Copper makes good on developing high-strength steel from recycled materials
Copper - an element previously cast aside because of the detrimental effects it can have on certain types of steel – can deliver light-weight, high-strength steel made from recycled material, say researchers from the University of Sheffield, UK.
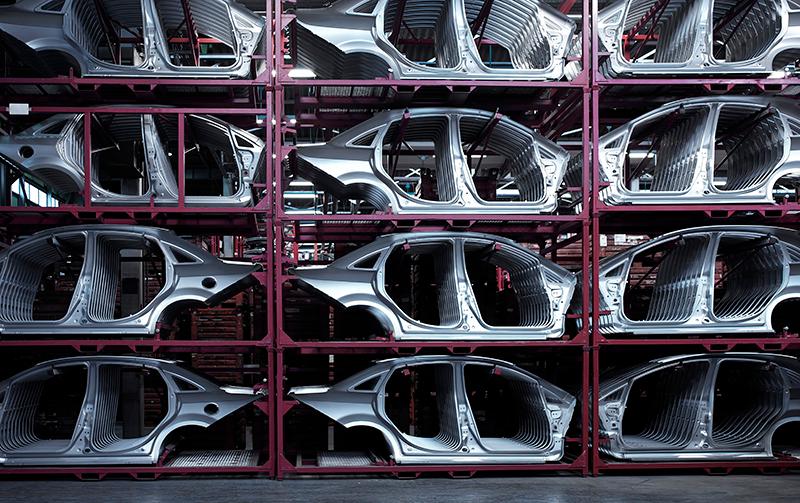
Copper – an element previously cast aside because of the detrimental effects it can have on certain types of steel – can deliver light-weight, high-strength steel made from recycled material, say researchers from the University of Sheffield, UK. They claim the discovery can be adapted to mass manufacturing and could put lighter weight vehicles on the road.
By fabricating and processing ultra-fine grain alloys, the research produces steel with a strength of 2GPa – for example, a 1cm diameter wire would be capable of holding a weight of 15t. The resulting material also has an elongation of 45%, ductile enough to be formed into complex shapes.
Copper is increasingly found in recycled steels from used cars and other engineered items that contain electrical wiring. With steelmakers looking to use more recycled materials in their production process, copper is now being seen as unavoidable by the industry, notes the Sheffield team.
‘In conventional steels, copper results in what is called hot shortness, where the steel cracks during hot working,’ says Professor Mark Rainforth of Sheffield’s Department of Materials Science and Engineering.
‘Copper levels have to be reduced to very small amounts to prevent this occurring. This is increasingly challenging where recycled steel is used as the feedstock material as steel scrap contains copper.’
To overcome the issue, the team has investigated how the copper atoms distribute themselves within the matrix, with the new steel engineered to avoid hot shortness through copper alloying and manipulation of the recrystallisation process through intragranular nanoprecipitation.
‘The rapid and copious nanoprecipitation not only prevents the growth of the freshly recrystallised sub-micrometre grains but also enhances the thermal stability of the obtained ultra-fine grain structure,’ the paper, published in Nature, reads.
The team attains the ultra-fine grain structure by reducing the grain size and preventing its increase during processing.
‘Strategies to do this, so far, have resulted in a steel with very poor ductility,’ Rainforth explains. ‘The key to the process is that copper is made to precipitate just at the right time. The steel is processed to give recrystallisation (to give the ultra-fine grain size) and then, precisely at the right moment, copper precipitates are formed which pin the recrystallised grain boundaries, freezing in the ultra-fine structure.
‘Furthermore, the beauty of the fine copper precipitates is that, while they pin grain boundaries, they do not appreciably hinder dislocation flow. This means that very high ductility is achieved – unlike conventional steels where carbide precipitates are used to pin grain boundaries which results in poor ductility.’
The rapid precipitation within the crystal steel grains has been studied using advanced imaging at the US National Institute of Standards and Technology.
‘[This] showed the precise structure and location of the copper precipitates,’ Rainforth says. ‘In addition, atom probe microscopy and synchrotron studies, that allow the location of each atom in the structure to be determined, was undertaken at Beijing Advanced Innovation Centre for Materials Genome Engineering and the State Key Laboratory for Advanced Metals and Materials, University of Science and Technology Beijing, China.’
According to Rainforth, ‘The new steel employs a very simple manufacturing process. This is essential in ensuring that the process can be upscaled using the steel making plant that already exists.’
The team will now explore scaling up, as well as evaluating mechanical properties such as creep strength.