Wheels of progress - extracting value from paper milling wastewater
Consortium partners from the EU INGREEN project discussed the development of new chemical building blocks, plastic materials and consumer packaging from paper milling wastewater at a recent webinar. Alex Brinded reports.
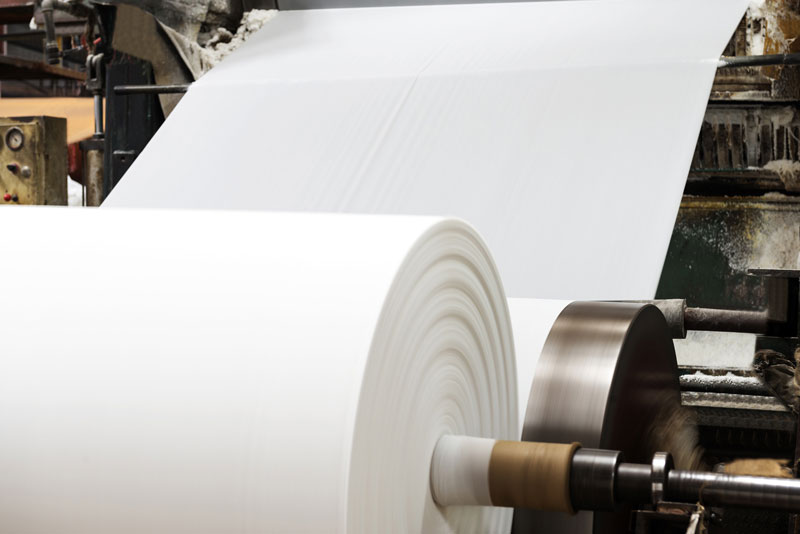
The EU INGREEN project aims to tackle the environmental impact of paper and agri-food industry by-products, by developing new chemicals, materials, and consumer products from whey, wheat and rye brans, and paper milling wastewater.
The project outlines that ‘the environmental impact of the pulp and paper industry is of particular concern since the industry emits a variety of gaseous, liquid and solid wastes to the surroundings. Although efficient wastewater treatment systems combined with biogas production are available in the paper industry, the environmental impact of organic fraction is still significant.
‘This is because approximately five litres of water are being released into rivers per kilogramme of recycled cardboard. In addition, little is known on the efficiency of the current systems to eliminate the toxicity attributed to the presence of organic compounds. Nevertheless, an interesting opportunity can emerge from these wastes if they can be converted into value-added by-products’.
INGREEN points to paper mill side-streams as a source of suitable carbon that could be upgraded to polyhydroxyalkanoates (PHAs), but with ‘more economical and environmentally friendly downstream processes to achieve this’. By using bacteria for extraction, the project aims to reduce toxic solvent use and produce high purity PHAs.
In turn, INGREEN is developing pilot-scale integrated biotechnological plants and protocols to produce safe biomasses enriched in PHA from the paper mill as an alternative to conventional plastic for the packaging industry. As there is limited knowledge on the application of PHAs as a polymer for packaging, INGREEN says it will provide a sustainable exploitation route.
An alternative plastic?
Dr Helena McMahon from Munster Technological University, Ireland, is Principal Investigator on the project and hosted a webinar for consortium partners to showcase their work.
PHAs are bio-based polymers, and defined by ScienceDirect as, ‘…a family of polyhydroxyesters of 3-, 4-, 5- and 6-hydroxyalkanoic acids, which are produced by a variety of bacterial species under nutrient-limiting conditions with excess carbon and are found as discrete cytoplasmic inclusions in bacterial cells’.
Jesùs R Gamero, from biotechnology developer Innoven, Italy, asked if PHAs could substitute for synthetic plastics. ‘It’s difficult to imagine our life without plastic synthetics because they are present almost everywhere, because the plastic synthetics have very spectacular properties. For example, elasticity or resistance, a low coefficient of friction and other benefits.
‘Generally, PHAs are…made 100% of biological origin, synthesised by microorganisms inside the cell when they are under stress condition. We can find more than 111 microorganisms [that are] PHA producers, they are microorganisms with the capacity of accumulating 90% of its weight in PHA and the PHA-producing bacteria have been found in all environmental conditions.
‘They are biodegradable and compostable. The PHAs can be hard to stress crack and [are] elastic, heat resistant, transparent and permeable to oxygen, ultra-violet stable, and they can have mechanical, physical, chemical and electrical properties like polypropylene for example.’
He continued, ‘In my opinion, the most important property of PHAs is biocompatibility. We can find more than 150 different monomers, but the three most important at the industrial level are 3- or 4-hydroxybutyrate, and 3-hydroxyvalerate – if we combine these three monomers, we can obtain a polymer with excellent properties…depending on the concentration of monomers in the polymer.
‘Unfortunately, the costs of PHA are very high – approximately 50 times higher than synthetics plastic. And these costs are limiting its introduction in the market.’
Reclaiming biomass from industrial waste
Paper manufacturer and INGREEN partner Smurfit Kappa, Italy, has developed a pilot plant in Tuscany that produces PHA-enriched biomass from their side-stream waste.
Luca Santarlasci, INGREEN Project Co-ordinator at Smurfit Kappa, said, ‘The paper mill waste usually contains suspended solids like fibres and cellulose materials in organic compounds, mainly represented by the calcium carbonate and many organic compounds that can be referenced as the COD, or the chemical oxygen demand of the waste stream.
‘In the case of Smurfit Kappa, Italy, about 40% of the overall COD consists of volatile fatty acids, which represent a useful substrate for PHA production using mixed microbial cultural techniques.’
Santarlasci explained further how the PHA-rich biomass is created. ‘The selection of the PHA-producing bacteria can be obtained by the so-called feast-famine cycles. During the feast phase, the feed is provided, and all the microbial species start to consume the volatile fatty acids in the paper-mill wastewater for cell growth and reproduction.’
The famine phase begins when the fatty acids are all consumed and ends when normal feed is provided to the microorganisms. In the famine stage, only species that synthesise intracellular PHA as feed reserve survive, while most unwanted species die. The PHA-enriched biomass is then degraded in a centrifuge to yield a solid of about 20wt.%. This is kept at 60°C for a few days to remove the 80wt.% of water and is then ground into a fine powder.
Nídia Lourenço, Senior Researcher in the Biochemical Engineering Group at the New University of Lisbon (NOVAID), Portugal, noted how the PHA is extracted/purified from mixed microbial cultures using an ‘eco-friendly’ approach. ‘Apart from a few exceptions...the PHA has to be extracted from the cells and can be up to 50% of the total production costs.
‘One [approach] is to solubilise the PHA granules and the other one is to dissolve everything that is not PHA.
‘The traditional approach involves organic solvent extraction to solubilise PHA granules and then we need a non-solvent precipitation step to recover the PHA. This traditional approach normally involves the use of chlorinated solvents like chloroform, and they have high recovery yields, high product purity in the end, but most of these approaches are not eco-friendly. And most of them are not scalable or are very difficult to scale up.
‘Our approach is based on chemical digestion to dissolve everything that is not PHA and after that we will do a PHA verification step.’
The pulp and paper industry is currently considered the third largest consumer of water and the sixth largest polluter in the world after the oil, cement, leather, textile and steel industries.
Approximately 5L of water is being released into rivers for each kilogramme of recycled cardboard.
Source: Paper milling wastewater – INGREEN (ingreenproject.eu)
Packaging plastic
At the other end of the supply chain, Technopackaging in Zaragoza, Spain, is producing a PHA film for bag-in-box products that they claim is biodegradable.
Irene Serrano, R&D Engineer at Technopackaging, reported, ‘The challenge is to manufacture bio-based films in a circular economy approach for the food, feed, cosmetics and pharmaceutical sector.
‘How do we go from the purified PHA to bag-in-box products? We use an extrusion component machine to blend the PHA within the necessary additives and thermoplastic matrix, which will enhance the properties of the extracted PHA and make it suitable for the final application. Then, the blend is tested in a film-blown equipment to assess its good processability, and after the production of the films, they are validated through mechanical, thermal and chemical characterisation to finally assess the suitability of the new developed material for commercial use.’
Discussing scaling up, Lourenço said, ‘The biggest challenge is to be in a chain where you have a production process that is stable and consistent, so that you know the quality of the biomass that you need to process. And so that’s a challenge for the successful extraction.’
McMahon concluded the event by noting, ‘PHA is a huge family of different types of molecules and polymers. And bringing those together creates a huge variety of materials with different properties. But how you potentially address that at the end of life if you want to recycle and regenerate and reuse the PHA molecules might present some other technical challenges that need to be overcome. So maybe that’s another follow-on project from INGREEN.’
With the paper and pulp industry ranked as the third largest consumer of water globally and sixth largest industry polluter, there is plenty of supply resource for the INGREEN team to hone their product with.