Correlation between crack complexity and material toughness
A Swiss Army knife and a confocal microscope was used to monitor 3D cracks, by the research team at EPFL in Switzerland.
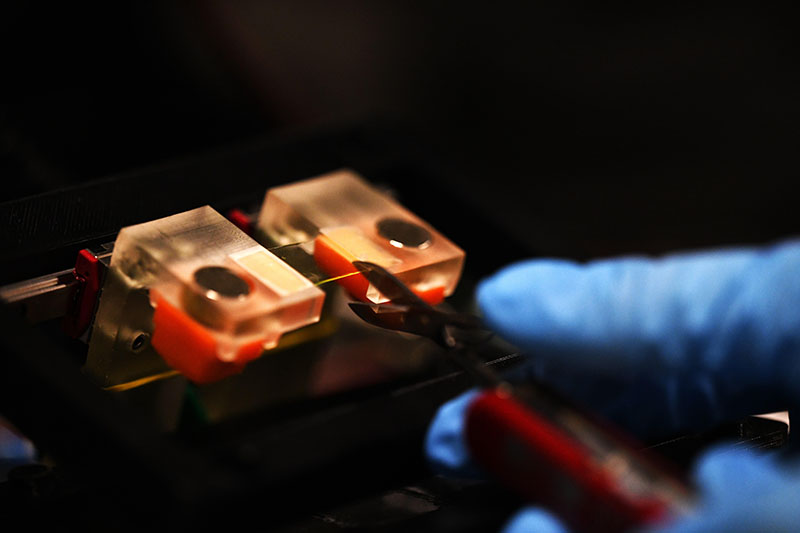
The experiments aim to correlate crack complexity and the forces the sample was exposed to when the crack emerged in situ.
Four very thin slices of different hydrogels were used to model brittle plastics, and an elastomer proxied rubber and silicone polymers.
A shearing action produced geometrically complex cracks in the hydrogel samples and a series of fluorescent images generated by the microscope were stacked to develop a 3D map of each fracture surface.
The results revealed that the strain energy required to drive the cracks was proportional to the lengths of the crack tips – i.e. the single point where a crack propagates.
This means a more complex 3D crack allows for more places of fracture as the crack advances, in turn this means that more energy is needed to increase its length.
A further experiment showed how, as a smooth crack meets a dent, the crack’s planar symmetry is broken and it stops. There is a large crack tip up to that point, meaning more energy is required to drive the crack past that point.
The team hopes the research could motivate new design approaches.
John Kolinski Tenure, Track Assistant Professor at the EPFL’s School of Engineering, says, ‘We now know that any geometric deviation from a planar crack front may lead to a mis-measurement – and potentially dangerous over-estimation – of material toughness’.
The paper is published in Nature Physics and is Open Access.