Liquid metals make light work of carbon storage for industry?
Australian researchers have created a new carbon capture and storage (CCS) method that they claim instantly and permanently locks carbon away in solid form.
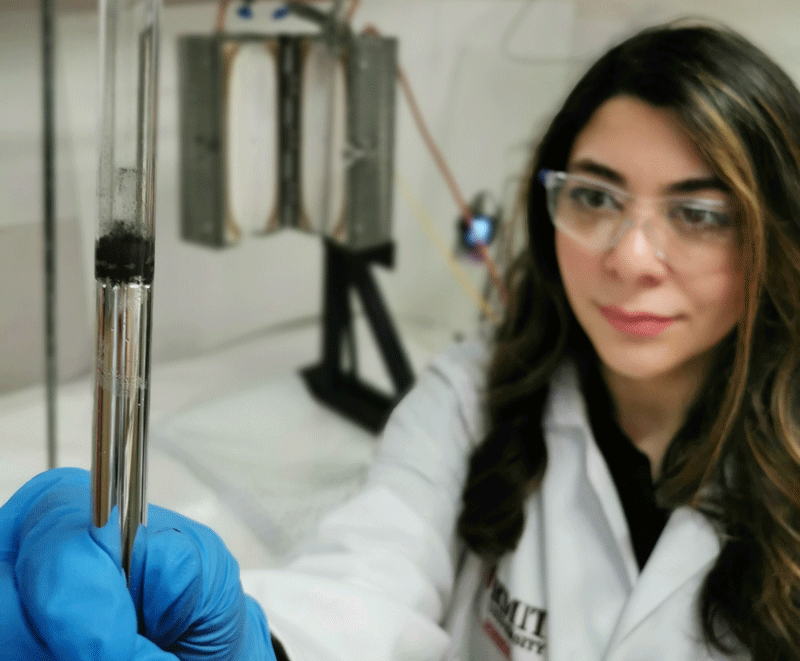
The team from RMIT University, Melbourne, suggests their method can be integrated into existing industrial processes – capturing and storing carbon as a solid securely and indefinitely.
‘Our main aim is to offer an alternative solution for industries that are difficult to decarbonise, such as cement and steel manufacturing,’ says lead author Karma Zuraiqi.
The RMIT team has built on previous research where they have observed liquid metals acting as electrocatalysts capable of reducing CO₂ to solid carbon. This process uses a ‘bubble column’ method. The liquid metal is heated to 100-120°C and as the gas bubbles rise, the molecules split to form flakes of solid carbon. This reaction takes only a split second.
Gallium-based liquid metals have been found to work particularly well – specifically, pure gallium and a eutectic gallium indium alloy, commonly known as EGaIn, due to their low melting points. ‘The use of EGaIn (with a melting point of 15.5°C) allows for the decomposition of CO₂ to solid carbon at room temperature, which can take us a step forward in the thermal conversion of CO₂ space,’ says Zuraiqi.
As the carbon is significantly less dense than the molten gallium, and insoluble in the liquid metal, it accumulates on the surface where it can be easily skimmed off. The metal’s high density also allows for a large amount of CO₂ to be converted.
Many other CCS methods compress gas to liquid and inject it underground, which can be expensive and energy intensive, the research team notes. They suggest their method is straightforward, avoids leaks and has the potential to provide reusable carbon.
‘Our process is very efficient, meaning that in the short time it takes for a CO₂ bubble to travel through our reactor, a significant percentage is captured and converted. With proper engineering design, it is possible to convert all CO₂ in a gas stream into carbon,’ Zuraiqi explains.
The group is currently focused on CO₂-rich exhaust streams. ‘Although it is technically feasible, separating and converting CO₂ from the air does present challenges in its economics due to its relatively low level in air,’ Zuraiqi continues.
RMIT is collaborating with a cement manufacturer, ABR Global, Australia, to scale up the proof-of-concept to a modularised prototype of shipping container proportions. ABR has put forward AUS$2.6mln to commercialise the technology to decarbonise cement and steel manufacturing. As well as reducing their carbon footprint, ABR hopes to turn a waste product into a core ingredient for their next generation of cement blends.
‘We are working closely with the engineers from ABR to design a modularised system to meet the throughput requirement of different processes, i.e. different flow rates of CO₂,’ Zuraiqi says.
During integration, the team will investigate whether the waste heat could offset and reduce the energy required. The relatively low temperatures to heat the metal also presents the possibility for using renewable energy.
She adds, ‘The process economics will be one of the important factors on whether a pre-reaction capture process is needed.’ This pre-capture could remove nasty contaminants and reduce the volume of gas to be handled.
The team is also exploring whether the liquid metal can be reused after regeneration, either continuously or batch wise in a cyclic manner. ‘Different industries have different needs, and we would like to learn more about different processes and their individual challenges,’ Zuraiqi concludes. ‘Carbon-based materials are generally valuable and find application in a wide array of industries.’