Enhancing hearing without power
An electrically conductive membrane is being deployed to simulate cochlear hairs by converting sound waves into electrical pulses.
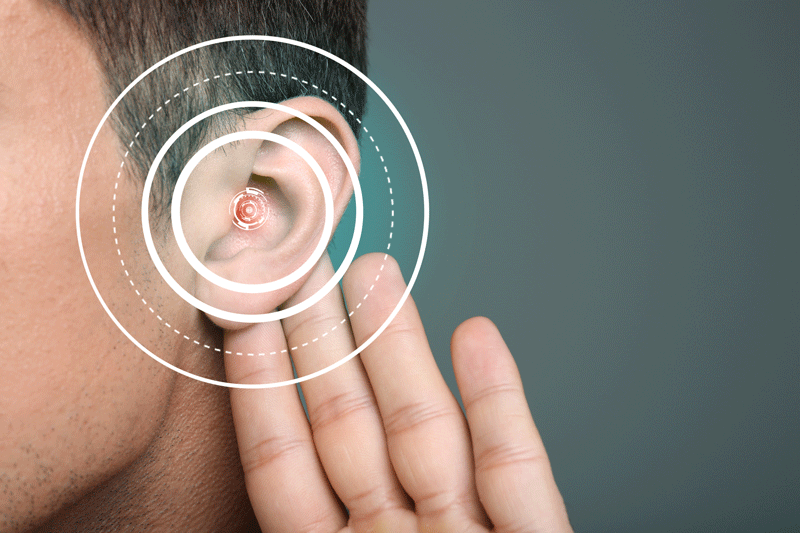
This could tackle hearing loss without the need for external power sources, say researchers at the Huazhong University of Science and Technology, China.
They claim the device can harvest the subtle vibration around the environment and convert the mechanical energy into electrical energy by coupling the piezo-triboelectric effect and electrostatic induction phenomenon. The device could be used for artificial cochlea and speech interactions.
The academics explain that current acoustic harvest devices are generally limited by weaknesses, such as relatively low output power density, high structure complexity and impracticable maintenance, which can be improved to a certain extent by using resonant cavities. Effective volume and portability are also restrained. In addition, they claim that these devices generally only perform well at the resonant frequency whose regulation can barely be achieved, which extensively obstructs further application.
Jiaqi Zheng, Doctoral Student at the University, explains that ‘implanting flexible sound-driven piezo-triboelectric nanogenerators (sound-driven PTNGs) as acoustic sensors to substitute the damaged hair cells of the human cochlea and provide an electrical response of the artificial auditory system’ could be a possible solution.
Zheng says, ‘The original structure of their sensing membranes was obtained by introducing dispersed barium titanate (BaTiO3) nanoparticles as the cores into porous poly(vinylidenefluoride-co-trifluoroethylene) (PVDF-TrFE) shells. The PVDF-TrFE and BaTiO3 are two kinds of widely used piezoelectric materials, which can enhance the performance of harvesting subtle mechanical vibrations into electricity.’
Zheng explains that the BaTiO3@SiO2 composite powder and PVDF-TrFE are uniformly dispersed in N, N-dimethylformamide and then dried from the stable solution by rotary evaporation.
Next, scientists remove the silicon dioxide shells with an alkaline solution. This step leaves behind a sponge-like membrane with spaces around the nanoparticles, allowing them to jostle around when hit by sound waves.
The output voltage is measured using a PCI eXtensions for Instrumentation (PXI) system, and the current and transferred charge quantity are recorded using an electrometer.
Zheng says, ‘The acoustic harvest principle that BaTiO3 nanocores bounce against porous PVDF-TrFE microshells and generate piezo-triboelectric potential is revealed by numerical modelling. In addition, the effect of the amount of added BaTiO3@SiO2 composite nanospheres, pore diameter, sensing membrane thickness, acoustic frequency, and sound intensity on the electrical properties of BaTiO3/PVDF-TrFE core−shell membranes is profoundly investigated and explained.’
Zheng continues, ‘By integrating piezoelectric ceramic particles with porous piezoelectric polymers into sound-driven PTNG devices, we greatly enhanced the short-circuit current density to 9.22mA/m2 and the open-circuit voltage to 15.24V under the measurement conditions of 170Hz, 120dB without a resonant cavity’ – frequencies that are within the range of most adult’s voices.
Finally, the researchers implanted the device inside a model ear and played a music file. They recorded the electrical output and converted it into a new audio file, which displays a strong similarity to the original version. The researchers say their self-powered device is sensitive to the wide acoustic range needed to hear most sounds and voices.
Zheng describes how fabrication contains steps of thermoforming, soaking in the alkali liquor and drying, which are large-scale processing methods.
‘Therefore, the technology is absolutely scalable. However, the scale of sealing and appliance remains unknown.’ The team is now looking to communicate with healthcare companies.