Ice-shedding coating put to the test
A 'fracture-controlled' spray-paint coating has outperformed current aerospace coatings in tests by Boeing.
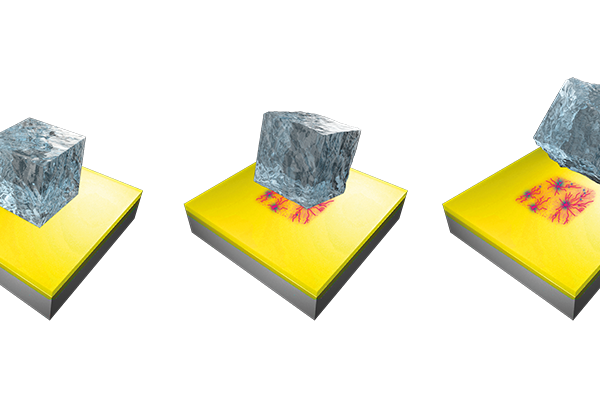
The aerospace giant tested the paint-like material made at the University of Houston, USA. They submitted it to erosive rain conditions at 385mph to check its durability and effectiveness in detaching ice quickly.
The principle of the material is that force is required to detach ice from a surface, and this inevitably leads to cracks forming. Over time, these cracks, or fractures, grow until the ice falls from the surface.
They claim the spray-paint coating demonstrates a quicker and more accurate process of ice detachment compared to other industry technologies.
'We developed a new concept in which, through material design, you can significantly accelerate the crack formation and growth and easily remove external objects from the surface,' explains Hadi Ghasemi, Cullen Associate Professor of Mechanical Engineering, in a paper published in Materials Horizons.
'This concept is implemented to develop materials that are highly durable and ice does not attach to these materials,' Ghasemi reports.
The laboratory work has focused on 'crack nucleation and fast growth at the interface between ice and the coating', and modifications were made before it was tested by Boeing in an industrial setting.
'We have divided the ice detachment into two stages and addressed each stage in our material in a specific phase.
'To accelerate crack nucleation at the specified coordinates, we introduced a soft low adhesion material as the second phase to the coating.'
The second step is crack propagation, which is a completely random process in an arbitrary material. In fracture-controlled material, we have introduced a third phase, which can be any inorganic material with high modulus of elasticity. By matching the modulus of elasticity of our coating to that of ice, the crack-tip does not tend to kink to either ice or the coating.'
In controlling the crack so it remains at the interface, Ghasemi says the researchers can 'save two orders of magnitude in detachment energy compared to the control single-phase material'. At the same time, this creates a composite coating that increases its durability to ice.
The material requires a certain viscosity and wetting properties if it is to work effectively as a spray-on coating. For this reason, it was important to develop a material that can demonstrate durability and icephobicity once it is sprayed and cured. The strength of the composite coating is its ability to withstand an applied load without failing and its elastic modulus, designed to be 9.1GPa, the same as ice, Ghasemi explains.
'While most durable icephobic materials are polymers that hardly exceed 100MPa, fracture-controlled surfaces have opened a new door for icephobic-coatings to have the same physical properties as your car paint, or even better, aircraft paint.'
To test the material, the team created an icing set-up in the laboratory to measure its ice adhesion. They also conducted a series of durability tests that included Taber abrasion, pencil hardness, cross-hatch resistance, pull-off adhesion and the application of a water jet.
'Only the samples that could perform the same or better than what is currently used in the industry were sent out for testing,' says Ghasemi.
Elemental Coatings has licensed the technology for commercial use and is currently undertaking pilot tests of the coating on wind turbines. According to the University researchers, ice build-up on wind turbines can lead to an 80% drop in power generation.