Pushing the boundaries - emerging 2D materials
Dr Aphrodite Tomou ProfGradIMMM, Technical Manager at Goodfellow Cambridge, UK, shines a light on three emerging 2D materials and their application potential.
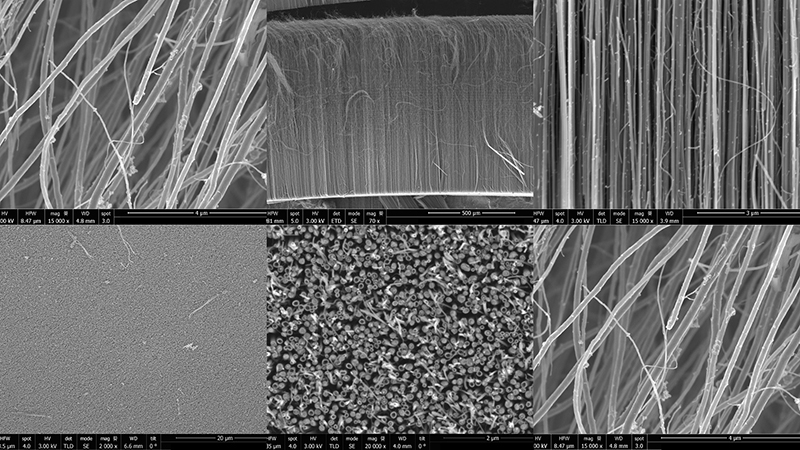
For research scientists, multi-wall carbon nanotubes, mass-produced ‘green’ graphene and boron nitride nanotubes, among other emerging 2D materials, provide an opportunity to not only push the limits of what we know, but also to discover and perhaps even create solutions to long-standing scientific mysteries.
Multi-wall carbon nanotubes
Multi-wall carbon nanotubes (CNTs) are freestanding, vertically aligned and called carpets or forests. They are synthesised by floating a catalytic chemical vapour deposition (CVD) method within a horizontal quartz reaction tube in an inert atmosphere (H2, C2H4). The catalyst used is an iron pre-cursor. The CNT synthesis parameters are carefully selected to provide maximum yield of CNT growth, high packing density and high graphitisation level. The graphitisation quality has been identified by Raman spectroscopy and has been calculated, ID/IG = 0.3-0.4, demonstrating a very low degree of defects. In addition, a differential scanning calorimeter (DSC) has shown a high oxidation temperature of 600-700oC. In the image below, Scanning Electron Microscopy analysis (SEM) demonstrates a high degree of alignment of thin and long CNTs.
Taking this into consideration, CNT carpets tend toward exceptional electrical and thermal conductivity. Due to their high structural uniformity, low graphitisation defect level and high degree of CNT alignment, they can be used in different applications such as in reinforced composites, filters, thermal interface materials, electronic devices and supercapacitors.
Green graphene
While CNTs are a promising due to their mechanical, thermal and electrical properties, it is graphene that has been labelled the ‘wonder material’. Because it has remarkable mechanical, electrical and thermal properties, it finds applications in a variety of sectors including energy storage, electronic devices, composite materials for aerospace engineering, or even, owing to its large surface area, as a filter for water desalination.
Recently, researchers have been focused on the mass production of graphene, a formidable challenge since the materials is mainly produced by either an exfoliation process, a reduced graphite oxide method, or chemical vapour deposition synthesis – processes that are hindered by several critical bottlenecks regarding scalability, purity, the high cost of production, etc. In response to this impediment to innovation, Goodfellow has introduced an ultra-pure ‘green’ graphene, guaranteed metal-free and applicable in metal-sensitive processes.
‘Green’ graphene is produced via a highly scalable process that involves breaking methane gas (CH4) – a very potent greenhouse gas – into hydrogen and elemental carbon atoms in a plasma reactor. The carbon atoms then recombine into graphene sheets in the hydrogen atmosphere. Elapsed time from the methane gas entering the plasma reactor to the point when graphene is formed is less than a second. This method produces a few layers of graphene which, after a special heat treatment process, become a predominantly one-layer graphene with exceptional properties. This green production process ensures that the graphene product has no additives, surfactants, catalysts or metal impurities.
The resulting graphene nanoplatelets are very thin, slightly crumpled and, unlike exfoliated materials, do not stack, ensuring optimal electrical, thermal and mechanical performance.
Specifically, the electrical conductivity of the predominantly single-layer graphene has been measured by the four-probe measurement on pellets technique (compressed under 10 bars for 20 minutes) and has a value of around 6100S/m. In addition, there is a high surface area value of around 320m2/g derived from nitrogen BET (P/P0=0.3), while graphite powder has a value of around 8.5m2/g.
These characteristics make this product a suitable nanofiller for electronic inks, polymers, metal composites and anti-corrosion coatings. Moreover, the speed and cost-effectiveness of this green mass production method could help make graphene readily available to a wide range of industries.
Boron nitride nanotubes
Boron nitride nanotubes (BNNTs) are attracting much attention in the research community and projected to become one of the most important materials in the fourth industrial revolution. Structurally, they are similar to CNTs – cylinders with sub-micrometre diameters and micrometre lengths (shown in the image above) – but with a notable exception. While CNTs have a carbon-constructed hexagonal structure, a BNNT is composed of hexagonal boron nitride constructed by combining boron and nitrogen.
The key features of BNNTs are light weight and mechanical strength comparable to CNTs. However, the properties of BNNTs are very different – whereas CNTs can be metallic or semiconducting depending on the rolling direction and radius, BNNTs are an electrical insulator material with a bandgap of ~5.5eV. Moreover, BNNTs have great thermal stability, as they can withstand up to 800OC in air, while CNTs can withstand only up to ~300oC.
Goodfellow’s high-purity BNNTs are produced by first ball milling a boron source (containing Fe) and then annealing under N2 and NH3 at 1,200oC in a nozzle-type reactor. Purification of iron particles at an early stage results in the BNNTs achieving one of the highest published purities (higher than 90wt%), if not the highest. In addition, a layered BNNT structure is much more thermally and chemically stable than a graphitic carbon structure.
Efficient heat dissipation is critical in the IT and electronics industry. There is an escalating heat dissipation problem that results from the high integration, miniaturisation, multi-functionality and lighter weight of electronic products – a problem that causes malfunction and shortens the lifetime of a device. One potential solution is an electrically insulating, heat-dissipating, epoxy-based composite material containing BNNTs.
Compared to CNTs, BNNTs have superior thermal and chemical stability as well as 200,000 times higher thermal neutron absorption capacity, enabling them to be used as a lightweight shielding structural material in aerospace applications that require exceptional radiation shielding performance. In addition, BNNTs are expected to become a suitable material for containers of radioactive waste from nuclear power plant operation, as they can be used as a neutron shield and absorber owing to their improved neutron absorption by 10B.
Toxicological investigations on BNNTs also reveal that the enhanced chemical inertia of BNNTs favours biocompatibility. As a result, they could have use in the biomedical field as nano-carriers and as nano-transducers.
The future
All of these materials can have an effect on a generation of devices and systems destined to improve our daily life. Specifically, the green production process for graphene is leveraging the material’s prospects for implementation and sustainability. Mass production and recent utilisation of graphene in commercial applications such as automotive and sporting goods is demonstrating that applications for 2D materials are rapidly reaching the marketplace and being absorbed into the mainstream.
Overall, organisations that implement strategies with hybrid composites of such 2D materials using recyclable or biodegradable matrices are contributing to a fundamental long-term impact on society, as environmental awareness is enhanced.