Ultra-thin composites for 5G communication
An ultra-thin composite film that absorbs more than 90% of electromagnetic (EM) waves could solve the problem of secondary interference in 5G communication frequencies over 26GHz.
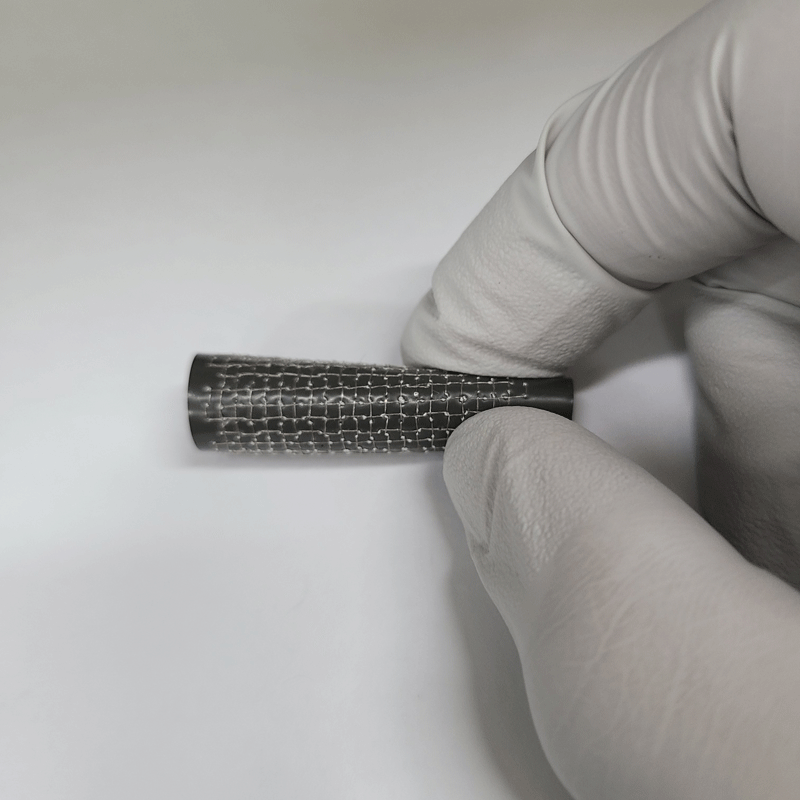
Researchers at the Korea Institute of Materials Science (KIMS) claim they have developed the world’s first ultra-thin composite film that can offset performance deterioration when an electronic component interferes with other electronic systems.
They explain that existing reflection-dominant shielding materials have an absorption rate of less than 10%. 5G communication uses frequency bands higher than 26GHz, which is 10 times more than the frequency of existing 3G/4G. As the secondary interference of EM noise is more severe with high frequency and short wavelength, there is demand for shielding materials with high absorbing capability.
‘This film consists of a magnetic lossy polymer-composite layer and a conductive grid,’ says Byeongjin Park, Senior Researcher at KIMS.
The metal-mesh optical filter has a conductive grid with a specific grid period that works as a bandpass filter – it passes only EM waves whose wavelength matches to the grid period (resonant frequency) and reflects the other EM wave components.
‘By placing a magnetic lossy composite layer on the conductive grid, the incident wave first attenuates in the lossy layer,’ Park says.
‘We found the relationship between the working frequency (resonant frequency, where the reflection is minimised) and the composite layer properties and grid geometries. By tailoring these parameters, especially grid geometries such as grid period and wire thickness, the working frequency of the film can be controlled.
‘Then, if the wave frequency does not match the resonant frequency, the conductive grid reflects a fraction of the incident waves. However, if the EM wave frequency is resonant, the incident waves are not reflected from the grid, and the shielding film absorbs the EM waves without any reflection.’
Park explains that the magnetic layer is produced by casting iron-mixed polyurethane solution into a thin film and, then once dried, conductive wires are stitched on the magnetic layer using an automatic sewing machine with a desired grid period.
The EM wave shielding effectiveness (SE), reflectance, absorbance and transmittance have been measured using a mmWave test facility at KIMS, which can test materials in the 0.5-110GHz frequency band.
‘The facility radiates 26GHz EM waves, and the radiated waves face the composite film. Then some of the waves reflect back, while the other is absorbed and transmitted through the film. By measuring the amount of reflected and transmitted waves, we can see how much this film reflects and absorbs (we can calculate the absorbance by subtracting the amount of reflected and transmitted waves from the amount of incident waves) the EM waves.’
At 400μm thickness, the film is reported to absorb 92.2% of the incident EM waves, while reflecting only 0.2% of them.
Park adds, ‘As this film is thin and polymer-based, [it] is quite flexible so that it maintains its shielding performance even after folded or wrinkled.’
The researchers believe the film will be easy to scale up as it is based on common polymer-based film casting processes.
Park concludes, ‘This process can be substituted by easier processes such as attaching printed/electroformed metal grids. We already succeeded to produce a composite layer film continuously of more than 100m, and we are preparing to test a pilot production of a 100m-long grid-attached-film this summer.’