Keeping the kilns burning
As the UK ceramics sector navigates high costs and pressure to decarbonise, there was much to discuss at an industry event.
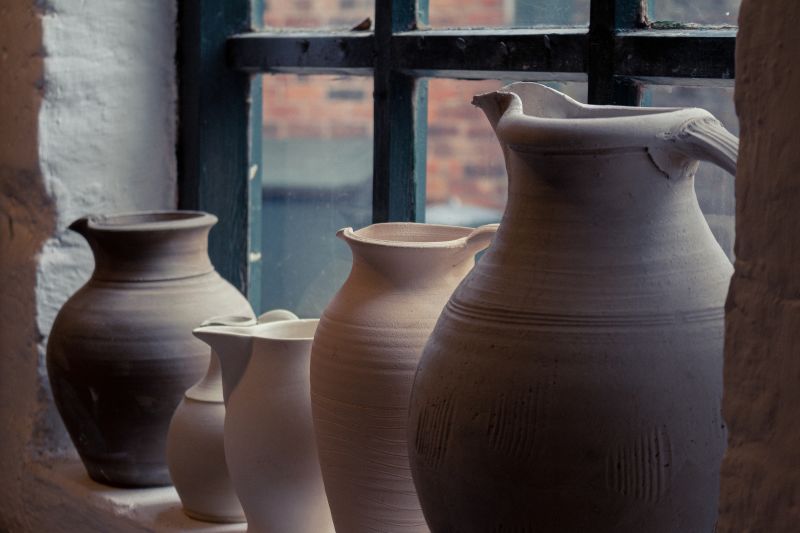
Last month, trade body Ceramics UK issued a damning rebuke to the UK Government. It says promises of support in the recent Industrial Strategy have not materialised.
Ceramics UK is now urging the government to rebalance its strategy and ensure critical manufacturing sectors are not left behind.
Rob Flello, Chief Executive of Ceramics UK, comments, 'We find it incredulous that the Department for Business, the Department for Energy and the Treasury still do not seem to understand that energy-intensive doesn’t just mean electro-intensive. Ceramics needs help with gas prices.
'Ministers and MPs, including Secretary of State Jonathan Reynolds, have publicly acknowledged that ceramics is one of the hardest sectors to decarbonise. However, when the Industrial Strategy was released, ceramics was barely mentioned and, even then, the reference failed to recognise that this is a national industry, not a regional footnote.'
Support for the sector is all the more pertinent says Ceramics UK, as the sector navigates its roadmap to net-zero by 2050.
The annual ‘Delivering Net Zero Conference’, held by the organisation on 17 June (before the release of the Industrial Strategy), saw industry peers, policymakers and experts share insights on decarbonisation projects, research, emerging technologies and the evolving regulatory landscape.
David Dalton, Chief Executive of the British Glass Manufacturers’ Confederation, speaking at the event, corroborated the view that the impact of high-energy costs on industrial sectors such as ceramics and glass needs to be better amplified, noting the 'impact that has on society and the economy.
'Despite all the great things that we’re doing, we find ourselves continually eroding away. And I think we need to buck that trend.'
Three years ago, he told an audience in Liverpool that in his near-50 years in the UK glass sector, he had never seen output significantly fall, with 3.3-3.5Mt consistently produced. In the same timeline, industry emissions had fallen from ~3Mt to 1.2Mt.
However, in the last two years, production has dropped by more than 20%. 'It is desperation stakes,' he said. 'If we’re going to survive, we’re going to need recognition. We’re going to need support, and we’re going to need investment by government to get there, and that’s going to be a difficult journey.'
Dalton questioned whether any government truly engages enough with industry to fully understand the problems. But he was also passionately clear that he believes the expertise exists within industry to decarbonise, while keeping industries buoyant.
State of ceramics
Ceramics UK President Hannah Ault reflected that news about sector challenges were inescapable, with several businesses recently closing, particularly in Stoke-on-Trent where the conference was held.
This is nothing new, she said, with many well-known and long-standing brands pushed to the brink by high costs. This has impacted UK competitiveness, leading to many companies being undercut by those without equivalent obligations and costs.
Ceramics UK has long called for more government support, pointing out that the UK sector employs a similar number of people to the British steel industry.
Ault noted, 'In terms of global uncertainty, ceramics are essential to UK supply chain resilience across the whole economy, and crucial for delivery of government targets such as for house building.'
Ahead of the fall-out over the recent Industrial Strategy, the sector welcomed the £86bln boost for government funding in R&D and clean energy investment. But Ault asserted the ceramics sector urgently needs targeted funding for technology roll-out, electrification and access to hydrogen, as well as provisions against carbon leakage to be maintained.
UK ceramics are still highly renowned for quality, design and innovation, Ault remarked, but adaptation strategies can only go so far. 'We’re simply asking for fairness to be able to compete, where quality UK-made goods itself will be a positive differentiator, rather than simply based on cost.'
The organisation’s new 2050 roadmap is seen as the big hitter of decarbonisation (see box-out below).
Roadmap to decarbonisation
The Decarbonising UK Ceramic Manufacturing Roadmap from Ceramics UK, published last year, outlines how sector decarbonisation is challenging due to the dispersed nature of UK production sites, mostly SMEs, with emissions that are difficult to abate. Not to mention, diverse processes and products, including clay brick, clay roof tiles, wall and floor tiles, sanitaryware, tableware, technical ceramics, refractories and suppliers to the industry.
Decarbonising the UK ceramics sector by 2050 requires emissions reductions of 94% from the 2019 baseline, of which 14% are expected to come from efficiency measures, 36% from hydrogen and 15% through carbon capture.
The projected timeline for emissions reductions are:
- By 2030 – process emissions by 7% through product adaptation or material substitution; direct emissions by 16% through improved efficiency, hydrogen and electrification; and indirect emissions by 69% through onsite renewables or grid decarbonisation. This could come to an overall 19% reduction
- By 2040 – process emissions by 15%, direct emissions by 45% and indirect by 100% = 43% reduction
- By 2050 – process emissions by 68%, direct emissions by 104% and residual by 6% of baseline = 94% reduction
Digging into the data
A dizzying array of data from a six-month project provided an overview of sectoral changes over the last 25 years. Lee Brownsword, Ceramics UK Associate Director of Industrial & Environmental Policy, led the charge.
From 2003-19, the UK ceramics sector reduced its Scope 1 & 2 by 53%, and carbon intensity decreased by 24%, with lower-carbon fuel and less energy demand. Many factories have been converted to be more efficient, reflected Brownsword, plus upgrades such as heat recovery, new refractories and renewable power.
However, 45% of that overall reduction is due to factory closures. While the sector has benefitted from a Climate Change Levy and free allocations through the Emissions Trading Scheme (ETS), many economic events over the last 20 years have taken their toll.
Gas prices rose 800% from 2000-23, Brownsword highlighted, with the UK losing its competitive advantage. Also, the industrial electricity price in Great Britain has gone up 600%, higher than competitor countries.
The Office of National Statistics recently published a 30% reduction in UK industrial output between 2021-24, which is 'deeply worrying', Brownsword said.
He remarked that 'the UK is grossly out of kilter', and, like his colleagues, stressed, 'ceramics has not had the support of other energy-intensive industries'.
It was bad news on carbon costs too. In 2000, carbon emission traded funds for sites in the UK ETS was 5% of industry revenue, rising to 25% in 2023.
The sector had pinned its hopes on the Industrial Strategy and now feels it was led up the garden path. The conference was also informed that the government is closing its Industrial Energy Transformation Fund.
The crux of it is that ceramics manufacturing has many characteristics that make decarbonisation difficult, heard delegates. There are many processes and diverse manufacturers that are predominantly small emitters, requiring high-temperature firing. All this contributes to an energy and carbon-intensive industry.
While the roadmap highlights transition technologies, these will not be implemented overnight, Brownsword said.
And although energy and carbon are big expenses, there are other burdens, such as recent employment tax changes. 'As a labour-intensive industry, that has a big impact, particularly in tableware,' Brownsword highlighted.
'What we really need is government to be thinking about consumption emissions, so looking at what the UK is consuming as opposed to what it’s producing,' Brownsword said.
In 2019, 94% of the UK ceramics sector was based on heavy clay construction products, with 4% technical ceramics and refractories and 2% whiteware goods.
In 2000, only 19% of UK-consumed whiteware goods were domestically made, falling to 4% in 2019, although tiles and sanitaryware skew the picture, he caveated. The remaining whiteware sector has adapted, he noted, playing to strengths in quality, design and innovation, with world-renowned tableware and giftware.
In 2003, 96% of clay construction products used in the UK were made here, which was 79% in 2019, a reflection of the construction and housing sector.
Overall, in the last decade, imports of ceramic products have risen, predominantly from the EU, and while non-EU volumes are comparatively small, Brownsword sees a potential tipping point. In a nutshell, the UK has doubled imports, reducing exports, with a £1bln trade deficit and growing. With upcoming decisions around the UK ETS and carbon leakage review, 'If we deviate from the European approach and have a loss of free allowances, this really threatens business viability and investment'.
His team assumes EU emissions are UK-equivalent, but non-EU emissions data is completely lacking. 'It is a real frustration for us, and that we know many are using higher-carbon fuels and very inefficient processes.' A sensitivity analysis of non-EU goods assumes they are 10, 20 or 30 years behind the UK.
Whiteware goods are reported to have the highest carbon intensity at 1.1tCO₂/t, due to multiple firings and more raw material preparation. Technical ceramics and refractories fire at higher temperatures and generally use intermittent kilns, so average 0.56tCO₂/t. Finally, heavy clay construction products have a single firing but more continuous production processes, so are allocated an average 0.22tCO₂/t.
However, from 2003-19, UK whiteware production reduced its carbon intensity by 29% and 74% in absolute emissions, with a similar picture for technical ceramics and refractories.
All emissions from ceramics products used in the UK are estimated to be down 33% from 2003-19 – a 53% reduction in absolute emissions for UK-made products, a 9% decrease for EU products and 0% change for non-EU products in all three scenarios.
Brownsword asserted, 'The rates of imports are rising and simply offsetting improvements that we’re seeing. This is quite simply, offshoring of production and emissions.'
Where will additional products originate for government housebuilding goals, Brownsword asked, and at what cost?
Firing up hydrogen?
Hydrogen is a fuel vector the sector is particularly excited about. Andrew McDermott FIMMM, Ceramics UK Deputy Chief Executive, explained that switching to hydrogen firing could save ~450,000tCO₂ p.a. across the sector, ~36% of its emissions.
McDermott updated attendees on Ceramics UK’s hydrogen trial. In phase one, 100% hydrogen firing of ceramics was tested on a modified glass rig, for whitewares, heavy clay and refractories. Hydrogen firing was deemed economically feasible without impacting the product, potentially cost-effective by the 2030s and optimal by the 2040s.
The second phase involves 13 Ceramics UK members and four external partners. A 4m³, 2.2t, 1,500°C max-specified kiln that runs on methane, hydrogen and blends had its first trial in September 2024. Early results show that NOx emissions were 2.5 times higher with hydrogen.
McDermott said the key is that hydrogen products have the same performance as those fired with methane, referencing two Wienerberger brick test bodies.
Despite no in situ demonstrator, Ceramics UK has developed five models – two for heavy clay, one under reduction conditions and one under oxidation conditions; a batch kiln model for refractories; and one each for whiteware and technical ceramics. They expect results in quarter 3 of 2025.
While kilns can be modified without stopping, McDermott emphasises the industry needs a firm commitment that hydrogen supply and distribution networks will be available in the future.
In a panel discussion, Clare Jackson, Hydrogen UK Chief Executive Officer, summarised the chicken and egg problem. 'The reality is no one wants to produce hydrogen. There are no off-takers, and nobody’s going to switch to hydrogen when there’s not that sort of security of supply.'
She praised the UK Government’s hydrogen allocation rounds and carbon capture track cluster process to accelerate deployment, as well as recent announcements of £500mln for transport and storage infrastructure, with end-users including power stations and industry. Having multiple off-takers in the same geographical location is really important, she noted.
Chloe Tindale, Air Products’ Hydrogen Strategic Marketing Manager UKI, insisted there is hydrogen availability now. The Fuel Switching for the Ceramics Sector project started off with two trailers, that could grow to a liquid supply before an electrolyser or grid connection.
For dealing with NOx emissions, she suggested blending oxy-fuel, before merging it with hydrogen when ready.
Blending with gas is extra security for producers, Jackson said, so if an off-taker goes down they can still blend their hydrogen into the network, reducing risk for first-user projects.
She referenced the HyDeploy project in the North West, which concluded that ~20% hydrogen can be blended into the gas network. A National Gas project in Spadeadam, Cumbria, has tested blends and 100% hydrogen in pipes of all ages and types, and shows existing networks are workable.
Hatty Culver, Policy Lead for Industrial Hydrogen Demand at the UK Department of Energy Security and Net Zero, noted that strategically locating electrolysers to be the most profitable for the grid, might not correlate with suitable geological storage.
'We have seen today that hydrogen [is] not going to be easy for us, but it’s probably easier than the alternatives,' said David Manley, Head of Sustainability at brick manufacturer Forterra, noting the barrier of onsite generation with electrification. He thought a hydrogen connection more likely.
Manley concluded, 'We really need to get off the fence and start committing to the transition, that’s us as businesses as well as the government, investing in the networks.'
Jackson listed three reasons to be confident in hydrogen decarbonisation. One being the staggering pace of development for a nascent industry, with the UK’s Hydrogen Strategy only four years old, and there is now a policy framework, a project pipeline and the first projects have signed contracts with government and will be taking investment decisions this year.
There is much to be optimistic about, but also many concerns still about securing the future of the UK ceramics sector.