A spin on waste tyres into graphene for concrete
Scientists from Rice University, USA, are converting waste from rubber tyres into graphene to strengthen concrete in a more material efficient way.
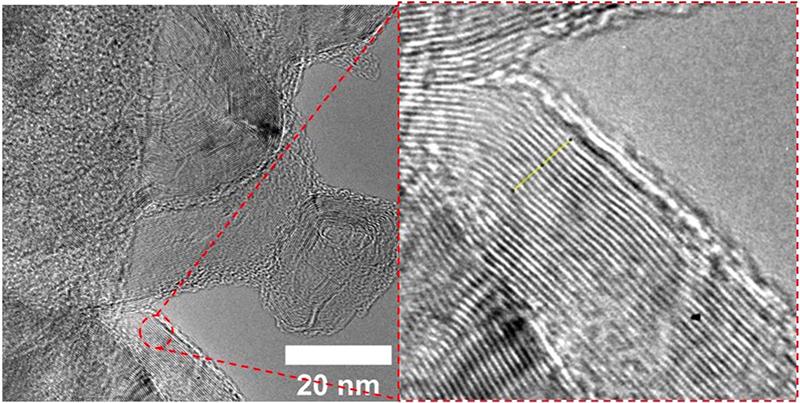
The process, known as flash Joule heating, produces a soluble, turbostratic graphene that can act as a reinforcing additive in concrete, allowing less cement to be used given the increase in strength.
Rubber tyres were chosen due to their high percentage of carbon atoms, which can be rearranged into graphene.
The flash Joule heating process – which refers to the heating when an electric current passes through a conductor – begins by placing the carbon feedstock between two graphite electrodes and compressing it.
‘This compression ensures closer contact between the individual particles, lowering the resistance of the sample. An electrical current is then passed between the electrodes from a bank of capacitors,’ says lead author Paul Advincula at Rice University.
‘In our system, this electrical current raises the temperature of the sample to >3,000K (2,727°C) in <0.5s. At this temperature, the bonds between the atoms in the feedstock break down and the carbon atoms can rearrange into graphene.
‘The rapid cooling of the system then locks the atoms into turbostratic graphene, rather than the AB-stacked graphene that results from other processes. Non-carbon atoms are sublimed out of the sample during this process, leaving a product with extremely high carbon content,’ shares Advincula.
Turbostratic is a characteristic that refers to the way graphene sheets are stacked which is said to make it easier to apply in composite materials.
‘Conventional graphene is AB- or Bernal-stacked…[which means sheets are] stacked nicely on top of each other and, as a result, are difficult to exfoliate. Turbostratic graphene sheets are actually rotated or twisted with regards to the sheets around them, making them much easier to exfoliate.’
Seventy per cent of tyre-derived carbon black converts to graphene, while flashing shredded rubber tyres mixed with plain carbon black to add conductivity transforms at a rate of 47%. The resulting tyre-derived graphene has been tested by adding it to cement and concrete to see if these materials could take advantage of its mechanical properties.
‘With the addition of 0.1wt% graphene, the compressive strength of cement paste and concrete increased by 30%,’ Advincula explains. ‘Production of cement accounts for 3% of total global energy use and 9% of human carbon dioxide emissions. Adding flash graphene to cement means that we can use less cement for the same application, reducing our CO₂ emissions overall.’
Further to that, he notes that the flash Joule heating process does not require any solvents or extensive chemical treatment.
‘The only components needed for this process are a feedstock, such as rubber, and electricity, which can be provided by renewable energy resources such as solar or wind energy. Removal of tyres from landfills and subsequent upcycling through flash Joule heating will have a significant effect on reducing waste and CO₂ emissions.’
To prepare the material, two different techniques are applied to the two forms of rubber used. Pyrolysed tyre-derived carbon black is thermally decomposed in an inert atmosphere, resulting in a fine, black powder suitable for flash Joule heating. Raw rubber tyres are, meanwhile, finely shredded into small particles (~1mm in size) and mixed with carbon black.
Carbon black is required because ‘on their own, shredded rubber tyres are not conductive enough to allow the electrical current to pass through the sample. Incorporating carbon black, which is extremely conductive, allows us to lower the resistance of the rubber tyres enough to pass electrical current through’, describes Advincula.
On scaling up, he says, ‘The process was originally carried out on a 50mg/batch scale, but our most recent systems are able to do up to 10g/batch.’
Universal Matter Advanced Materials, Canada, is now scaling up the process and expects to reach 1kg/day soon.