Increasing the loading rate for nuclear waste encapsulation
Technology company Lucideon, based in Staffordshire, UK, has forged a partnership with NUVIA UK, to bring its MIDAR-Augmented Lower-cost Lower-carbon Encapsulation Technique (MALLET) to the nuclear waste management sector.
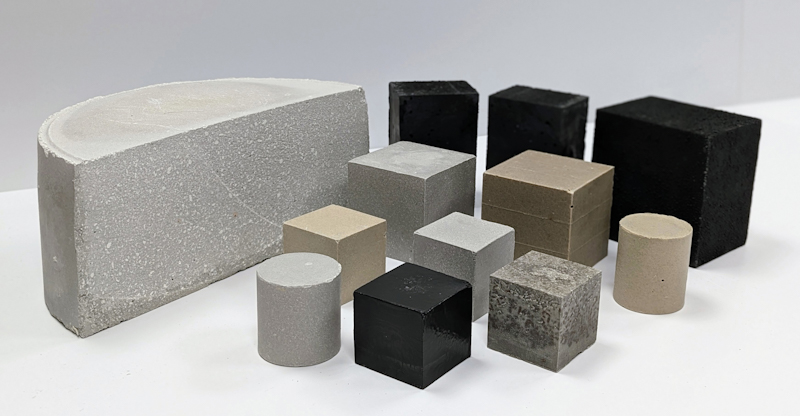
MIDAR is a geopolymer technology that uses a low-temperature chemical reaction to consolidate a refractory material and form a robust body with high strength and chemical stability. The resulting material, says Lucideon, is suitable as an encapsulation and immobilisation agent by incorporating a solid or liquid waste stream into the inorganic solid matrix that is formed during the reaction.
MALLET was developed in response to several nuclear industry waste disposal challenges, most significantly low percentage load rate for difficult wastes, or in some instances no viable route of disposal. The new system is reported to provide a cost-efficient method of managing intermediate level waste streams (ILW), including oils, graphite, zeolites, sludges and ashes.
MALLET addresses these challenges by increasing loading rates through geopolymer formulations where the waste is encapsulated fully and homogenously throughout the matrix using existing equipment.
Current methods for encapsulating Magnox Sludges can encapsulate approximately 30% by weight meaning 70% is grout. MALLET is reported to encapsulate 70% Magnox Sludge by weight meaning 30% is grout. This could lead to significantly lower disposal costs.
Richard Goodhead of Lucideon says, '[MALLETT] offers substantial benefits over traditional forms of ILW stream disposal techniques such as Portland Cement, including a significant reduction in carbon emissions as energy intensive cement is not used, and as MALLET raw materials do not require high-temperature firing and it does not produce CO2 during the chemical reaction.'
He explains that waste volumes are also reduced as MALLET makes use of foundation industry wastes such as ground granulated blast furnace slag and fly ashes within the formulations – in turn, closing the cycle, resulting in a considerable reduction in waste processing and disposal.
'The technology is also compliant with Waste Acceptance Criteria and is chemically stable,' says Goodhead.
'The system uses the same technique to produce the encapsulant as current techniques, therefore safety measures are already in place,' adds Euron Roberts of Lucideon. 'Additionally, the mixture is contained in an enclosed system when it is being mixed so that splashes are contained. The process produces negligible exotherms.'
The work is currently at lab scale. Roberts says, 'NUVIA will be upscaling the technology, but we do not envisage this being a problem because we have already used the encapsulation materials in 3,000L tanks, and this is larger than they will be used at in this application. We can have the technique viable for deployment in 12 months.'
Lucideon’s development of the technology has been supported by Innovate UK.