High-energy X-rays shine path to 3D-printed stainless steel
A 17-4 precipitation hardening (PH) stainless steel made by additive manufacturing (AM) matches the strength and corrosion-resistance of stainless steel, say researchers.
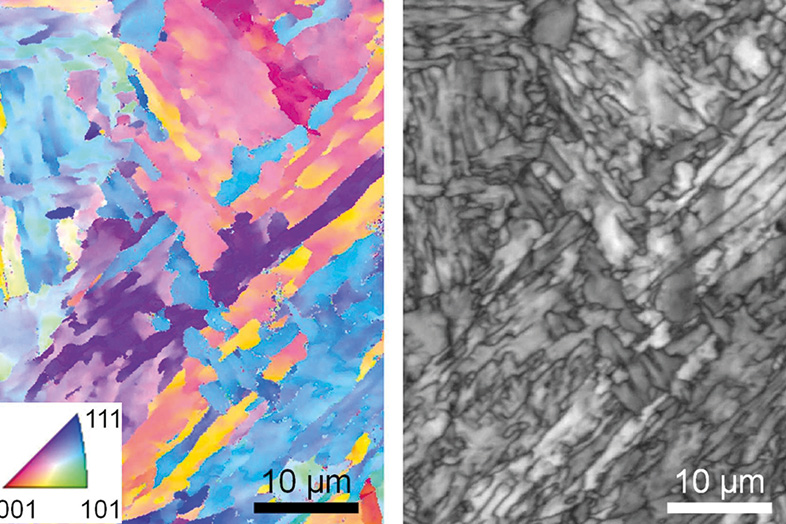
To date, researchers have struggled to fabricate high-strength and durable 17-4 precipitation hardening (PH) steel using 3D printing due to difficulties that are inherent in controlling the alloy’s martensitic microstructure, notes Fan Zhang, a Physicist at the National Institute of Standards and Technology (NIST).
'17-4 PH stainless steel is a remarkably strong and corrosion-resistant alloy that finds many applications in airliners, cargo ships, nuclear power plants, and other critical technologies. The design and fabrication flexibilities empowered by AM promise more high-value-added applications for 17-4 steels. These possibilities motivated us to study AM 17-4.'
This prompted NIST’s joint research with the University of Wisconsin-Madison and Argonne National Laboratory (ANL).
The researchers “smashed” high-energy X-rays into steel samples during 3D printing using an Advanced Photon Source (APS) at the ANL. This gave insight into changes in the crystal structure as the printing progresses, revealing how certain factors that are controlled – like the composition of the powdered metal – influence the process throughout.
'The phase transformation sequence in martensitic steel is complex,' notes Zhang, on the use of synchrotron X-ray diffraction or XRD.
'As the temperature decreases, it typically involves a high-temperature ferrite phase (б ferrite), a face-centred cubic austenite phase, and a body-centred-tetragonal martensite phase.
'Our initial high-speed diffraction measurements led us to conclude that the б ferrite in additive manufacturing (AM) 17-4 can be highly stable. This high degree of stability correlates with a lack of transformation from austenite to martensite.'
With this in mind, the researchers’ materials design criteria has focused on the initial liquid-to-solid transformation to minimise the formation of б ferrite and enable the austenite-to-martensite transformation.
However, steel’s 'liquid-to-solid phase transformation under AM conditions is often associated with a cooling rate between 104-106 K/s, making direct measurements difficult', adds co-author Professor Lianyi Chen, UW-Madison.
'The lack of validation data also presents a hurdle to establishing a rigorous computational framework that can accurately predict the phase transformation pathway.'
NIST and UW-Madison have spent years developing and using synchrotron-based materials characterisation tools, and the high-speed XRD-based approach, made possible by the APS, enables the team to capture the liquid-solid and solid-solid phase transformation at a high rate of 250Hz.
Zhang adds, 'We also showed that, over a wide range of cooling rates, say between 1,000 and 10 million degrees Celsius per second, our compositions consistently result in fully martensitic 17-4 PH steel.'
Before the material is ready for use in industry further research is needed for its fabrication at a larger-scale.
Chen says the alloy’s composition fits the allowed compositional range of conventional 17-4 steel, so less work is needed to meet the requirements.
'We demonstrated that the alloy maintains its martensitic character in the as-fabricated condition over a broad range of cooling rates, opening the possibility that it could be adopted by a range of AM technologies, from laser powder bed fusion to directed energy deposition,' he says.
One interesting aspect of the alloy is the copper-rich precipitates contained in the material’s as-fabricated state.
'These strengthening precipitates typically require ageing heat treatment for conventional cast/wrought 17-4,' explains Chen.
'Because of this characteristic, costly heat treatment procedures for PH could be eliminated... the unique microstructure features (e.g., high dislocation density) from rapid solidification under AM conditions can be maintained.'