An insight into the manufacturing industry during a pandemic
As UK manufacturing works towards full capacity operations, there are significant challenges ahead with varied experiences within the sector. Shardell Joseph investigates the pandemic’s impact and the measures being implemented to continue production.
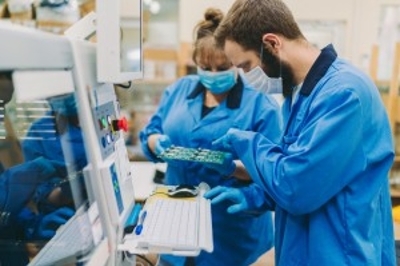
UK manufacturing is said to be experiencing a continued recovery following disruptions due to COVID-19, according to the latest IHS Markit/Chartered Institute of Procurement & Supply (CIPS) manufacturing report published in October.
The report records that the Purchasing Managers Index (PMI) for UK manufacturing fell slightly to 54.1 in September, down from August’s two-and-a-half year high of 55.2. However, the PMI has remained above its no-change mark of 50.0 for four successive months.
Despite the easing of the rate of growth, output has increased for the fourth consecutive month in September. The reopening of operations, returning of staff and improved inflows of new work have resulted in higher production, according to the report.
‘Manufacturing made solid progress towards recovery in September, with just a minor step back from August’s two-and-a-half-year index high. New pipelines of work increased for the third month in a row and export orders [are] the strongest for almost two years,’ says Rob Dobson, Director at IHS Markit.
Nevertheless, a report from trade body Make UK and bank Santander forecasts that it will take until 2022 for manufacturing to recover its pre-COVID-19 growth track, costing a potential £35.7bln in Gross Added Value (GVA) this year alone. It highlights that total manufacturing GVA could be between £6.8bln and £16.5bln lower in 2022 compared to the pre-COVID-19 forecast, and that manufacturing investment could decline between 1% and 9.7% in 2020.
The bigger picture
To manage the manufacturing sector’s response to the pandemic, Make UK says it is imperative to continuously review how it is faring. COVID-19 has disrupted activities in such a seismic manner that few parts of the economy have been spared. This was confirmed with the GDP result for Q1 2020 which reported an average 2% decline in national earnings since the previous quarter.
‘What is worrying, however, is that the decline in GDP for Q1 was thanks to a huge drop in activity in March alone,’ says Verity Davidge, Director of Central Policy at Make UK. Like any other industry, each company has been affected and has responded differently, dependent on factors such as size, specific sector, financial resources and other variables.
‘It really depends on the manufacturing company,’ insists Tony Summers, Partner and Head of Manufacturing at accountancy firm MHA Carpenter Box – a sector specialist and sponsor of manufacturing forum METALL. ‘Some have adapted remarkably well and were in the right markets to enable them to do that. Others have struggled, both in terms of falling demand and being able to make the manufacturing process socially distant.
‘There have been several instances across the country where a number of staff at different manufacturing companies have tested positive for COVID-19 and the factory has been shut as a result. Indeed, in a survey we carried out, 80% of manufacturers had struggled with social distancing.’
Make UK reports that the national accounts indicate steep declines in services, construction and parts of the manufacturing sector, such as motor vehicle sales. On the other hand, the pharmaceutical and cleaning products industry witnessed a boom in demand demonstrating the manufacturing sector’s importance to the UK in a time of crisis.
‘Most…firms have continued to operate albeit at levels below their pre-COVID-19 levels. Although the results remain mixed, the latest data does indicate manufacturers are treading towards greater levels of activity,’ notes Davidge.
Make UK reported in September that 46% of companies have achieved 75-100% operating level, and 54% now expect it will take less than 12 months to return to normal trading conditions. However, the prospects of local lockdowns and the challenges around implementing social distancing on the ground remain an impediment to reaching 100% capacity.
‘I think it’s fair to say that where there has continued to be demand for their products, manufacturing businesses have found a way to continue production, subject to supply chain issues,’ adds Summers. ‘Some have managed or been forced to innovate or design new products to meet supply shortfalls in the market. Sometimes this has been in completely different markets.’
Supporting the industry
In the UK, government policy has been imperative to sustaining manufacturing. ‘Restrictions on our social behaviours included everything from social distancing to complete isolation for the most vulnerable, reshaping the status quo of our daily lives,’ Davidge says. ‘However, it is the effectiveness of these measures on businesses that has generated tremendous debate in recent weeks as the impact of COVID-19 on producer activity is yet to be fully understood.’
Summers continues, ‘Our recent survey of manufacturing businesses showed that 90% had furloughed staff and almost 70% had received a Coronavirus Business Interruption Loan or a Bounce Back Loan. This shows that the manufacturing sector has relied heavily on the government’s support.’
Davidge adds, ‘After a shaky start, these schemes started to operate relatively well. However, significant numbers of companies are either waiting for loan applications to be processed or have yet to apply.
‘The amount disbursed is still relatively low when compared to elsewhere in Europe and the USA. And there is only a certain amount of additional debt that businesses are willing to take on, particularly if it is used to finance unproductive activity. That’s why the Job Retention Scheme has been so critical.’
Supporting staff retention and maintaining national employment, furlough – whereby workers placed on leave were able to receive 80% of their pay under the Coronavirus Jobs Retention Scheme – has been a critical government measure for businesses.
As the scheme is set to wind down, 62% of companies believes it should be extended for critical sub-sectors, according to the September Make UK Monitor. In addition, 31% of manufacturers currently have no staff furloughed – the highest share since the survey’s inception. While 28.8% of manufacturers continue to furlough between 1-10% of their staff, 19.9% have furloughed 11-25%, 15.9% have furloughed 26-50%, and 4.4% have furloughed 51-75% of staff. No manufacturer surveyed currently has more than 75% of staff furloughed.
Summers emphasises, however, that even with the support of furlough and other schemes, if the demand for a company’s goods have fallen and alternative products or markets are not available to them, then inevitably they won’t need as many staff.
He says, ‘There’s a delicate balancing act to be done here, particularly for skilled workers. Companies do not want to lose all their skilled workers and not be able to respond to upturns in demand in the future. Some, rather than losing staff are asking staff to accept reduced hours to save all jobs, on the understanding that the position is continually monitored in the hope that all can return to their full hours at some point in the future.
‘That will be what happens in many of these situations. In others, however, staff cuts will be made as reduced hours are not sustainable for many households and so staff will look for full-time employment elsewhere if it can’t be provided by their current employers. Staff understand the current plight of companies and are being very understanding, but their goodwill and patience is not everlasting.’
Make UK also reported in September that 42% of firms have already made redundancies, and many firms will continue plans to make workers redundant. The share of manufacturers who are planning to make redundancies in the next six months has fallen from 53.3% to 30.2%. The Make UK Monitor in July included a company survey on training and apprenticeships. Promisingly, almost half of respondents, 44.5%, have continued with their apprenticeship plans, yet almost three in ten, 28.8%, have put some or all of their apprenticeship training on hold, as firms furlough apprentices or are unable to pay wages.
Wider training has taken a larger hit with almost half, 46.7%, putting some of their training on hold and one in five, 18.5%, pausing all training plans. Davidge notes that industry – alongside Make UK – will continue discussions with government over the situation and how several schemes are performing in mitigating some of the impacts of the virus on the manufacturing sector. Policy recommendations being put forward include a reduction in business rates, incentives to invest in automation, artificial intelligence and other digital technologies, as well as increased support for export activities.
To support employees facing redundancies, Make UK is also re-iterating calls for a National Skills Taskforce, and boosting the existing National Retraining Scheme so it is accessible to anyone, at any skill level or age. The trade body is also calling on government to future proof the skills of the next generation by offering direct payment incentive to employers and increasing the current Apprenticeship Incentive Funding for Employers.
‘It is essential that government recognises that manufacturing cannot simply switch on the engine and return to the output levels it was at a few months ago,’ Davidge warns. ‘As the pandemic continues to take its toll on our sector, we are continuing to call on government for decisive, bold action to support our sector in the days, weeks and months ahead.’
Pressing forward with innovation
The pandemic is forcing manufacturers to innovate, an approach that Summers encourages while urging the government to ramp up its related financial incentive schemes. ‘[Innovation] helps growth and develops new markets and the government has been good at encouraging that behaviour through the R&D tax credits and through generous tax treatment for new plant and machinery in the form of Annual Investment Allowances. I would like to see these enhanced further.’
As the sector returns to production, some companies are still in the stages of crisis management to offset the effects of the virus, and others are transitioning to future planning.
‘Some firms will inevitably struggle, some may have gone out of business already, while others may relocate, causing further supply chain disruptions that will take time to resolve,’ asserts Davidge. ‘In addition, many companies have eaten into their cash reserves to survive the crisis. It is highly likely that as the wider economy restarts, manufacturing will struggle to return to previous levels of output smoothly or quickly. It is inevitable that social distancing and related safety procedures within production facilities will impact upon the wider performance of the sector, particularly output levels.’