A greener path to steelmaking
The European Steel Association is embracing the EU hydrogen strategy as a way to introduce green steelmaking into industrial processes. But what are the most promising green steel technologies? And what are the limitations for industry adoption? Shardell Joseph reports.
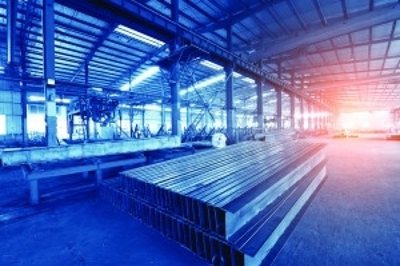
The European Commission’s hydrogen strategy unveiled in July sets out its goals for integrating an energy network to achieve carbon-neutrality by 2050. The European Steel Association (EUROFER) has since welcomed the move but warns that the ‘industry will need millions of tonnes of competitively priced hydrogen by 2050 to make its low-carbon transition a success’.
It adds, ‘Steel produced using new hydrogen and clean-energy based methods will be 80-95% less CO₂-intensive by 2050 than they are today, but will also cost significantly more to produce.’
EUROFER’s A Green Deal on Steel report outlines the potential contributions green steel could have on the European Green Deal. ‘European steel’s transition to carbon-lean, “green” steel requires a fundamental change in the way steel is made, because our current processes are already at the technical and thermodynamic limits,’ the document reads.
‘The benefits to society from the availability of hydrogen and green industrial products, such as green steel, are huge – so Europe needs to strive to make the energy transition as quickly and comprehensively as possible,’ adds Axel Eggert, Director General of EUROFER.
The European steel, mining and energy companies working on hydrogen-based steelmaking processes in a bid to become carbon-neutral include ArcelorMittal, Tata Steel, thyssenkrupp, voestalpine, Liberty Steel Group, SSAB, LKAB and Vattenfall.
The incentive?
Currently in the UK, steel continues to be dominated by the basic oxygen steelmaking (BOS) route, which starts with the reduction of iron ore with coking coal and uses around 20% of steel scrap in the process.
Imperative to UK industries such as construction and automotive, the contributions that the iron and steel sector make towards carbon emissions have been recognised. A 2019 University of Bath, UK, research paper, Industrial energy use and carbon emissions reduction in the iron and steel sector: A UK perspective, explains that the sector accounts for around 26% of greenhouse gas (GHG) emissions from British industry and is considered the largest contributor among all other sectors.
Jon Bolton FIMMM, steel industry advisor, adds that the blast furnace route (BF), meanwhile, generates 1.9t of CO₂ for every tonne of liquid steel manufactured. The steel industry represents 5% of global CO₂ generation. Increasingly, steel manufacturers are recognising the wide range of benefits that come with implementing greener processes. ‘Steel producers, by engaging in greener behaviour, can see their social image and stakeholder relationships improve, foster a creative environment at the work place and enhance their internal innovation capability,’ says Hasan Muslemani, Doctoral Researcher in Energy and Climate Change at the University of Edinburgh Business School, UK.
‘[They also] benefit from increased employee commitment as they engage with the employees’ social values, and, perhaps most critically, remain competitive in countries where companies have to abide by or adapt to stringent climate regulations.
‘A few recent global initiatives, such as ResponsibleSteel for instance, are working on setting a holistic certification standard for defining “responsibly-sourced” steel, of which GHG emissions during production is only one aspect,’ he adds.
Because there are few viable alternatives for steel, the industry is increasingly supporting and investing in emission reduction technologies. EUROFER explains that hydrogen and renewable electricity is needed to develop innovative technology for greener steel, as well as carbon capture and storage to get as close to zero emissions as possible.
However, the capital costs of transitioning are significant, estimated in the multi-billion-euro range. The costs of steel per tonne could be 35-100% higher, according to EUROFER.
‘Increases in cost due to greener production processes may risk seeing consumers switch to other local or overseas manufacturers who are selling cheaper, “browner” steel – the effect of this may be especially felt by first-market-movers as market support mechanisms are not yet in place,’ explains Muslemani. ‘This will in turn also raise concerns of carbon leakage.’
During a podcast recorded by the Institute of Materials, Minerals and Mining (IOM3), Chris McDonald FIMMM, CEO of the Materials Processing Institute and a Board Member of IOM3’s Iron and Steel Society, acknowledges the difficulties. He says, ‘If you want to switch from a process that is built around the use of carbon to a process that’s built around some alternative, then it means taking out all of that billions of pounds of capital investment and switching to something else. [It is] really difficult for a private company to be able to justify doing that.
‘When you reach the natural end of the lifecycle, then you are going to switch and reinvest anywhere. Now naturally, you would want to invest in the same technology you had just been using, that’s the safe thing to do.’
Muslemani asserts, however, that despite the higher costs associated with developing green steel processes, which may be hedged against available government incentives, green steelmakers can still capitalise from first-mover opportunity, developing a loyal customer base for their differentiated, environmentally-friendly products.
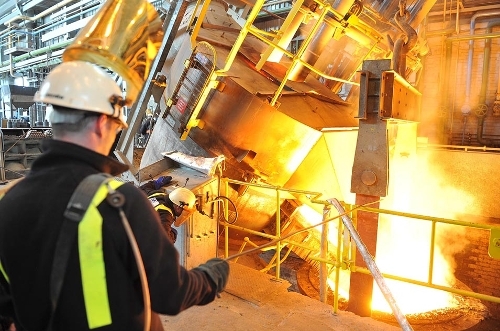
McDonald explains the industry can support the transition to green steel processes by promoting the financial benefits to investing in these technologies. ‘What we need to do is help the steel companies to invest in the new technology, which is a bit riskier for them, and embed them in that new technology for the next 20/30 years.’
Dr Alexander Fleischanderl, Head of ECO Solutions at Primetals Technologies, explores the potential changes steel manufacturers could witness by transitioning their processes. ‘One of the more immediate effects would be reduction of operating costs due to lower energy consumption. ‘But in the near term, many of the benefits to be gained from green processes will lie in avoiding the downsides of not having them – rising expenditure for emissions allowances in trading schemes and carbon taxes.’
Fleischanderl explains that if plans for a carbon border adjustment in the wake of the EU Green Deal move forward, whereby import fees are levied by carbon-taxing countries on goods manufactured in non-carbon-taxing countries, there will be another straightforward reason for producers to go green. Not adopting these changes could mean losing competitiveness at best and access to entire markets at worst, Fleischanderl adds.
Making the transition
The transition to green steelmaking is still in its very early stages. Like many other industries, carbon capture and storage technologies are considered an effective approach for reducing emissions and investment is increasing for industrial use.
In terms of transitioning steelmaking away from traditional BF and BOS approaches, one process gaining traction worldwide is the Electric Arc Furnace (EAF). Steel produced through the EAF route recycles scrap steel and needs to be powered solely by reheating furnaces using renewable energy with electrical or hydrogen to produce the finished product – e.g. beams, near-end shape blanks, rolled strip, etc. The technology’s significant reduction in emissions makes it a desirable alternative for industrial steelmaking processes.
‘Around 90% of the energy consumed in the BOS route actually comes from coal, which acts as a reducing agent, but just 7% from electricity,’ says Brian Edy FIMMM, Director of the Steel and Metals Institute at Swansea University, UK, and Board Member of IOM3’s Iron and Steel Society, in an IOM3 podcast.
‘For the EMF routes, the energy input from coal is only around 10% with 50% coming from electricity and 40% from natural gas, so, they’re quite significantly different production routes in that sense.’
According to Edy, in the future, the surplus of steel scrap may eliminate the need for BFs and avoid the need to transport and convert millions of tonnes of virgin material. ‘An EAF will emit a third of the CO₂ emitted through a BF route. Theoretically, if you use renewable energy, then you can further reduce the generation of CO₂.’
Edy claims that the proportion of steel produced by the EAF process in the UK is lower than the world average. ‘The EAF route lends itself more to commoditised products such as steel reinforcing bar on the one hand, as is used in construction, or where high purity products and tight specifications are needed as in the production tiers for aerospace, like aircraft landing gear, for example.’
There are significant capital considerations for making the switch. A 2010 document from the International Energy Agency reported that investment costs are approximately US$100/t for a BOS, the capital cost for EAFs, however, amounts to around $220/t a year. ‘EAF production consumes significantly greater amounts of electrical energy than the BOS process,’ says Edy. ‘So, if you want to switch from BOS to EAF, not only are you having to use more electrical energy, but you have to use a lot more very expensive electrical energy.
‘And if we look at the consumption levels just in terms of electrical energy, production consumes roughly speaking about 2GJ/t compared with 1.4 GJ/t for the BOS route.’ Bolton notes how the costs increase substantially when reducing impurities and using very clean scrap. ‘This is why companies such as Liberty UK have a two-pronged approach – they will invest in EAFs where possible but maintain some BF capability and look to adopt low-carbon methodologies such as the use of hydrogen.’
He continues, ‘Reduced CO₂ is of course ecologically the most important reason but costs can also be reduced – both operational and capital – as an EAF is a simpler piece of kit costing less capital than an integrated steelworks and requiring less people to operate it. ‘An EAF is also more flexible as you can switch it on and off easily. This is not the case with a BF and associated processes such as coke ovens. They have to keep running or else the kit can be badly damaged.’
Propelled by policy
Experts acknowledge the responsibility of steel manufacturers to promote and invest in green technologies, but there is a consensus that this is not possible without government support. Fleischanderl highlights that it is likely to be state actors that will lead the charge on fostering green steel consumption. ‘The German government, for example, makes this point quite explicit in its recently presented action plan on steel – Handlungskonzept Stahl – which comprises a national roadmap for a sustainable future of the German steel industry.
‘We have no doubt that other European governments will follow suit, and with public construction works expected to increase in order to counter the [current] downturn, state actors have quite a lot of weight to throw around as steel consumers.’
Fleischanderl adds, ‘What’s even more important is that large consumers in the private sector, which are to various extents dependent on government support, like the automotive industry, will come under increasing pressure to include green steel in their supply chains as well.’
Muslemani puts forward how governments can make a marketable case for green steel production. Firstly, intervention through public procurement, and secondly, setting a certified standard for green steel.
‘Regulatory mandates could be ratified to ensure that a certain amount of green steel is purchased by large consumers – two analogies here are the use of Energy Performance Certificates in new building regulations and technology – forcing policies such as the US Clean Air Act which seeks penalties for vehicles not complying with certain emission standards. Governments can protect green steel exports by ensuring products retain privileged access to certain markets.’
He adds, ‘It is evident that no single policy will bring green steel to the market on its own, and that a combination of complementary measures might be needed to support and protect a green steel market.’
Hot opportunity for the UK
The UK Government has made commitments to green technology, claiming that it will launch a Research Fund for clean steel and hydrogen in 2024, which will run through till 2030. ‘Whilst that’s helpful, I think the timescale is just too long, it’s too far away,’ admits McDonald.
‘Work really needs to start now to catch up with our competitors. And this is competitors, not only from an industry perspective, but also from a national perspective as well – there’s the risk of the UK falling very severely behind other countries in terms of our efforts to decarbonise.
‘What we need is a policy that reflects the carbon embedded in imported products and puts our industry on a level playing field and…I fear without that, it will never be hugely competitive to take up this opportunity to invest in the UK.’
Muslemani adds that companies may have fundamentally – different technologies in place to produce green steel – the local context is key. It’s a point echoed by Richard Curry, Research Programme Manager of the Sustain Steel project at Swansea University. ‘The UK has an amazing opportunity to lead the green steel revolution, just as we led with industrialisation. The fact that we only have two integrated BF plants and three large EAF steel plants means that the number of emissions point sources is low and can be tackled with great effect very easily. As an example, if the Port Talbot plant was fitted with carbon capture, storage and usage, it would cut UK industrial emissions by almost one third.’
McDonald states that there is a societal shift here that industry must recognise. ‘The UK Government has got a net-zero target of 2050. And I know a lot of companies are building their investment plans around being able to hit that target on time. ‘But as I keep pointing out to people in the industry, the people who you are going to employ in 10 years’ time in 2030 are currently 10 years old, and the people you’re going to seek to employ in 2040, who will be vital for running your business, haven’t even been born yet.
‘I think we have to recognise as an industry that we might not have the luxury to get to 2050 and continue to survive. Deadlines like 2030 and 2040 will be determined by the communities in which the steel industry operate as being acceptable deadlines to decarbonise. So that urgency and pressure runs far faster than legislation and so the technology needs to be implemented much more quickly.’
Steel solutions
The Sustain Steel hub, based at The University of Swansea, UK, is a £35mln project funded by research councils, universities, trade bodies and industry. The project ambitions include developing systems for carbon neutral iron and steelmaking by 2040, doubling steel gross value added by 2030, and implementing intelligent infrastructure by 2030.The researchers within the hub aim to achieve this via multidisciplinary collaboration and influencing UK research, providing skills training through an outreach programme, influencing policy and setting the agenda for future skills, creating commercial solutions for reaching net-zero and providing smart processes for smart products.
The UK’s Materials Processing Institute is also working on technologies to enable a zero-carbon and zero-waste steel industry. Challenges such as hydrogen reduction of iron ore, or making low nitrogen and low residual steels from scrap-based Electric Arc Furnace (EAF) technology, form part of the Institute’s innovation strategy.
With research teams in advanced materials, decarbonisation and the circular economy, plus facilities in EAF steelmaking and continuous casting, the Institute is working with partners in the industry to accelerate commercialisation of green steel technologies in the UK, Europe and beyond.