Paper mill packs in carbon savings
A more efficient drying process at Smurfit Kappa’s paper mill in Kent, UK, is reported to have reduced CO₂ emissions by 5%.
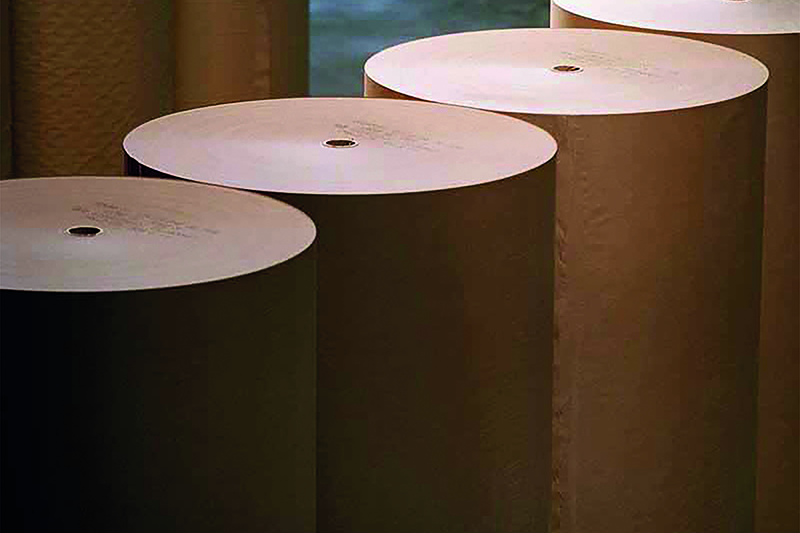
The emissions savings at the Townsend Hook paper mill comes from reducing steam energy by 6% with decreased water and power usage.
Darryl Jackson, Smurfit Kappa UK Operational Excellence Manager, says that there is no change in the performance or quality of the products made.
'The previous controller was a normal proportional-integral controller regulating the variables we set. The new technology allows the drying process to consider the conditions of the paper machine when optimising the running variables to ensure the most energy efficient control range,' says Jackson.
The European paper and packaging manufacturer uses a digital twin to simulate the new process in advance to accurately gauge its future performance.
Jackson explains, 'Our digital twin partner – Automation X – worked closely with our local team to collect data, understand the process and its limitations. A detailed verification process was undertaken with our project partners P.I.T.A, Automation X, Perceptive Engineering and the Carbon Trust, followed by a factory acceptance test whereby the pass limit was 95% accuracy of digital twin versus reality.'
Like many long-term projects over the last couple of years, the group collaborated remotely, which Jackson says made the sharing of technical information more complicated.
Smurfit Kappa is trialling this method in other manufacturing areas and is hoping for similar results. The company aims to reduce its CO₂ emissions by 55% by 2030 from a 2005 baseline, leading to CO₂ net-zero by 2050 at the least. It says the 2030 reduction targets have been independently validated by the Science Based Targets initiative as aligning with the Paris Agreement.
'We will deliver on our 2030 targets through ongoing continuous improvement, greening of our Scope 2 grid supply in Europe, and through specific projects like, a new recovery boiler to boost energy optimisation at our Nettingsdorf Paper Mill, a re-design of the multi-fuel boiler at our Zülpich paper mill in Germany, and investment in a biomass boiler for our Cali paper mill in Colombia.
'We are also experimenting in new technologies today to take us beyond 2030, including trialling hydrogen at our Saillat paper mill in France and geothermal in the Netherlands.'