Travelling light – fibre-reinforced polymer composites in zero-carbon emission flight
Professor Paul Hogg FIMMM and Dr Faye Smith FIMMM at Avalon Consultancy Services, UK, investigate the opportunities and challenges for fibre-reinforced polymer composites in zero-carbon emission flight.
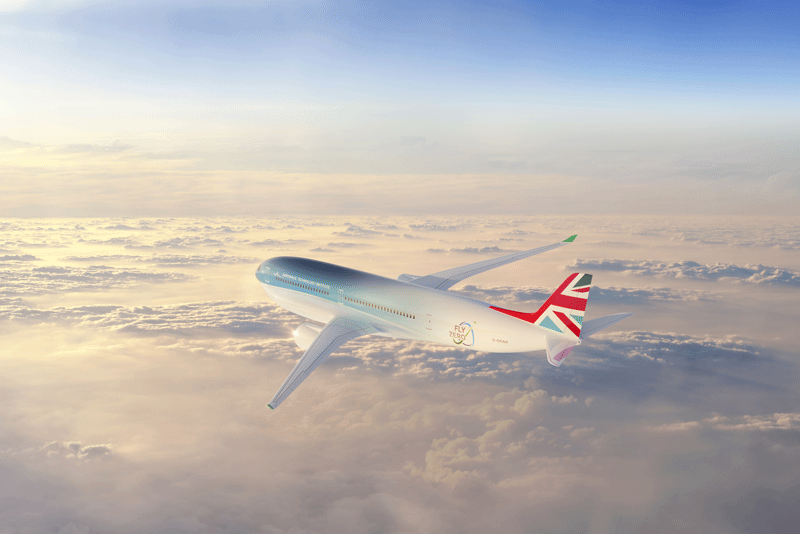
Led by the UK Aerospace Technology Institute and backed by the government, the FlyZero initiative began in early 2021 as an intensive research project investigating zero-carbon emission commercial flight.
The independent study has brought together experts from companies across the UK to study the design challenges, manufacturing demands, operational requirements and market opportunities of potential zero-carbon emission aircraft concepts.
The initiative has called upon expertise through work packages on specific questions related to realising zero-carbon emission commercial air travel. One of the studies commissioned by FlyZero was Novel Composites and Composite Aerostructures Technology, a position paper led by Avalon Consultancy Services, UK, with the support of membership body Composites UK. The paper focuses on fibre-reinforced polymer composites and excludes composites for use in cryogenic storage or interiors (covered in separate position papers). It considers composites in relation to the following criteria:
- Recent technology development and maturity – could they be ready for entry into service in 2030 or 2050?
- Technical benefits, economics, limitations and blockers.
- Supply chain availability.
- The potential applications in aerostructures – wing, fuselage, empennage, nacelle, etc.
- Cross-over to other areas of industry.
Push and pull
Much of the recent strategic work on composites has looked at the requirement of sectors, i.e. industry pull. This position paper differs from these in that it looks first at the composite technologies that are being developed and then considers how they might be used to facilitate the FlyZero goal, i.e. technology push.
Given that the ability of composites to replace metallic parts has often been limited by economics and design constraints, rather than just focusing on material properties, the paper includes developments in composite processing and structural design and manufacturing. It also considers the wider sustainability challenge linked to lower embedded carbon and a circular economy.
-
Improvements in properties.
-
Reductions in the cost of manufacture of parts.
- Contributions that composites can make to the development of novel structures.
- Sustainability.
Graphene potential
Composites with better mechanical properties could clearly result in lighter structures with direct weight savings. However, the primary contribution to composite mechanical properties comes from the fibres used, which for aerospace structures are almost exclusively carbon fibres. Recent carbon fibre research has focused on cost and environmental footprint rather than improved mechanical properties.
Where the mechanical properties of composites may be improved is in areas such as delamination resistance, damage tolerance and possibly fatigue, where additives such as nanomaterials could be deployed.
Graphene (and its derivatives) has the potential to be a relatively cheap material that could be added to composites, as coatings to fibres and additives to resin when problems linked to standardisation, health and safety, and manufacture at scale have all been dealt with.
Despite a wealth of ongoing research, it is unlikely that nano-enhanced composites will be qualified for a new commercial aircraft with an expected entry into service in the 2030-35 timeframe, although 2050 should be feasible.
It should be noted that increases in mechanical performance would need to be significant to be worth the inevitable additional costs associated with the manufacture and certification of the constituents. The use of nanomaterials could also provide indirect benefits to weight saving if they realised their potential of creating multifunctional composites to provide lightning strike protection and de-icing capability. It is unlikely that this will reach sufficient maturity by 2030.
Better bottom line
Historically, aerospace composite parts were manufactured using slow, energy-intensive processes requiring expensive capital equipment in the form of autoclaves and a host of ancillary processing consumables. This resulted in a high proportion of scrap and a struggle to meet demanding requirements for rate. The industry has been developing out-of-autoclave processing for many years and this survey has shown that such alternative process routes are either in use or close to becoming viable.
Probably the most favoured low-cost routes for thermosetting composites are variations on the infusion/resin transfer moulding (RTM) route, and manufacture of aerospace components has been successfully demonstrated using most major variants. There are still problems with achieving secure, reproducible low-void infusions in large and complex parts, but there are many solutions to this underway, including sequential or partitioned infusion, coupled with better modelling.
Wrinkling of fabrics to conform to complex curved surfaces is still a difficulty, but this can be remedied on a case-by-case basis, and modelling of fabric deformation has significantly improved.
The major difficulty would now seem to be to quantify the probability and severity of defects to facilitate certification. New, low-viscosity, two-part resins look to become a valuable addition for infusion once qualification can be overcome. Most infusion or RTM processes involve reduced scrap and, if 3D preforms are used, the process is near-net shape.
Thermoplastic composites, which involve thermal processing of individual layers in automated fibre placement (AFP) or automated tape laying (ATL), forming of reconsolidated sheet and welding of parts, potentially offer rapid processing along with lower energy costs, especially as new heating methods are commercialised.
Thermoplastic composites are used in limited quantities for structural parts such as leading edges and many small parts such as clips and brackets. Demonstrator projects in the EU are now underway, which could assist in the wider use of thermoplastic composites, the use of which could have some long-term benefits in terms of both recycling and repair.
Having previously been a leader in the development of new materials and manufacturing methods, generally it is now the case that aerospace is slow to introduce new processes and embrace new concepts for primary structures, in comparison to sectors such as automotive. However, with the right support, it is believed that higher rate, more environmentally friendly manufacturing methods could reach maturity by 2030.
Moving away from 'black metal' design
Design with composite materials has always presented greater difficulties than with nominally isotropic materials such as metals. Nevertheless, the industry has gained experience and confidence over the years via the gradual introduction of the materials into structural parts, and increasingly powerful analytical tools have been developed to assist the design engineer.
The integration of the various design processes and manufacturing operations under an engineering umbrella of modelling-based energy systems (MBES) looks likely to reduce overall costs and shorten development times. What is becoming clear, however, is that current design approaches, and the accepted structural layout of composite aircraft wings and fuselage, still largely conform to the concepts adopted for years in the design and manufacture of metallic aircraft, for example ‘black metal’ design.
Design principles, influenced by such protocols as MIL-BDBK-17 (Composite Materials Handbook, Volume 1 – Polymer Matrix Composites Guidelines for Characterization of Structural Materials and Certification Requirements), are constraining the use of novel design concepts. The move to alternative power sources offers the opportunity of a dry wing (one that does not contain liquid fuel) and the design freedom that results could allow an engineering team to adopt radical new concepts.
Biomimetic approaches using generative design methods could be one strategy to develop step-changes in weight reductions. Curved spars and structural elements mapping the major stress paths in a wing structure are now feasible from a manufacturing perspective. Tow steering/tow shearing and the use of non-standard ply orientations could all be explored, although improvements in deposition rate would need to be made.
This could possibly be supplemented by judicious local use of additive manufacturing and over-moulding by thermoplastics, the incorporation of structural power, and nano-based systems for lightning strike protection and de-icing integrated into the structure.
This could also trigger renewed interest in the development of new carbon fibres with bespoke properties tailored for local needs in a hybrid structure. However, to do so requires a willingness to adopt new ideas and concepts. It would require a considerable change – a paradigm shift in design practice.
The move away from ‘black metal’ design and considering the use of non-standard composite material lay-ups are probably as fundamental as the original move from metals to composites, but this would appear to represent the best way to make a significant leap forward.
Examining the footprint
Many advances in materials, material properties and processing that are likely to make a significant contribution to the FlyZero agenda, come in the area of sustainability.
While the sustainability of a material has no direct influence on whether an airframe that meets the FlyZero requirements can be developed, it would be perverse to promote materials technologies that might be overtaken and rendered irrelevant as environmental legislation increases and becomes more restrictive.
At present, the prime composite materials of interest to aerospace – carbon fibres and epoxy resins – are developed from oil feedstocks. Carbon fibres also require significant amount of energy to be produced from polyacrylonitrile precursors, resulting in a significant carbon footprint. If legislation emerges where the embedded carbon linked to a material constitutes part of the selection criteria, then it would be prudent to know what the embedded carbon is and find ways to reduce it. This is not something that is in place at present and may itself be a blocker for future composites development.
Work to reduce the embedded carbon of materials is underway and the field of biosourced resins is developing at a considerable rate. It is likely that industries such as the automotive sector will make use of such materials in the short term, but direct practical experience from other sectors could however be valuable.
Out-of-autoclave processing highlighted earlier as a route to reducing costs is also a route to reducing energy consumption, using less consumables and reducing scrap.
It is clear that recycling of carbon fibre composites is technically feasible via many emerging routes and potentially commercially viable, but only if there is a market for the products of the recycling process. It is probable that an aerospace recycling route will depend on markets for recycled fibres in other sectors, notably automotive and consumer products.
Qualification and certification
Through the investigation of new advances in composites, there was a consistent theme that, while many developments are exciting and promising, the major obstacle is likely to be qualifying a material and certifying a part.
Biosourced materials suffer from variability and therefore present a problem. New manufacturing processes may present difficulties in guaranteeing the extent and severity of manufacturing defects. Adhesive bonds are not suitable for certification for primary structures at present.
Most importantly, however, radical design approaches could require prohibitive levels of testing and validation if certification processes do not adapt. It could be that the only way forward is to reduce the testing burden by replacing the majority of coupon testing with virtual testing, augmented by a greater reliance on element or subcomponent testing.

At present, the new manufacturing processes and design capabilities available for composites could provide a route to cost-effectively delivering much lighter and more efficient aircraft, suitable for novel power systems and hence zero-carbon emission flight. At the same time, materials, processing and recycling developments could significantly reduce the embedded carbon content in a carbon part making them competitive with other materials from a sustainability perspective. The major blockers to this are:
- Black metal design concepts and reticence to use non-standard composite material lay-ups.
- Lack of understanding of the embedded carbon in composite materials and parts.
- Lack of cost-effective routes for radical composite designs to meet certification requirements.
Towards carbon-free flight
In September 2021, FlyZero identified green liquid hydrogen as the fuel of the future for commercial aircraft. It highlighted that hydrogen has three times the energy of kerosene per kg, 60 times the energy of batteries per kg, and emits no CO₂ when burnt.
FlyZero’s midsize aircraft concept demonstrates a hydrogen-powered aircraft capable of carrying up to 279 passengers anywhere in the world. It could fly between London and San Francisco direct or between London and Auckland with just one stop.
Carbon-free flights will require a step-change in the design, development, manufacture and operation of commercial aircraft. With the right investment, FlyZero believes new technologies have the potential to usher in a new era for aviation, akin to the advent of the jet age, bringing with it opportunities for the UK aerospace industry to capitalise on this future market building on decades of expertise.
The programme aims to deliver three zero-carbon emission aircraft concepts, an assessment of the potential market and economic benefits for the UK, a sustainability assessment, technology roadmaps, an assessment of the UK’s industrial capability and future industrialisation requirements. These findings will directly support the UK aerospace sector and its supply chain in capitalising on the opportunities a new generation of aircraft will bring.
To discover more and download the FlyZero reports, visit www.ati.org.uk.
Hitting milestones
The economic viability of zero-carbon emission commercial aircraft is dependent on the development of lightweight, aerodynamically efficient airframes. While the blockers to the adoption of new composites technologies are significant, the industry needs to accept the challenge of overcoming them as quickly as possible if the desired entry into service dates are to be achieved.
The authors would like to thank the FlyZero team (in particular Kuheli Sahu, Stephen Phillips and James Minshull) for their support during the production of the Composite materials technology position paper.