Taking biomaterial fabrication for a spin to develop nanomaterials
Transforming biomaterial fabrication with a less environmentally hazardous electrospinning process could enable scalable production of nanomaterials, researchers say.
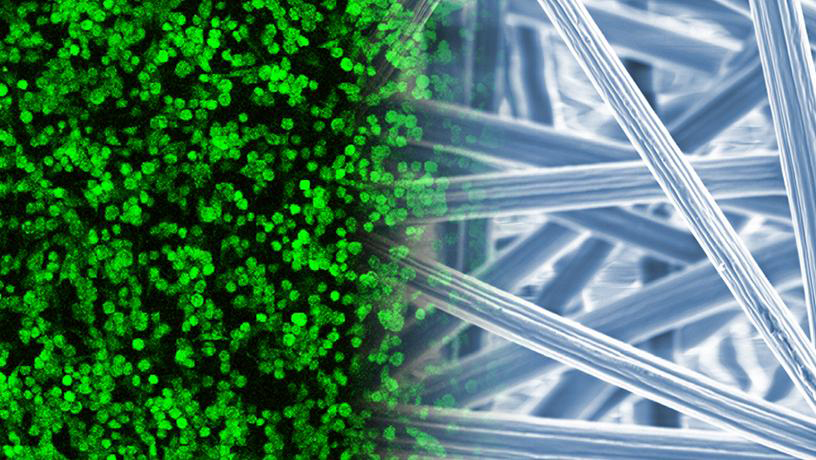
A team from Columbia University, USA, says their process provides a less harmful alternative that can be scaled, while traditional electrospinning uses hazardous or volatile chemicals that cannot be stored in large volumes for risk of explosion. This is posing a significant barrier to industrial scale-up and clinical translation.
By reducing the ecological impact of the process, the researchers claim they can ameliorate the fabrication of biomedical polymers, cutting the harmful manufacturing impacts of electrospinning by three to six times.
‘Electrospun fibres serve as temporary substrates for cells to regenerate tissues, and they biodegrade as new tissues form,’ says Christopher Mosher, Doctoral Student at the University.
‘Despite research success, the clinical translation of electrospun technologies is severely hindered by a myriad of challenges in scaling up for biomanufacturing, ranging from the environmental risks of volatile solvent storage and disposal at large volumes, to meeting health and safety standards during both fabrication and implementation.’
By systematically testing what the US Food and Drug Administration (FDA) considers biologically benign solvents (Q3C Class 3), the team has identified acetic acid as a solvent with low ecological impact – determined by Sustainable Minds Life Cycle Assessment – that supports a stable electrospinning jet under routine fabrication conditions.
‘We performed a lifecycle analysis to show that the solvents in question have minimal environmental impacts with regards to acidification, ecotoxicity, eutrophication, global warming, ozone depletion and fossil fuel depletion,’ Mosher notes.
‘We [also] systematically evaluated FDA Q3C solvents classified for pharmaceutical use to ensure the solvents explored are not damaging to human health.’
They have tuned the electrospinning parameters, such as needle-plate distance and flow rate. The team has used biomedical polymers, polymer blends, polymer-ceramic composites, and growth factor delivery systems. These are the most common materials used in both soft (cartilage, ligament, tendon) and hard (bone, calcified cartilage) tissue engineering applications. The electrospinning of biopolymer nanofibres and synthetic polymer microfibres act as matrices to support cell-based biofabrication.
Despite modernising traditional electrospinning, Mosher shares that they have preserved the composition, chemistry, architecture and biocompatibility of traditionally electrospun fibres, and improved their mechanical properties to closely mimic those of collagenous tissues, with double the ductility of traditional fibres without compromising yield or ultimate tensile strength.
Mosher concludes, ‘It is our hope that existing electrospinning technologies adopt our technique, and companies…utilise our technique to facilitate mass manufacturing and clinical adoption of electrospun biomaterials for tissue engineering applications.’
Also see Materials World, April 2020, for an article on well spun medical innovations at bit.ly/3DVxRlR.