Get talking – investing in metallography training
Crysta Haigh and Richard SA Brown MIMMM of M&C Educational Training Services, UK, discuss why there needs to be investment in metallography training.
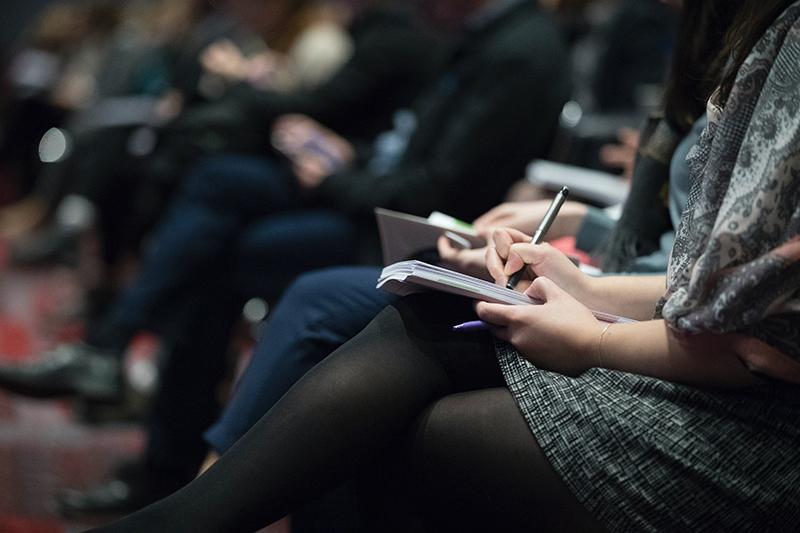
Metallography is the study of the microstructure of all types of metallic alloys. Using specialist techniques, scientists and engineers can observe and determine the chemical and atomic structure and spatial distribution of the constituents, grains, phases, or inclusions in metallic alloys.
So, is this a useful skill to understand more about? Of course. Companies need microscopy analysis to protect their products, especially if they are patented. They also need it to investigate why things fail if integrity and quality are sub-par.
We have noticed there is a development need to give employers and their workforce a better base knowledge for metallography in the workplace so more can be done in-house.
Thomas Whiskin, from ASAMS Ltd, a metals testing laboratory in Great Yarmouth, UK, notes, ‘We used to deal with a lot of companies that would have, in the past, had someone onsite who was either trained, or had an interest in metallurgy, but I don’t think that is the case anymore. If there is anyone, then they are usually someone who operates from what they have learnt from textbooks or their degree.
‘The skill of metallography is to diagnose and fix problems during the process rather than after the failure has occurred. If more people had the training, then it would enable them to carry out that quick look during the process rather than having to stop everything and then go back and restart it all over again.’
The foundation of practical metallography is built upon examining materials on a macro- and micro-level.
Macro-examination is a procedure in which a specimen is etched and evaluated macrostructurally at low magnifications, typically x10 or lower. It is a frequently used technique for evaluating steel products such as billets, bars, blooms and forgings.
Micro-metallography is longitudinal, tapered sections and is performed on samples either cut to size or mounted in a resin mold. The samples are polished to a fine finish, normally with one-micro-metre diamond paste, and examined unetched as these show inclusions which can change on etching. Micro-examination is performed for several purposes, the most obvious of which is to assess the material’s structure.
This useful technique is deployed within the workplace across many sectors. It is important to not only understand the theory, but also the practical of the ‘why’ and ‘how’ of the process, especially for failure investigations.
Iain Macleod of Howco Ltd, a high-grade alloy specialist in Glasgow, UK, adds, ‘Metallography is important so companies have a deeper knowledge of the basics of what they do. This is a very good indicator of the mechanical properties of steel and its ability to perform under service conditions. That is especially true with corrosion resistant alloy (CRA) materials such as stainless steel and nickel alloys. Many material specifications of CRAs have metallographic requirements built into them, which are often the most important feature of those specifications.
‘With fewer companies offering the skills to develop, and fewer colleges providing this training, manufacturers often outsource this to test laboratories rather than have any capability to do it in-house.’
Steven Chambers, from non-destructive testing firm Morgan Ward, in High Peak, Derbyshire, UK, echoes the issue around a lack of investment in training. ‘We are in a dangerous position of losing the skills that made the UK the best in the world at manufacturing metal, with a gap in the market created by lack of funds, an age gap and outsourcing.
‘The age demographic within metallurgy is a vast chasm between the old generation and the new, and sadly people are leaving or retiring faster than we can replace them because we don’t see these skills as important anymore. These are the basics of our industry. Without metallography, you are stabbing in the dark.
‘Preparing samples is an art form. If you get your sample presented incorrectly, it can give you a false indication. Learning how to get your sample flat, learning how to prepare the edges of your component is so important. People need to be taught that you have to get the basics right.’
The basics of metallography should be a staple learning curve for everyone within the industry. This is the ‘bread and butter’ of understanding how metals are affected by heat, corrosion, forging, etc. Macleod says that ‘this kind of learning is essential because it directly links into the transformation of metal during the heat treatment process, and that is what metallurgy is all about. It is about processing the metal from As-Cast through to raw product, moving on to heat treatment, and essentially that process is all about producing a desired microstructure’.
It is clear to see metallography is a basic requirement, and that training is just not being given. This is costing companies to outsource this work when they could – if they had the resource capabilities – train a few employees on a metallography course and save money by having the samples prepared and examined in-house.