Take off for all-composite helicopter wheels with new partnership
Carbon ThreeSixty and the National Composites Centre, UK, are collaborating to develop and manufacture an ultra-low mass, robust, proof-of-concept carbon fibre reinforced plastic (CFRP) wheel for rotary wing aircraft.
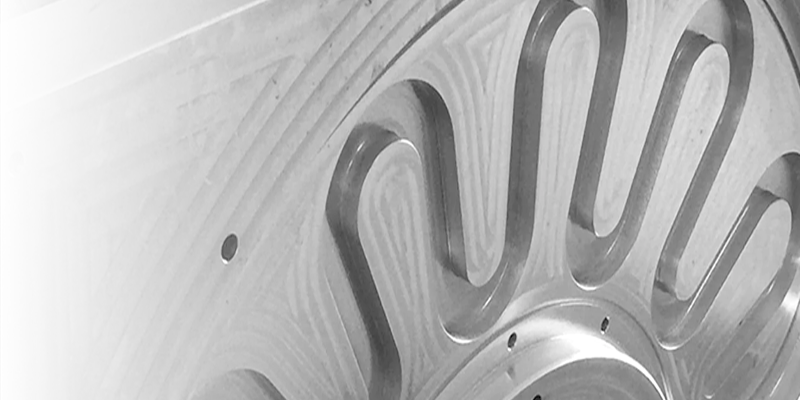
Joining forces with aircraft supplier, Leonardo, and co-funded by Innovate UK, the NATEP project aims to improve performance, safety & full ownership cost.
The current global market for helicopter wheels uses metallic light-alloy materials, usually aluminium or magnesium. These offer sufficient strength and stiffness from a relatively low density.
The team claims the wheel made of CFRP will offer significantly enhanced mechanical properties at approximately half the density of metallic wheels. Compared to aluminium alloys, a CFRP wheel will be lighter, with higher performance with an extended working life.
The project will use cutting edge composite manufacturing technology such as tailored fibre placement (TFP), braiding and out of autoclave processes to ensure repeatability and scalability while utilising novel product and process design to enable the partners to protect IP required to successfully manufacture the products.
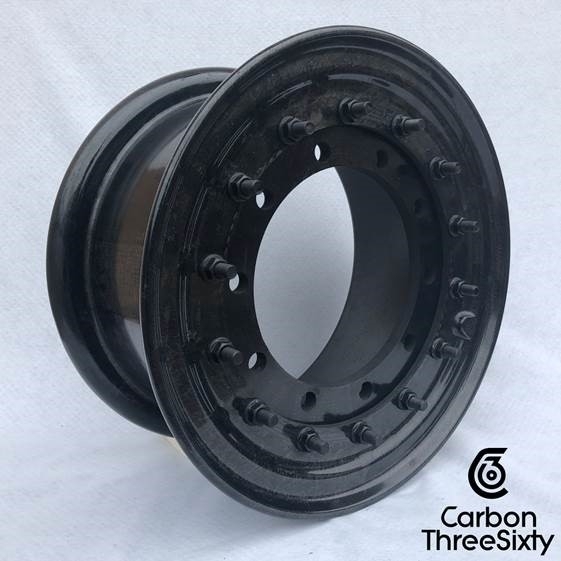
'Composite wheels have only become viable in the last 10 years due to improvements in resin system toughness, lower carbon fibre prices and improvements in process automation,' says Alex Doyle, Technology Project Lead of National Composites Centre. 'We can see this in the automotive wheel market, where they are now proven.
'However, aerospace applications are more challenging. The shift in cost, combined with the technical improvements are the reason why now is the time composite wheels are feasible for aerospace rotorcraft applications.'
Adrian Smith, R&T Portfolio Delivery at Leonardo Helicopters UK, adds, 'Composites are expected to save around 1.5kg over each 5kg alloy wheel. This 6kg weight saving overall represents almost 1,000 gallons of fuel saved over a typical 12,000 hour service life and equates to around 12 tonnes of CO2.'
The project is expected to last around 18 months, with a total budget of around £250k. Deliverables will include 12 fully tested proof of concept wheels, and a methodology for design and manufacture.