attempt to reduce a 10,000-year journey to the nearest star outside our Solar System to just 20 years.
Dr Richard Norte, Associate Professor at TU Delft, notes, 'We’ve engineered SiN into ultra-thin reflective metamaterials, which is where the novelty lies.'
Instead of using electron beam lithography to precisely write each tiny nanoscale hole into the material individually, they have used photolithography to pattern slightly larger holes. 'This approach floods the entire area with light, defining millions of holes simultaneously in seconds, dramatically reducing fabrication time,' notes Norte.
The team say the material is noteworthy because of its high-aspect ratio. 'This is not just another step in making things smaller; it’s an entirely new way of thinking about nanotechnology,' explains, Norte. 'We’re creating high-aspect-ratio devices that are thinner than anything previously engineered but span dimensions akin to massive structures.'
Their process combines topology optimisation and neural network optimisation techniques, which have previously been distinct areas of research, highlights Norte. Together, they create a novel, pentagonal-lattice-based, photonic crystal reflector.
The project simultaneously considers performance (acceleration of the sail) and manufacturing constraints (fabrication costs). 'This hybrid optimisation method led us to discover entirely new sail designs,' comments Norte.
This includes a gas-based etching technique to suspend ultra-thin structures without tearing them. The etch delicately removes the material under the sails, which the team reports as robust once completed.
'Fabrication is typically the most challenging stage, where liquid-based methods cause destructive surface tension forces,' reveals Norte. This process avoids this, he notes, requires no subsequent cleaning and allows the structures to handle higher optical powers. 'Additionally, our photolithography method creates uniform hole patterns without seams, enabling uniformly suspended sails.'
They can currently scale up to the maximum wafer size available, around 300mm-diameter wafers. 'Optimal sail size depends on balancing laser beam size and the weight of payloads, as heavier payloads require proportionally larger sails to ensure effective acceleration,' reflects Norte.
The group is now preparing experiments to push the membrane sails across centimetre distances against Earth’s gravity. They highlight that while it might not sound far, it would be 10 billion times further than anything yet pushed with lasers.
Norte says, 'The greatest challenge is integrating expertise from thousands of scientists worldwide into a complete, functional, lightsail spacecraft. This requires miniaturising cameras, communication systems and power supplies into a total payload mass of about a gramme – a formidable challenge itself.'