Iron makes a play for hydrogen fuel cells
Iron, carbon and nitrogen catalyst could replace costly platinum to produce hydrogen fuel cells, say researchers at Imperial College London, UK.
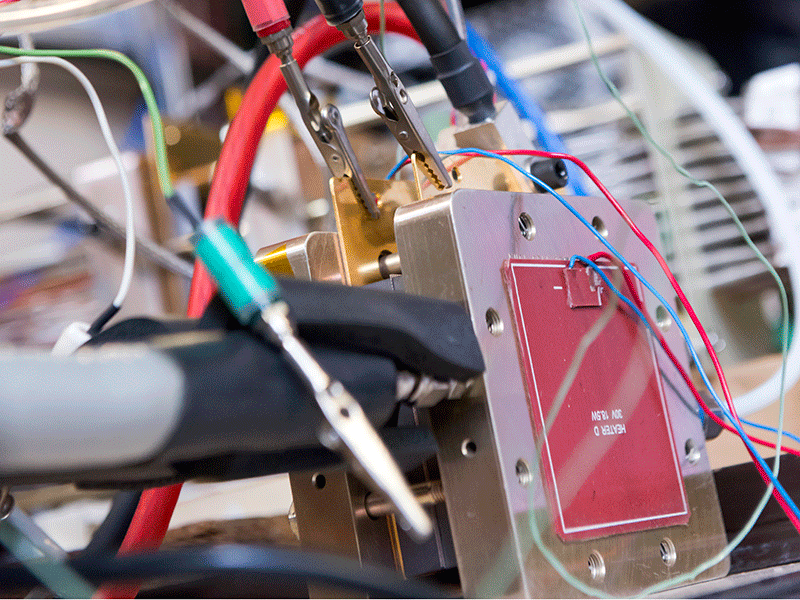
Single iron atoms, which are more reactive than bulk iron, are dispersed within an electrically conducting carbon matrix. The nitrogen acts as a binding site – a ligand – as four nitrogen atoms surround the central metal one and hold it in position.
Professor Anthony Kucernak, who is leading the work, says, ‘In terms of fuel cell power output under comparable operating conditions, our catalyst achieves about one-third the amount of power compared to a state-of-the-art platinum catalyst.
‘It has relatively low density and has a high porosity. The high porosity coupled to the electrical conductivity means we have also examined its use as an electrode substrate in lithium batteries.’
Kucernak continues, ‘Iron coordinated by nitrogen in an organic matrix has been known as an important biological structure in oxygen transport and respiration…hence researchers have studied model materials which contain similar structures such as iron porphyrins and iron phthalocyanines as potential catalysts. It was found by others that if you took these simple organic molecules and pyrolysed them, they lead to a more active material which contains the iron-nitrogen complex in an electrically conducting carbon matrix. What we have managed to do is fine tune the production of the active sites and massively increase their density – thus supercharging the resultant catalyst.’
The scientists use transmetallation, where one metal is swapped for another, to avoid iron clusters. The initial metal zinc is soaked in acid, then the zinc ions are replaced with protons, before these are replaced by iron ions. Two phases apparently results in better conversion than one, and does not take much longer than platinum catalyst manufacturing, says the team.
‘The nice thing about the transmetallation approach is that it allows us to swap different metals into the carbon matrix and we have already produced a range of catalysts with different metals instead of iron, including cobalt, manganese, copper, tin and antimony,’ Kucernak says.
The team is working to improve durability as catalyst performance wanes after 10-50 hours.
The method could be adapted for other catalysts, such as using atmospheric oxygen instead of chemical oxidants, and to remove contaminants from wastewater.
Sponsor Johnson Matthey is running tests for scaling up.