Sustainability in mining
Mining engineer and consultant Laurence Morris FIMMM discusses the role and realities of sustainability in mining.
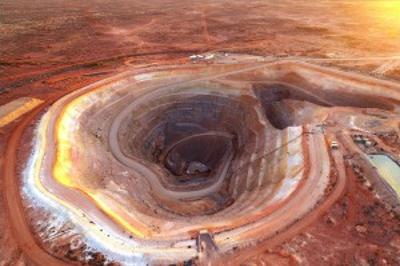
We are consuming irreplaceable resources too fast and destroying the natural environment, according to environmentalists. And replacement is difficult or impossible – replacing old growth forests and North Sea fishing stocks would take many decades, and minerals taken out of the ground cannot be replaced at all. Hence, the concept of sustainability or sustainable development has arisen, although sustainability has many meanings and frequently is synonymous with the term ‘environmentalism’ itself.
A good starting point is the United Nations-sponsored Brundtland Report of 1987 entitled Our Common Future. It is accepted by most environmentalists and defines sustainable development as, ‘development that meets the needs of the present without compromising the ability of future generations to meet their own needs’.
Brundtland does not explicitly discuss the replacement of resources, but assumes a ‘dinner plate’ analogy – that is, eating about half of the meat and veg on the plate, leaving the table hungry, but saving the rest for breakfast. In other words, society is gobbling up the whole plate now, leaving nothing for tomorrow, or for future generations.
Brundtland defines needs as prioritising the world’s poor rather than societies as a whole. But societies not only include post-industrial countries such as the UK and the USA, but also developing countries from Afghanistan to Zimbabwe, all of which need resources. Few people would disagree about the unacceptable levels of inequality across the globe, but the poorest levels of society benefit from economic growth, which includes rich countries as well as poor – and all the middling countries in between. Between 1981 and 2013, the number of people globally in absolute poverty fell by one billion, reported The Economist in an article in 2017, and the number who escaped poverty entirely rose by roughly four billion through economic growth.
Growth depends on the consumption of raw materials, especially ores and minerals. But in maintaining high levels of growth, the environmentalist’s concern is that we will eat the entire dinner plate leaving nothing for the future.
Complete sustainability would suggest we cut consumption of all raw materials – from tuna and teak to tungsten – and make do with none or negative economic growth, as demanded by Extinction Rebellion or as put forward by Prince Charles – a lower level of sustainable growth based solely on green technology. However, the problems with zero or low growth are at least three-fold:
- Green technology depends on mining metals like copper (2.5-6.4t of copper per megawatt of power, according to the Copper Development Association), rare earth elements such as lithium, and minerals such as limestone and aggregates, for example, for wind turbine foundations.
- Funding a redistribution of resources towards a green future will likely be costly, as the British government will likely discover on its quest to a carbon-neutral future by 2050. Reliable cost figures, however, are hard to obtain.
- The rest of the world from Brazil to Bangladesh will power on funding conventional economic growth, whatever the policies or opinions of Europeans, and eat up more of the Earth’s resources.
Defining sustainability in mining
Brundtland’s sustainability cannot apply to those non-renewable resources needed for growth and the alleviation of world poverty. Sustainability has therefore developed different meanings to overcome this, and sustainability applied to mining is no exception. A discussion of sustainability in mining by The Guardian newspaper back in 2015 quotes ‘stewardship’, good relations with local communities and stresses mitigating adverse socio-economic factors that can occur.
On the other hand, Transparency International of Canada, in its 2018 report on Mining for Sustainable Development, discusses combatting corruption as the first step in sustainability. Meanwhile, other authors consider, among other things, energy efficiency, climate change and water scarcity. In other words, mining sustainability means different things to different authorities.
There is one exception to the conundrum of irreplaceable ore resources. An ore reserve is a resource that is proven to be economic to extract. Mining companies spend fortunes converting resources into reserves, from exploration to the choice of mining equipment, and is part of the reason why some invest in innovative technology. Subsequently, mining technology has changed out of recognition over the last 100 years, enabling progressively less richer resources to be mined profitably. Economic gold ore grades have fallen from 4.0 to less than 0.4g/t in the past 30 years, allowing large low-grade deposits to become economic. There is no reason to believe that technology will falter now, and, in future, economic grades may become low enough to allow undersea mining.
The likely prospect is that provided technology continues to reveal mineable low-grade deposits, some resources will become available for future generations and the Brundtland definition of sustainability is met, even allowing for continued economic growth in the present.Otherwise, there are many definitions of mining sustainability in use. In this article, the focus is the technical aspects that are within the control of mining operations, such as energy usage, equipment efficiency, water scarcity and rehabilitation.
For many, sustainability is seen as a sub-set of environmentalism, which is dominated by climate change. Miners as good world citizens are obligated to reduce atmospheric emissions and all that is possible to alleviate climate change.
Powering through
A problem faced by many mines is obtaining enough power. Requirements can vary enormously from a few to several hundred megawatts. Getting power from a country’s national grid can be difficult through grid capacity, remoteness, terrain, and environmental and social permitting. It is also extremely expensive. Instead of feeding from the national grid, many mines instead rely on diesel generators, or, in the case of Quantum Minerals’ Cobre Panama, build its own 300MW coal-fired power station.
Some mines are looking at renewable power, such as B2Gold’s 7MW solar power plant at Otjikoto in Namibia. The Diavik diamond mine in Canada’s North-West Territories has installed a wind farm producing 9.2MW. However, these are somewhat isolated examples and perhaps more needs to be done to encourage renewable energy.
Solar costs have dropped by 80% over the past decade, reported The Harvard Review in its article, Why mining – yes mining – cares about sustainability in April 2018. And the cost of battery storage is making electric vehicles more competitive. Given the environmental and permitting pressures on building long-distance powerlines, it can be expected that the mining industry will eventually consider solar and wind farms as part-solutions for its power-hungry requirements.
Mine trucks
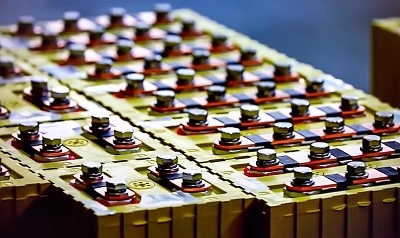
All the major countries have strict vehicle emission standards and it would be suicidal for an original equipment manufacturer (OEMs) not to meet those standards. The principal OEMs, such as Caterpillar, Komatsu, Leibherr, Atlas Copco, Tamrock and JCB, are all cognizant that most major mining regulatory authorities now insist on measuring and reporting emission standards. Meeting those standards assumes the equipment is kept in good condition by efficient and OEM-supported preventative and predictive maintenance programmes.
There is a tendency to move towards hybrid diesel and electric fleets. Trolley assist is being employed in several First Quantum mines for uphill haulages, which saves on diesel and considerably increases uphill speed. The company’s Cobre Panama operation is using the Liebherr T284 hybrid ultra-truck.
The next upgrade from trolley assist is to use the all-electric truck. Caterpillar has introduced the 795 AF ultra-haul truck that carries a payload of just over 312t. While the electric mine fleet effectively produces zero emissions, it cannot be widespread until mines solve the electric supply issues, and, in my experience, hybrid and electric trucks are not tolerant of poor road construction. Haul roads have to have few irregularities – or the truck loses power from the overhead pantechnicon – and preferably be sealed.
Another energy-saving means is to reduce truck haul distances by using conveyors and in-pit crushers, or placing the crusher at the top of the main pit ramp. Overland conveyors then transport the crushed ore to the plant. Cobre Panama has four large in-pit crushers matched to the ultra-trucks, and the Ixtaca project in Mexico will have the crusher located by the pit entrance.
Water scarcity
Water is a scarce resource in many mines, and, in some countries, there are prohibitive regulations on abstracting from rivers or pumping groundwater. The Esperanza mine in Chile is constructing a seashore desalination plant and intends to pump the water 145km to the mine site. The Ixtaca silver and gold project plans on using a complex system of surface water collection for the plant and also supply the local communities with fresh water.
Rehabilitation plans
Most mining regulatory authorities insist on a mine closure plan, including a full scheme of rehabilitation that should leave the terrain in an equal or better state than the mine found it. Most legislatures also require payment of a bond to cover the rehabilitation costs. To quote the Minerals Council of Australia, ‘The industry’s approach to land rehabilitation has improved significantly over past decades. We work to improve rehabilitation methods to ensure mining’s compatibility with current and future land uses such as farming. Mining companies understand land rehabilitation is fundamental to responsible mining. It is a critical factor for ongoing community acceptance and a key indicator for corporate reporting’.
However, the somewhat rosy picture can be compromised by tailings ponds. Tailings are the waste products from mining, consisting of finely ground rock particles, chemicals, minerals and water, often in a slurry or solid form. The chemicals include toxic elements such as cyanide and arsenic.
Tailings dams can be huge – every tonne of ore sent to the process plant produces essentially one tonne of waste. Dams can be created by the ‘upstream’ method which uses the tailings themselves to form a barrier. Several upstream dams have failed, sometimes spectacularly, such as Brumadinho, Brazil, in January 2019.
The rehabilitation of tailings dams can be difficult given their physical instability and chemistry. As described by the Government of Victoria, Australia, the dam should be fully dried out to allow machinery on its surface. The walls are stabilised by battering down to a lower angle, and cut-off drains are installed to prevent flows onto the surface. Tailings that are excessively acid or have high levels of heavy metals have to be capped and further treated by lime and other chemicals. Dams then have to be maintained in perpetuity. Doubts on this have led to the development of filtered (solid) tailings and cyanide alternatives.
Copper demand
The Harvard Business Review points out that copper production is likely to increase owing to its role in green technology. Copper is an essential element of electric vehicles, batteries, solar panels and wind turbines. According to the Copper Development Association, in the wind turbines Vestas Model V47 and Vestas Model V80, rated at 660kW, the motor windings contain around 800lb (363kg) of copper. According to the US Government’s National Renewable Energy Laboratory (May 2017), for every megawatt of wind power, between 0.7 and 1.8t of copper are needed, depending on the model – and 110t of steel on average. Turbines also comprise 13% by total turbine mass of fibreglass, resin and/or plastic, states the same source.
Against the forecast of rising demand for copper, the grade of copper is down from 4% some 200 years ago to under 1% now, and it is still falling. The Harvard Business Review believes that the copper industry is going to hit a crunch point unless the industry itself uses new technology to mine lower grades.
Finite resources
Mining has some way to go to achieve sustainability, but part of the problem is the loose meaning of the term. Ore bodies are finite resources and although technology allows economic extraction of lower grades, they are not renewable resources in the way a forest or a lake is. Hence, achieving sustainability is really about being good environmental stewards in protecting flora and fauna, conserving energy and water, improving local communities and a whole plethora of activities. Several practical ways mines are achieving sustainability is the management of emissions, pollution, energy usage, equipment efficiency, water scarcity and rehabilitation. And, in fact, many mines spend prodigious amounts of money on environmental and socio-economic protection, which is increasingly required as part of the operational permits by governments worldwide.
However, perhaps one unexpected consequence, is the need to at least continue the extraction of copper and other metals – and rare earths – and to increase production. Green technology is a heavy user of several metals, especially copper, and rare earths. Without some tolerance of mining, vaunted decarbonisation of the economy is a hopeless dream.