Pyrolysis and hydroformylation combined to recycle waste plastic
Post-consumer, high-density polyethylene (HDPE) has been converted into high-value chemicals by a research team in the US.
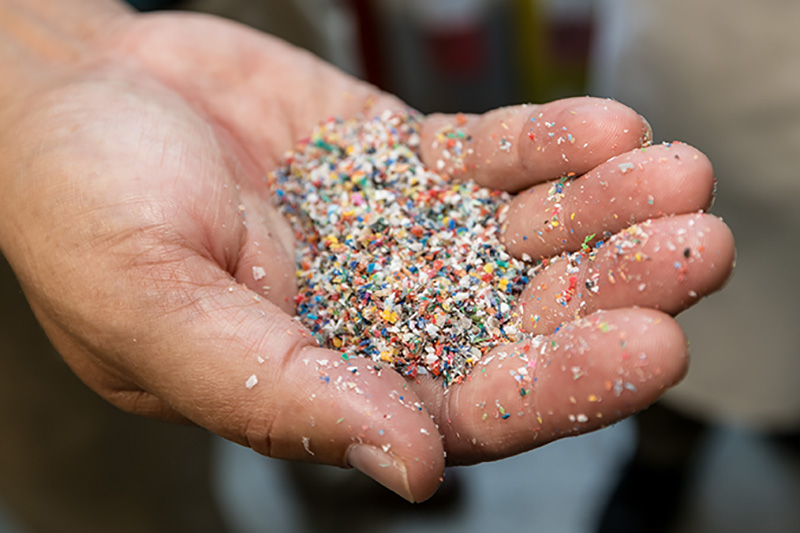
Two chemical processes – pyrolysis and hydroformylation – have been put together by a team at the University of Wisconsin-Madison, USA.
The group reports upcycling post-consumer, recycled, coloured, HDPE into a wide range of materials, including surfactants for soaps and cleaners, or polymers of a higher value than the original polyolefins.
Postdoctoral Researcher Dr Houqian Li adds that the method can produce high-value alcohols worth US$1,200-6,000/t from waste valued at around US$100/t, and that by using the prevalent methods of pyrolysis and hydroformylation, scaling up the process should be relatively easy.
The chemical engineers’ two-step process could reduce greenhouse gas emissions from conventional production of these industrial chemicals by roughly 60%, according to their model.
In current energy-intensive processes like steam cracking, chemical manufacturers produce olefins by subjecting petroleum to extreme high heat and pressure. In the new process, the UW-Madison team recovers olefins in the pyrolysis oil and then uses them in a much less energy-intensive chemical process called homogenous hydroformylation catalysis. This converts olefins into aldehydes, which can then be further reduced into important industrial alcohols.
'The overall yield of polyolefins from plastic pyrolysis, hydrotreating and steam cracking is less than 30wt.% from the virgin polyolefin. The overall yield of our approach is 60wt.% aldehydes from the virgin polyolefin,' Li says.
The coloured HDPE comes from an operational material recovery facility and is shredded into 2mm pieces to facilitate the feeding and reduce the reaction time for pyrolysis. Around 120g of waste plastics are processed per hour in a fluidised bed reactor.
The waste plastic is heated to 500°C for 20 seconds without oxygen to create a pyrolysis oil, which contains large amounts of olefins. The researchers then use fractional distillation to separate the oils into various cuts.
They then hydroformylate and hydrogenate the different cuts of pyrolysis oil. The hydroformylation process inserts a formyl group into the carbon bonds, thus generating aldehydes with one extra carbon. Dicobalt octacarbonyl (Co2(CO)8) is used to catalyse the reaction at 120°C, 70bar syngas in the absence of a solvent.
The aldehydes are hydrogenated into alcohols using a silica-supported nickel catalyst in a batch reactor or a continuous flow reactor. The team has modelled the downstream separation required for producing industrial alcohols and are now doing that in the laboratory.
The experimental results show that 50g of mono-alcohols and 12g of diols can be produced from 100g of post-consumer plastics, as well as 14.5g of aromatics, 20.9g of paraffins and 4.8g of side products – such as hydrocarbons, aldehydes, hemiacetals, esters and acids. The pyrolysis step also produces 18g of pyrolysis gas and 2g of char.
The team notes that at least 10 large chemical companies have built or announced plans for facilities to produce pyrolysis oils from waste plastics, many of which run the oil through steam-crackers. The team says their chemical recycling technique could be ‘more sustainable’ and more lucrative.