Smashing nano-technique hardens metals for manufacturing
Manufacturing metals at the nanoscale can make them four times harder, claim scientists at Brown University, USA. By smashing individual metal nanoclusters together, they customise metallic grain structures from the bottom up to form “macroscale hunks” of solid metal.
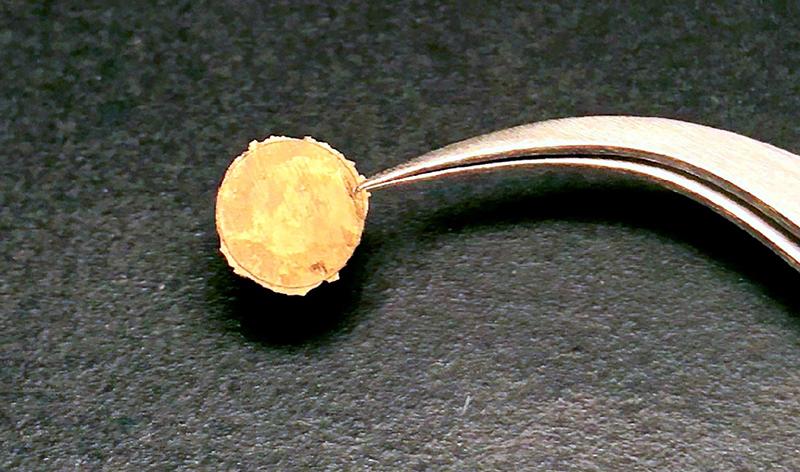
‘Hammering and other hardening methods are all top-down ways of altering grain structure, and it’s very hard to control the grain size you end up with,’ says Ou Chen, Assistant Professor of Chemistry at Brown.
‘What we’ve done is create nanoparticle building blocks that fuse together when you squeeze them. This way we can have uniform grain sizes that can be precisely tuned for enhanced properties.
‘We used our home-made pressure piston cell to press the nanoparticle building blocks and fuse them together. Since the required pressure is not very high, the process should be easily scaled up for large scale production.’
Since the grain conditions of the final bulk metals are determined by the nanocrystal building blocks, the team are able to control the size, shape, crystallinity and composition of the nanoparticles to control the grain condition of the bulk metal.
Using nanoparticles of gold, silver, palladium and other metals, the researchers have made centimetre-scale ‘coins’. To confirm the hardness of the materials, they conducted nano-indentation measurements.
‘In this way, we can have a much better and precise control of the grain conditions of the bulk metal,’ Chen notes. ‘In addition, since these nanoparticles are tiny and can be dispersed in solution, unlike most existing top-down methods, our method is potentially compatible with all the solution processing techniques, such as printing, spray, spin coating, etc.’
According to Chen, chemical treatment is central to the process – using sulphur and azanide to strip away the ligands, which typically prevent the formation of metal-metal bonds between particles. They achieve this by modifying the surface to exchange the long organic ligands – originally on the nanoparticle surface – to small inorganic ones, and then washing the nanoparticles to remove the inorganic ligands. This allows the clusters to consolidate with only a little pressure.
Taking the smashing one step further, the team has demonstrated that they can make an exotic form of metal known as a metallic glass.
‘This is the first time making a single-metal-component palladium metallic glass – taking the unique advantage of the possibility of making amorphous palladium nanoparticles,’ Chen continues. ‘Making metallic glass from a single component is notoriously hard to do, so most metallic glasses are alloys.
‘There will be a lot more studies and research that needs to be done to further understand this type of fundamentally new materials.’
Chen explains that the technique could be widely used for commercial products. ‘Since our technique is relatively simple without complicated set-ups, I believe this nanocrystal coining method has great potential in industry with large-scale production capabilities.’
The team will explore how to precisely control the nanocrystals’ size, shape and compositions, and aim to further understand the relationship between the grain boundary condition and the final properties.
Chen adds, ‘In addition, we are trying to expand the scope of this method to other metals and even non-metal materials with the hope of creating new materials that have never been discovered before.’