Carbon-loving membrane materials absorb emissions
A fabrication method for gas membranes is set to overcome the bottlenecks in selectivity and permeability to absorb carbon emissions in industrial settings. Shardell Joseph finds out how.
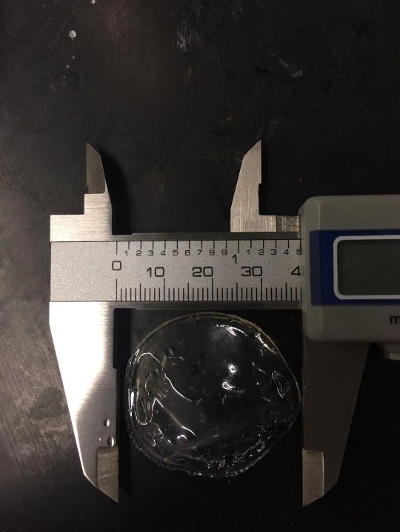
Gas membranes that can withstand temperatures of up to 500°C and have potential for large-scale carbon capture in industrial plants are the focus of research at the US Department of Energy’s Oak Ridge National Laboratory (ORNL) and the University of Tennessee, USA. The new membrane is made using a fluorinated polymeric material, with researchers claiming it is operationally simple to construct with readily accessible starting materials.
‘Membrane separation is one of the most energy efficient processes for gas separation. Especially in the case of carbon dioxide separation from a flue gas. It could afford significant energy savings compared to ethanolamine derivatives or basic inorganic absorbents,’ says Ilja Popovs, Researcher at ORNL.
‘Membrane separation would require lower energy input because CO₂ is directly separated from the flue gas by transporting it selectively across the membrane, in this case, pressure gradient across the membrane acts as a driving force for this separation process.’
He explains that membranes for gas separation are usually made from polymers such as polyimides or polyetherimides. Typically, these ‘are prone to failure when operated in chemically aggressive environments and at relatively high temperature and have relatively modest selectivity and permeability performance’. They generally perform below the Robeson upper bound, a known boundary that constrains how selective and permeable most materials can be before these rates start to drop.
‘Our most recent work demonstrates a straightforward way for the introduction of fluorinated functionalities into the carbon molecular sieve membrane materials using readily available fluorinated polymeric material,’ Popovs adds. ‘In turn, CO2 separation performance of the membrane prepared from the fluorinated material is markedly better compared to the membrane prepared from a non-fluorinated precursor.’
When comparing performance, the new membrane reaches above the upper bound of the Robeson plot. The team also claims it shows improved selectivity toward CO2 even at 90% relative humidity conditions. The membrane is prepared using a sol-gel method. ‘Essentially, a fluorine-containing substrate that also contains nitrile group and arylether group is polymerised using strong Brønsted acid (CF3SO3H) as a promoter/catalyst,’ Popovs notes.
The obtained material has a high amount of fluorine atoms in the structure rendering it hydrophobic. It is then washed with water and ethanol and dried, leaving a free-standing film.
‘Next, this film is placed in a tubular oven where it is carbonised at 500°C under a very slow stream of nitrogen gas affording a carbon molecular sieve-based membrane,’ Popovs says.
The discovery is said to expand the limited library of practical options for carbon-capture membranes. The team will continue to develop the membrane for future commercialisation.
‘We were able to easily scale up the synthesis to hundreds of grammes and, in the future, we are planning to scale it up even further,’ Popovs explains. ‘However, field-test demonstration and deployment are still several years away.’