Acoustic levitation assembles micromechanical parts
Acoustic levitation may lift and assemble complex micromechanical structures without physical contact.
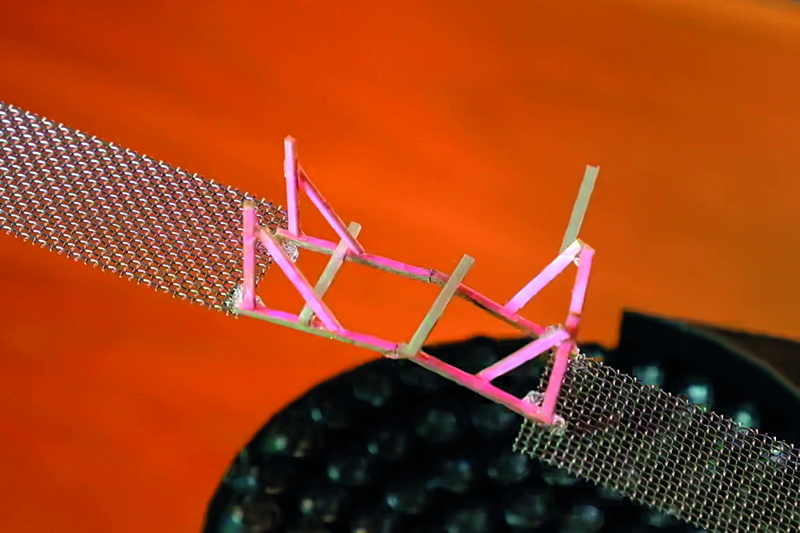
The LeviPrint system, developed at University of Navarre, Spain, combines a robotic arm and liquid dispenser to levitate and control the position and orientation of the components.
Ultraviolet (UV)-curable glue can be dispensed in liquid form, levitated into its target and cured remotely with UV light for assembly.
'It enables manufacturing techniques that cannot be achieved using traditional 3D printing, such as adding elements on top of existing parts or manufacturing inside closed containers from the outside,' Iñigo Ezcurdia, PhD student and lead author of the research. The ultrasonic field can pass through fabrics, meshes and other materials.
The team explains that levitation of small particles and droplets has been achieved before, but existing work has not trapped elongated objects in position and orientation. This research uses segments, sticks or beams for “fast and contactless manufacturing of robust, lightweight and complex structures'.
The materials they have tested so far are plastic spheres, droplets of glue and wooden sticks.
Asier Marzo, Lead Researcher, says, 'Acoustic levitation creates sound fields that trap particles in mid-air.
'When sound is emitted from multiple emitters (speakers), the sound field has wavy patterns of high and low amplitude (sound volume) and the particles tend to be trapped in the
low-amplitude regions.
'Two opposed emitters will create a standing wave, which is the traditional way to trap particles or droplets, yet it does trap an elongated stick. We engineered what the speakers emit to create acoustic fields with the correct shape to trap a stick and discovered that a field that has two low-amplitude regions at both sides of the stick works best.
'We can manipulate small, brittle parts, as well as liquids
or powders, thus making the processes more versatile.'
Marzo explains that this system will allow for less cross-contamination, manipulation of beads, liquids, sticks and powders with the same “end-effector” and the capability to move these building parts through holes in the piece.
He says, 'We usually use plastic and Styrofoam small spheres as the simplest objects to levitate.
'Liquids are more complicated to levitate since the levitation force needs to be adjusted – too much and the droplet will get squeezed and burst, too little and it will drop.
'The sticks were unstable with traditional standing waves, but were fully trapped with the new acoustic fields.'
With these materials the researchers simulated the forces and torques on sticks, and later assembled basic structures like butt and mitted joints, before moving on to more complex structures such as cubes or bridges.
'As an example, we [also] built a tiny boat inside a bottle made of metallic mesh by introducing the parts through a small hole at its side,' Marzo shares.
Two potential applications in the short- and mid-term are millimetric components in a watch and the optical parts in mobile phone cameras.
'The technique can be applied for building structures made of hundreds of pieces in a computer-controlled system,' Marzo continues. And could one day be adapted to work in water-based media for biomedical applications such as assembling cells or scaffolds.
'Our device was a prototype, just powerful enough to showcase the techniques and suggest future applications. Now, it is up to companies to build more powerful and accurate levitators that provide more accuracy and the possibility to work with aluminium or denser objects, if the technique makes sense for them.'