Changing gears - materials testing in the automotive industry
Materials testing evolves as the automotive industry shifts towards electric vehicles.
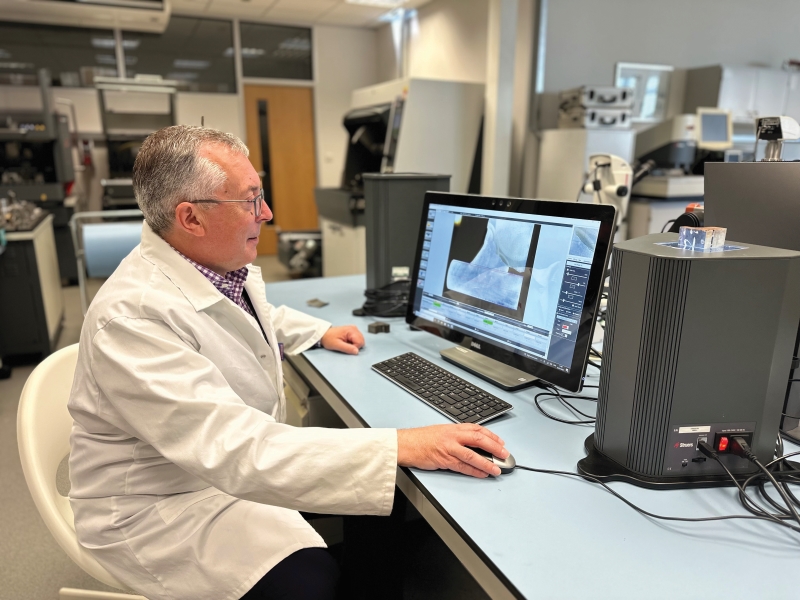
Over the years, well-established testing routines for internal combustion engines (ICE) and bodywork have been implemented globally across original equipment manufacturer (OEM) sites and their materials laboratories.
Metallographic procedures, integral to ensuring material integrity, have undergone iterative enhancements in line with the automotive industry’s continuous improvement.
Traditionally, car manufacturers have focused on refining and optimising vehicles with a single drivetrain, transmission and engine size, contingent upon the specific model and target market.
The longevity and efficacy of testing protocols for elements such as trim, safety systems and paintwork have fundamentally remained the same, even as technological advancements and evolving consumer preferences bring about nuanced changes.
But while certain testing procedures may retain their simplicity, others, such as paint-thickness requirements or intricate specifications for luxury-marque, dash-wooden veneers, demand more rigorous examination.
Regardless of the intricacy involved, automotive manufacturers will always need to subject their products to in-depth testing during quality control (QC) to confirm that the delivered products adhere to specified standards. QC, in this instance, certifies products are delivered to consumers free from defects – maintaining both product integrity but also brand reputation, and protecting the user from risk or harm through failure.
For automotive manufacturers, the rules of engagement have long been simple. But as the car industry drives towards changing energy requirements and fizzles out diesel and petrol engines, it follows that testing procedures need to evolve so both quality and new material specifications meet production and consumer needs.
We must now be mindful of the powertrain and, more specifically, the zero-emissions power or energy source used in vehicles, whether designed for passengers, light or heavy commercial and goods vehicles.
Battery-operated
Lithium battery testing is a case in point. The lifetime and operational performance of a lithium-ion battery is dependent on microstructural elements like particle size and layer thickness fluctuations.
Recent work with battery manufacturers has helped define metallographic testing requirements, which in turn can be used as a blueprint for new battery suppliers.
In a recent report on how to avoid delamination when sectioning and preparing lithium-ion batteries, Struers describes the process used to inspect these characteristics on large battery surfaces. The results of this could help optimise production process parameters and derive manufacturing tolerances.
Cutting, vacuum impregnation and grinding/polishing processes have been determined, primarily to accommodate the large electrode sample size. The results obtained using the prescribed methodology are reproducible, and the sub-micrometre finish facilitates further inspection and analysis.
This is one example where metallography is being used proactively to help battery developers.
Meanwhile, as technology improves, new batteries are developed, and the testing will ultimately move further forward.
Round cells are being used for the first time in the sixth generation of electric mobility batteries from the BMW Group. With a diameter of 46mm and two different heights of 95mm and 120mm, the new cells are designed for what BMW are calling ‘Neue Klasse’ architecture. Here, the storage system takes on a supporting role in the body structure and can be integrated flexibly into the vehicle chassis platform.
And despite the continued evolution, current or next-generation systems are already in the process of being superseded by solid-state advances, maybe not quite in practice, but certainly in terms of wishful thinking.
While the batteries recycling and energy-storage solutions are becoming fairly commonplace, the solid-state solution takes this ‘problem’ to a new level in terms of safety, ease of handling and perceived compliance. It is no wonder that early OEM adopters are mid-scramble to realise this battery option.
A large German automotive manufacturer is already taking the lead by setting the standards for battery acceptance and controlling the supply chain accordingly. This is undoubtedly the thin edge of the wedge as more global OEMs realise that, while the playing field has changed, they still get to control what happens with the ball. Or, at the very least, get the first line out.
In service
Recently, Struers has talked with the materials laboratories of several automotive manufacturers to find out what they thought would be the significant change in their testing regimes as we move away from ICE.
Apart from electric vehicle (EV) start-ups, all laboratories estimated their workload to lighten as the inspection and testing of parts such as engine blocks, piston caps and cylinders fell away.
It is highly likely this will happen, but equally, we will have the new direct-drive systems, and as motive systems are improved, there will always be the requirement to approve testing processes as reality (or production) meets R&D.
Given the amount of torque that drive components are subject to while in continuous operation in EV or battery EV direct-drive assemblies, hardness testing will undoubtedly be more relevant in profiling transmission components.
Typically, a fully automated hardness tester can be left to run unattended, often overnight, with the user collecting the results the following morning. Recent innovations have even allowed for multiple samples to be pre-programmed on motorised stages, allowing test work to be undertaken on several batches of test components at once. Hardness profiles can be saved and reported on according to the production and test laboratory requirements.
Wear factors are already being considered in terms of EV lifetime, and testing precursors may allow manufacturers to extend service intervals and service life as they begin to understand these drive systems more fully and the required materials to increase longevity.
On brief
The metallography or testing requirements we see right now are pretty straightforward. The car manufacturers are not developing new alloys or base materials – although the interest in application is definitely there.
They may use some additive manufacturing but, again, testing requirements are pretty much nailed down. They may look to exploit new joining technologies – look at how the prevalence of rivet and press joining, particularly in aluminium bodywork, has taken off in passenger vehicles – but mostly, their brief remains the same, that is to perform a QC role that supports production and facilitates manufacturing capacity.
However, what is changing and will continue to change, is how repeatable and consistent these procedures will need to be going forward. Technology and materials advances are driving this need for consistency and the use of automated systems.
Volume is also a factor, and while the automotive materials laboratory can make checks for paint thickness or veneer lamination as one-off failure investigations, the number of samples tested in battery manufacture and quality procedures will be significant.
It is here that the volumes once seen in engine testing may be replaced – the difference will be incumbent on metallographic equipment manufacturers automating preparation methods as much as possible to provide the repeatability, consistency and throughput speed required.
Imagine then, a fully automated preparation solution. Load up the specimens, select the method and allow the machine to do the rest. It is even better if it can do the routine sample quality procedures and has the flexibility to run those fast turn-around “one-offs” that design and proto-typing are crying out for.
Here, samples are prepared regardless of operator experience or expertise, and the metallographer is relied upon to simply read and report on the findings.
Undoubtedly, there are challenges ahead for the automotive industry as the reliance on oil (and gas) is superseded by new energy and motive sources. Cars will change to accommodate this, as will the factories and supply chains that make them. The product and component testing will remain constant, and these requirements will only become more demanding as the technology advances.
As driverless cars appear, we may also see fully robot-approved quality releases across automated factories, but metallography will always be required as technological advances are made.