Spotlight: Polishing up post-heat treatment
Originally conceived for 3D-printed metal parts, a new surface finishing approach is finding application as a post-heat treatment process. Jonathan Housden, Project Coordinator at Wallwork in Cambridge, UK, gives us the lowdown.
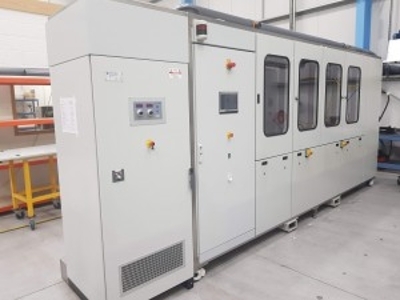
Somehow word had got around that R&D was about to start on an unusual experiment. Staff from all departments – coatings, heat treatment, vacuum brazing, machine build, lab and admin – had gathered expectantly, at a safe distance, around a lab table placed in the voluminous main production hall. This was not an experiment to conduct in an enclosed space. On the table, there was a rather Heath Robinson arrangement comprising a 2m-long plastic tube, pivoted in the middle from a retort stand and propped up on one end.
From one end of the tube, a metal test piece, connected to a large HT power supply, dangled over a 2L glass beaker of salt solution. This was counter-intuitive – dipping a metal object, connected to a high voltage power supply, into water. Everyone knows water and electricity do not mix well.
The crowd was not disappointed. In full PPE, holding one end of the plastic tube, the team lowered the test piece into the beaker while voltage and current were read out. Loud pops and crackles rang out in the hushed hall and sparks began to fly. However, the crackling quickly settled to a more continuous loud fizz and the sparks converged into a bright glow, lighting up the beaker. This was no ordinary electrolytic process – this was Electrolytic Plasma Polishing. Electrolysis with such high power that a gas envelope develops around the biased metal test piece and, within that gas envelope, a glow discharge plasma ignites, producing bright visible light while anodic dissolution removes material and smooths the surface.
Four years on, one Innovate UK Feasibility Study project, one European Commission Fast Track to Innovation project, and three iterations of prototype machines later, the beaker set-up has evolved and scaled up into a fully automated industrial polishing machine, CE marked and ready to ship to the first customer in France. Wallwork has collaborated with partners at the University of Manchester’s Department of Materials, the Fiat Research Centre in Italy, Poly-Shape in France and Wisildent in Italy.
Together with the machine development, the process has also been meticulously researched, developed and patented to include a series of carefully honed electrolyte mixtures and associated process parameters for rapid polishing of steels, titanium and other alloys without detriment to geometric, structural and corrosion-resistant properties.
Going back to its roots
The original idea for Plasma Additive Layer Manufacture Smoothing (PALMS) arose from an issue facing 3D-printed metal parts. Over the last two decades, additive manufacturing (AM) has progressed from 3D printers used simply for rapid prototyping to sophisticated manufacturing that can create parts directly from digital models without the use of tooling. AM technologies build up components layer by layer using materials that are available in fine powder form, producing near-net shape parts. The 3D-printed part is very close to the final shape, and enables a design-driven manufacturing process whereby highly complex, yet extremely light and stable, structures can be produced. AM provides a high degree of design freedom, optimisation and integration of functional features, the manufacture of small batch sizes at reasonable unit costs and a high degree of product customisation.
Critically, this unprecedented design freedom enables the production of lightweight optimised components that are impossible to make with traditional techniques, or bespoke components that would otherwise be prohibitively expensive if produced in small volumes. AM has the potential to vastly accelerate innovation, compress supply chains, minimise materials and energy usage, and reduce waste.
Despite the significant progress made in AM, the surface roughness of parts produced by this method continues to be an issue. Rough surface finish on AM parts causes wear, corrosion, fatigue, micro-cracks, poor tolerances and is aesthetically displeasing. These negative characteristics often outweigh the benefits of unlimited complexity of shapes and weight reduction. Post-processing finishing methods exist for reducing roughness, but these can be costly and have limited effectiveness, particularly in relation to complex-shape components with high surface roughness. As a result, the application of AM parts in industry is being constricted, particularly in the aerospace and medical industries, where the surface finish of components is highly critical.
PALMS is a multiscale finishing solution based on electrochemical plasma technology. AM parts with original macro finish (10-50μm) are rapidly treated in a highly controlled manner in less than 20 minutes, leaving a uniform, smooth micro-finish of less than 0.1μm in Ra roughness, improving aesthetics and mechanical performance.
In non-PALMS-treatable zirconia, as an example, an increase in surface roughness Ra from 1 to 3μm results in fracture toughness falling from 6 to 2MPa.m1/2. PALMS addresses this type of issue by providing a fast, cost-effective, environmentally friendly method of producing smooth finish (Ra <1.0μm) on AM parts, facilitating widespread adoption of AM by aerospace, biomedical and other sectors.
By cost-effectively producing a quality finished part – of almost any common metallic material, shape and complexity – in a time-efficient manner, PALMS removes a significant barrier to widespread adoption of AM technology and creates a step-change finishing method for the sector. PALMS will be an enabling technology for AM in aerospace in areas such as interior structural components, fixtures and fittings, parts in fluid-flow applications such as turbines, impellers and filters, and high-performance components such as nozzles, manifolds and internal flow-channel systems.
Honing the prototypes
In the initial Feasibility Study project, the team worked closely with Dr A Yerokhin’s group at the University of Manchester’s Department of Materials, who advanced fundamental understanding of this technology. The work featured in the academic journal Electrochimica Acta in 2019. The first prototype PALMS machine was developed and the electrolyte for polishing stainless steels was optimised, achieving a short process time and producing a tailored finish. As a simple initial investigation, the feasibility of polishing complex geometries, inner and outer surfaces, and holes with different aspect ratios was evaluated.
Changes in material properties were assessed using X-ray diffraction and microhardness testing and applied electrochemical impedance spectroscopy to evaluate any changes in corrosion resistance. The comprehensive study was detailed in a 2020 Additive Manufacturing journal article and showed no detrimental effect in treated surfaces – in fact, it demonstrated a slightly improved resistance to mechanical and corrosion attacks.
A second iteration of the PALMS prototype machine allowed increased sample handling and automation. A major challenge was to develop an electrolyte for PALMS polishing titanium alloys without leaving a tarnished surface. Careful tweaking of the electrolyte ingredients achieved a sparkling finish. Electrolytes for other alloys, such as other steels and cobalt-chrome, in various surface states and finish conditions were also optimised.
Finally, a third iteration of the prototype PALMS machine resulted in two industrial-scale, fully automated, pre-production machines, incorporating all the knowledge gained from the previous machines and electrolyte and PALMS-process development.
Applications in heat treatment
Heat treatment can leave a thin oxide film on the treated part, particularly from tempering. Comparatively low tempering temperatures, even under vacuum, tend to leave a light oxide especially on highly alloyed materials. If the part is net-shape and requires no further machining, then often the oxide must be removed before the item goes into use. This is particularly important if the item is to be coated after heat treatment. Coatings generally do not adhere well to oxidised surfaces.
PALMS polishing offers a fast and cost-effective method of cleaning these components of their superficial oxides, both simple and complex geometries. Many parts fall into this category, including plastic mould parts, press tools, precipitation hardening stainless steels 13-8PH, 15-5PH, punches, wheel studs for motorsport in 13-8 precipitation hardening stainless steel (for example prior to titanium nitride coating).
A similar issue arises with plasma nitrided parts. Removal of the top brittle compound layer, consisting of either epsilon or gamma prime phases (primarily pure nitrides of iron), is necessary prior to coating. PALMS can quickly and efficiently remove these compound layers.
Examples of relevant parts include plastic welding electrodes in 304 stainless steel and S600 tool steel, cutting discs in stainless steel, cutting blades in high speed steel, as well as motorsport spindles in stainless steel and F1 damper rods in maraging steel S162 that need
pre-treatment prior to deposition of diamond-like carbon coating.
Heat treatments can be combined to obtain the best properties, such as hardening and tempering, to provide core hardness. The key to success here is in removal of surface oxide prior to plasma nitriding, which gives the material appropriate load support, and then compound layer removal prior to applying the hard-wearing physical or chemical vapour deposition coatings.
At present, oxide removal or compound layer removal are carried out by light grit blasting, which then requires a mechanical re-polish. These two steps can be replaced by a few minutes single-step of PALMS polishing.
The finishing line
Industrial trials are underway on both ALM and traditionally manufactured components ranging from cold-forming tools to dental scaffolding. In some cases, PALMS has reduced polishing times from half a day of hand polishing to just ten minutes, while maintaining product dimensions and structural integrity. Proposals are currently being invited for additional industrial trials.