Energy-harvesting wooden floors
Wooden floors are being transformed into nano energy generators to switch on lightbulbs indoors in novel proof-of-concept displays.
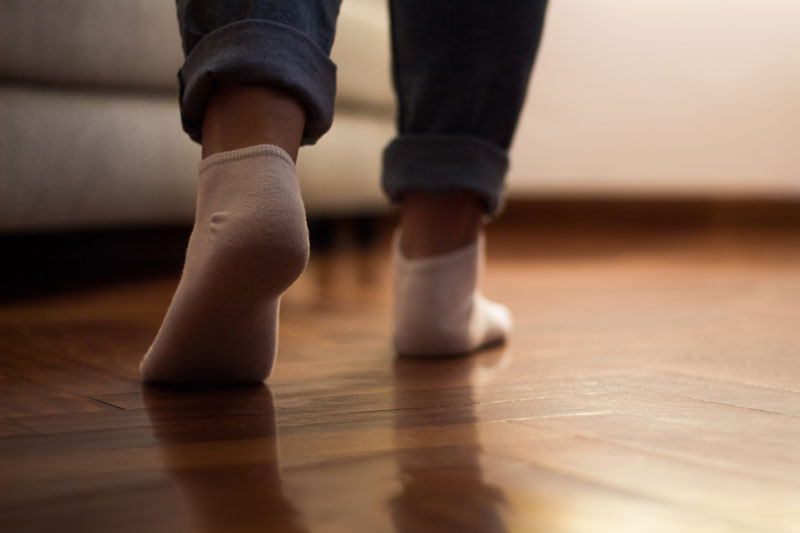
Researchers in Switzerland, at the Eidgenössische Technische Hochschule (ETH) Zürich and the Swiss Federal Laboratories for Materials Science and Technology (Empa), have achieved this by functionalising wood. They have applied a silicone coating of poly(dimethylsiloxane) (PDMS) and embedded nanocrystals to change the properties of a traditionally triboneutral natural material with limited ability to generate electricity.
Dr Guido Panzarasa, Group Leader at ETH Zürich, explains, ‘Wood is not triboelectrically active, but has excellent mechanical properties and a highly versatile microstructure. PDMS, a common silicone, is highly tribonegative and compliant, but very soft. Metal-organic framework (MOF) nanocrystals, such as ZIF-8, are tribopositive and with a large surface area, but fragile. Incorporating these materials in wood provides them with mechanical stability and additional features such as enhanced roughness and contact area. The resulting composites can then be assembled into a highly efficient and stable triboelectric nanogenerator. Furthermore, the functionalisation does not affect the building properties of wood and even leaves its aesthetic appearance unaffected.’
The team has used spruce wood as a scaffold for the generator – a common wood for building applications – by sandwiching two pieces of functionalised wood between electrodes. Through periodic contacts and separations when stepped on, the wood pieces become electrically charged – a phenomenon called the triboelectric effect. The electrons can transfer from one object to another, generating electricity. Metal electrodes are attached on the back side of each functionalised veneer to collect and transfer the electrostatically induced charges through an external circuit.
‘This is a very simple schematic…We start from two, thin, 1mm-thick, wood slices which we call wood veneers,’ Panzarasa explains. ‘Each veneer has two large faces, one is covered with a metal electrode, while the other is functionalised with either PDMS or ZIF-8 and is free to contact one face of the other functionalised veneer. When the faces are brought into contact, the PDMS-wood layer acquires charges from the ZIF-8-wood layer, this happens during the pressing. Then, when the pressure is released, the two surfaces separate again and, because there is a charge of separation on them, they are electrically charged.’
According to the team's research published in Matter by Cell Press, the ZIF-8 particles are grown in situ and the PDMS applied through spin coating and curing. ‘The resulting surface chemical and morphological changes increase the ability of wood to donate (ZIF-8-modified wood) or acquire (PDMS-modified wood) electrons during periodic contact-separation cycles and, consequently, the amount of electricity produced,’ the paper reads.
The team will now seek to further optimise the nanogenerator with chemical coatings that are more eco-friendly and easier to implement. Panzarasa adds, ‘The main challenge, at least from our viewpoint, is the associated electronics for the management of the produced electricity.’