Waste not, want not – turning waste food into new materials
Tackling food waste is one of the main challenges we face in the race to net-zero and a more robust circular economy. Andrea Gaini investigates how wasted produce is finding its way into the production and advancement of new materials.
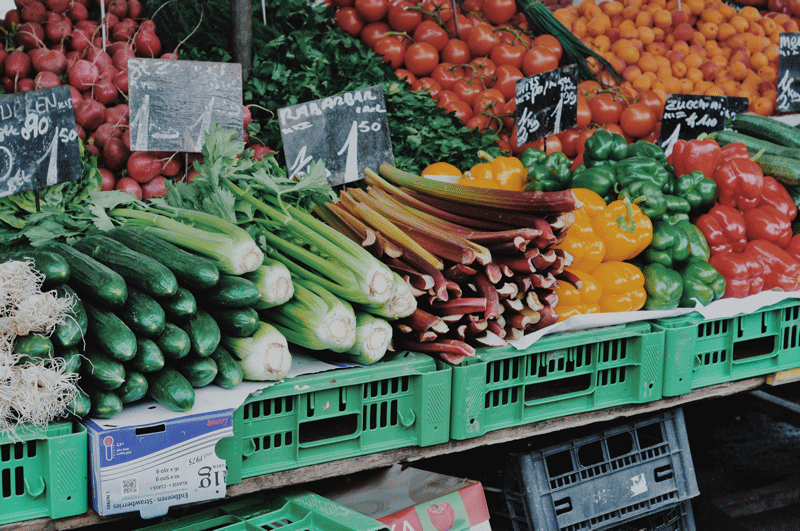
The UN Environment Programme (EP) Food Waste Index Report 2021 estimates that around 931Mt of food waste was generated in 2019 globally, 61% of which came from households, 26% from food service and 13% from retail.
'This suggests that 17% of total global food production may be wasted (11% in households, 5% in food service and 2% in retail),' reads the report, noting that 8-10% of global greenhouse gas emissions are associated with food that is not consumed.
The study examined the dangers of this burgeoning waste stream, and the multi-faceted benefits of reducing it at retail, food service and household level.
Here, we look at research projects that seek to produce novel materials from food waste.
From potatoes to plastics
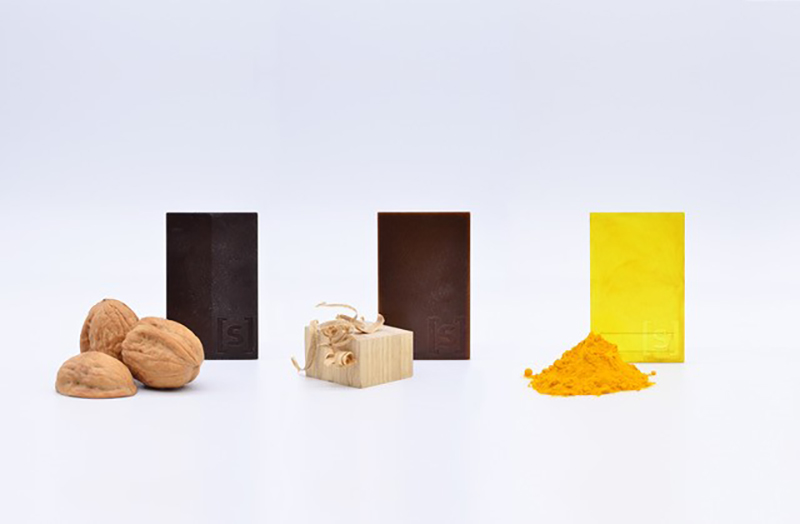
UK-based Chip[s] Board produces Parblex PLA – a thermoplastic and bioplastic that the inventors say can both be recycled and industrially composted at the end of its life.
Kingston School of Art design graduates Rowan Minkley and Rob Nicoll became 'fascinated both with the amount of materials wasted in the design industry and the amount of food wasted both commercially and domestically', Minkley explains.
'I was running multiple kitchens and began bringing home peelings and scraps and with Rob, began to experiment with making materials.'
Now the pair produce bioplastics using potato waste supplied by McCain UK.
Minkley continues, 'We recently relocated to Yorkshire to be closer to the UK’s main food processing centre and have access to a broad range of food waste supplied by Duynie. At the moment we are focused on vegetative food waste as our primary sources.'
To produce this material, they ferment food waste to create lactic acid, purify it and then polymerise it into Parblex PLA.
'Food waste is full of valuable nutrients and building blocks for our bacteria to convert into lactic acid and other valuable chemicals.
'Using second generation biomass (food waste) has a significantly lower environmental impact than first generation biomass (virgin food crops) and doesn’t compete with land for food production. We are completely focused on circular economy principals and low impact manufacturing.'
Minkley suggests that there are several benefits to using their materials, such as significantly lowering CO2e compared to bioplastics produced from virgin crops and petrochemical plastics, having multiple options for disposal at end of life, and 'also, like-for-like replacement with a number of petrochemical plastics, ease of use for polymer processing companies, [and] multiple uses after recycling as a thermoplastic'.
Minkley explains that Parblex can be injection moulded, 3D printed, spun into fibres and formed into sheets that adhere to standards.
'There are a whole range of ISO and BS EN tests we can complete looking at the materials properties. These include tensile strength, three-point bend, glass transition, ultra-violet degradation, compostability and more. We are currently working on completing a full material data sheet for our customers,' he adds.
'Initial results show a like-for-like performance against PLA made from virgin resources and strong performance against petrochemical plastics. We are still in the midst of this testing cycle.'
Regarding the future, Minkley says that scaling bioplastics is the only way to make them price competitive with petrochemicals and is one of the biggest limitations with the market.
'Currently bioplastics are less than 2% of the total plastic market in volume. The UK has potential to produce hundreds of thousands of tonnes of bioplastics from available food waste sources.'
'We are currently launching our pilot plant in Leeds, UK…Once this has become established, we will focus on funding and constructing a demo plant with significantly increased capacity and automation for higher volume production.'
Wasted food into construction materials
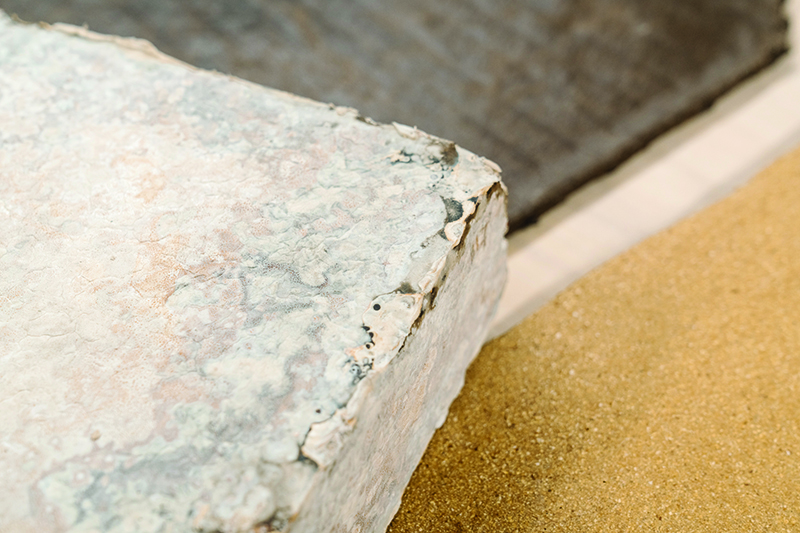
Biohm, UK, was founded by Ehab Sayed – a designer, engineer, researcher and entrepreneur – to bring the principles of biomimetics into the construction industry. He seeks to adapt and apply the ingenuity that is found in nature to the built environment.
The idea to use food waste came after the design of an intricate, nature-inspired construction system – triagomy – that does not require permanent binders or fasteners to create robust high-quality buildings. This allows buildings to be deconstructed and reconstructed at any stage of their life – eliminating demolition and making extensions, downsizing, relocation, recycling and reuse a much easier process.
Biohm explains that for such a system, healthy and regenerative materials are ideal.
The company uses mycelium for insulation panels and acoustic panels, and an organic refuse biocompound (Orb) to make construction board as well as lampshades and tiles.
For Orb, they have previously used orange peel, coffee chaff and sugar cane, among other food waste streams. For mycelium they tend to use agricultural waste streams, such as hemp stalks.
Orb, the firm says, can be formed into standard sheets for use as dry lining, or moulded or compressed into a diverse range of forms. It is moisture resilient – maintaining form, performance and breathability when exposed to moisture within the build.
The benefit of using unused produce is that organic waste contains interesting lignocellulosic compounds which make it a good food source for mycelium and gives it interesting properties in Orb.
To produce the materials, the waste is processed so it is clean and the right size for incorporating into the materials – this can include milling and sorting.
Mycelium is produced by letting the fungus grow in and around the substrate forming a foam-like composite material. For Orb, the waste is mixed with a plant-based binder and can be pressed into sheets or shaped into 3D forms.
The materials have undergone a variety of tests including tensile strength, compressive strength, thermal conductivity and acoustic properties.
Initial testing indicates that mycelium insulation has good thermal conductivity with an indicative range of 0.03-0.06W/mK.
Dressed up in pineapple leaves
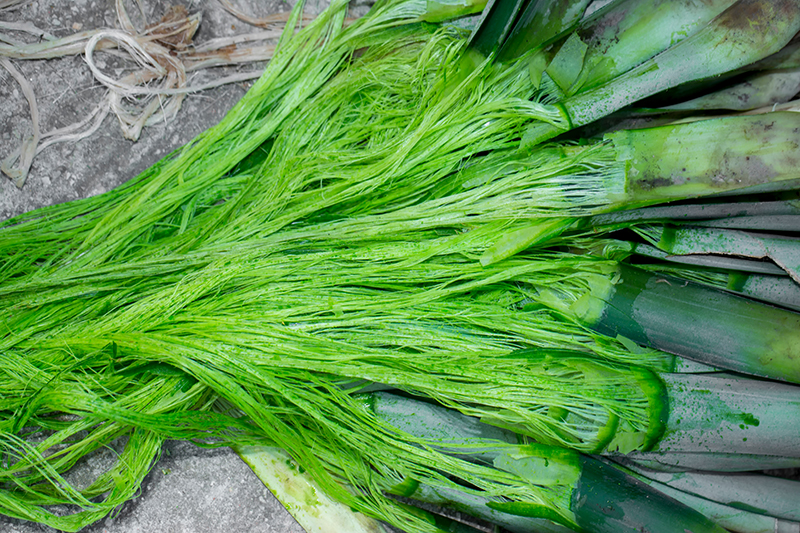
Ananas Anam in Spain creates Piñatex – a coated, non-woven textile from waste pineapple leaves for use in footwear, accessory and interiors markets. The firm suggests the textile is a suitable alternative to leather.
Inventor Dr Carmen Hijosa was inspired by piles of leftover pineapple leaves after a fruit harvest when she was in the Philippines.
Piñatex is made from 70% (± 2%) pineapple leaf fibre. After the fruit is harvested, the leaves are collected and the fibres extracted by semi-automated machines. They are then washed in water and dried naturally in the sun, or in cabins during the rainy season.
The dried fibres are purified before being blended with polylactic acid (PLA). This blend undergoes a mechanical needling process to create a non-woven mesh, which forms the base of all Piñatex collections. Pigments and a thin protective coating are applied to add colour, durability and other necessary properties.
Piñatex has been tested in a certified laboratory to validate its technical properties for use as textile, including REACH, and tear, tensile and abrasion tests.
The firm promotes the product as fully vegan and cruelty free, with no extra land, water or pesticides required to produce the raw material.
Eggshells and tomato peels gain wheels
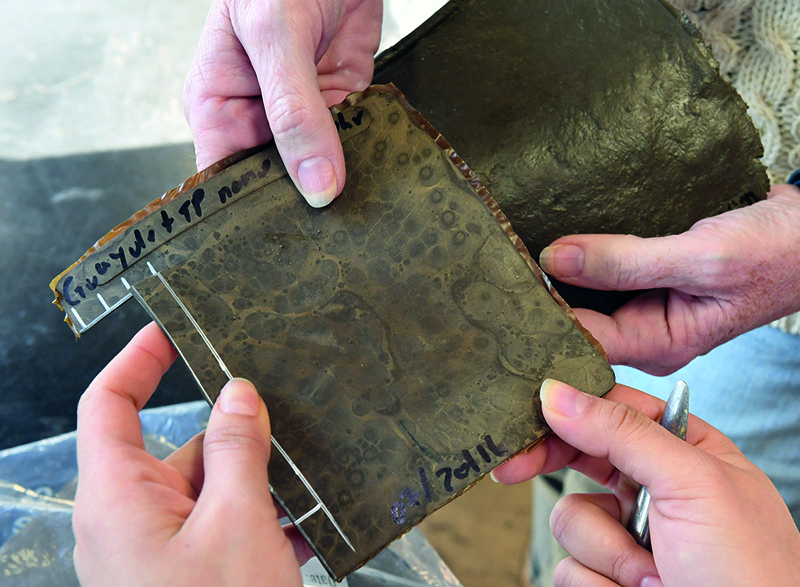
Food waste can partially replace the petroleum-based filler to manufacture tyres, according to research at Ohio State University, USA.
The scientists report that the resulting rubber exceeds industrial standards for performance, which may ultimately open up new applications.
Lead Researcher, Katrina Cornish, has spent years cultivating new domestic rubber sources and claims to have developed a method for turning eggshells and tomato peels into viable replacements for carbon black.
She explains, 'The chemical composition and hydrophobicity are very important because these determine whether or not a particular waste must be chemically modified before being added to a polymer, or if a compatibiliser is needed. In general, a new material has more affinity to itself than to the polymer into which it is being mixed so tends to aggregate – a good dispersion is required not agglomerated lumps.'
To prepare the wasted produce, eggshells are cleaned and ground to a powder, while tomato peels may come in the alkaline solution used to strip them from the fruit.
'They can be grown up in the liquid or dried first. The size of the grind matters but so does the expense of grinding. The smaller the particle size, the more expensive the waste-based filler is to prepare.'
Cornish describes how they tested the waste-derived fillers in latex and solid rubber products, varying the type of rubber used and the amount of filler incorporated.
'We then tested their strength, static and dynamic mechanical performance, ozone resistance, durability, hardness, and the amount of power needed to generate the homogenous rubber mixtures required for product manufacture.
'Tomato peels and eggshells gave better results than lignocellulosic fillers. We found that both fillers reduced the power required for mixing. Both were effective at partially replacing unsustainable carbon black or silica fillers when used as micro-size fillers, which are simple and relatively cheap to make.
'The eggshell microfiller also helped disperse the other filler in the rubber matrix. Nano eggshell gave good results when used to completely replace carbon black, but this is an expensive material to make.'
Banana peel and coffee grounds make graphene
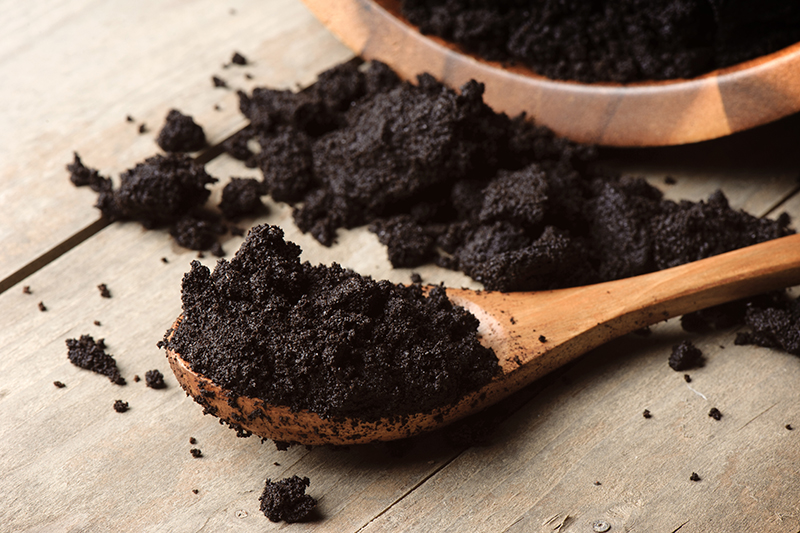
A novel process, developed at Rice University, USA, could produce graphene using banana peel, coffee grounds and other waste materials such as plastic.
The process, which the Lead Researcher James Tour calls the ‘flash graphene’ technique, is said to be quick and cheap and can convert “nearly anything with carbon content” into graphene for a fraction of the cost used by other bulk graphene-producing methods.
Tour says flash graphene is made by heating carbon-containing materials to more than 2,700oC. This flash joule heating is said to improve on exfoliation from graphite and chemical vapour deposition on a metal foil, which require much more effort and cost to produce graphene.
The process produces ‘turbostratic’ graphene, with misaligned layers that are easy to separate.
'A-B stacked graphene from other processes, like exfoliation of graphite, is very hard to pull apart,' Tour says. “The layers adhere strongly together. But turbostratic graphene is much easier to work with because the adhesion between layers is much lower. They just come apart in solution or upon blending in composites.
'That’s important, because now we can get each of these single-atomic layers to interact with a host composite,' he says.
The lab notes that used coffee grounds transform into “pristine single-layer sheets of graphene”.
Bulk composites of graphene with plastic, metals, plywood, concrete and other building materials could be a major market for flash graphene, according to the researchers, who are already testing graphene-enhanced concrete and plastic.
The flash process happens in a custom-designed reactor that heats material quickly and emits all non-carbon elements as gas. 'When this process is industrialised, elements like oxygen and nitrogen that exit the flash reactor can all be trapped as small molecules because they have value,' Tour says.
The flash process produces very little excess heat, channeling almost all of its energy into the target.