Stretchy film for wearable batteries
A stretchable packaging film for batteries that has a high moisture and gas barrier could help realise wearable devices with highly deformable batteries.
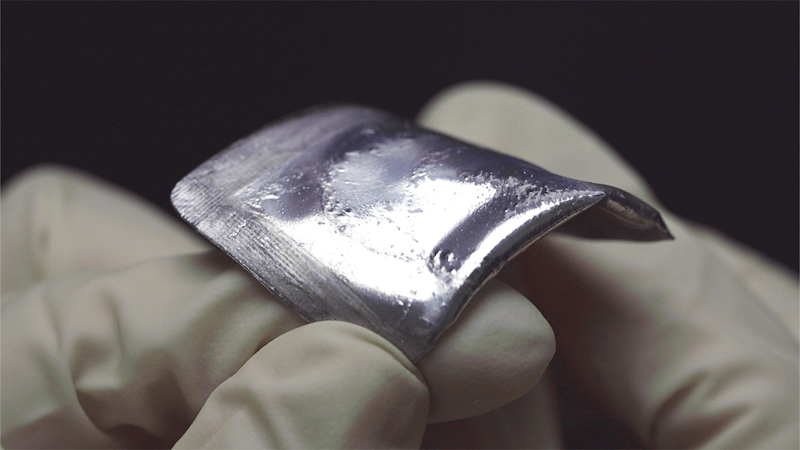
Researchers at Yokohama National University, Japan, have designed the film by coating a thin layer of liquid gallium and tin onto a gold-thermoplastic-polyurethane film layer-by-layer. They say this allows them to get the desired deformability, unlike aluminium-laminated films.
First author Nyamjargal Ochirkhuyag says that a total of four layers are deposited – thermoplastic polyurethane, gold, liquid metal and then another layer of thermoplastic polyurethane. She adds, 'Thermoplastic polyurethane is used because of its excellent robustness and stretchability. Gold is used for adhesion between liquid metal and thermoplastic polyurethane to enhance the wettability of liquid metal.'
Accordingly, the films are reported to show excellent oxygen-gas impermeability under mechanical strain as well as extremely low moisture permeability. Oxygen gas permeation has been measured as 0cc/m²/24hr and moisture permeation at 0.0004g/m² for 15 hours. The film was stretched up to 20% for gas permeation measurement.
The stretchable lithium-ion battery that has been assembled is also said to operate reliably in the film.
The stretchable battery is assembled by placing stretchable electrodes and gel electrolyte in the gas barrier film, then the film is folded in half and sealed by a vacuum sealing machine. All components, including the electrodes, gel electrolyte and packaging have been tested using a uniaxial stretching machine.
Ochirkhuyag says, 'The stretchable battery would be replacing solid batteries that are currently in use in wearable electronics. It can be beneficial for reducing the size and weight of the devices.'
She notes, however, that the capacity of the device battery is lower than other lithium-iron-phosphate batteries or lithium-titanate batteries.
Their next steps are to enhance the film’s moisture protection by modifying the materials, and to improve the stability of the battery performance even under deformation. Making the film cost-effective will contribute to eventual scalability.